Astronauts Assemble Tools to Test Space Tech
March 1, 2019 | NASAEstimated reading time: 1 minute
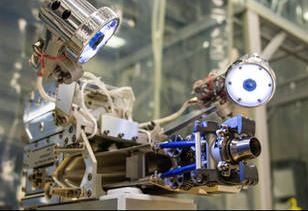
Technology drives exploration for future human missions to the Moon, Mars and beyond. For spacecraft to journey farther and live longer, we’ll need to store and transfer super-cold liquids used for fuel and life support systems in space. In December 2018, the Robotic Refueling Mission 3 (RRM3) launched to the International Space Station to do just that — transfer and store cryogenic fuel in space for the first time.
Some Assembly Required
Last week, astronauts Anne McClain of NASA and David Saint-Jacques of the Canadian Space Agency assembled the mission’s custom transfer tools and prepared them for installation on RRM3.
RRM3 consists of two primary parts: the main payload that houses the fluid, transfer lines and tanks and three external tools mounted on a pedestal. The three tools are the Multi-Function Tool 2, which operates smaller specialized tools to prepare for the fluid transfer, the Cryogen Servicing Tool 2, which uses a hose to connect the tank filled with liquid methane to the empty tank, and the Visual Inspection Poseable Invertebrate Robot 2, which uses a state-of-the-art robotic camera to make sure tools are properly positioned.
Shortly after RRM3’s arrival, the space station’s robotic arm Dextre affixed the main payload to the station. Meanwhile, the pedestal and tools made their way inside for assembly. With assembly complete, Dextre will soon attach the integrated hardware to the payload.
Looking Forward
With both parts together in one piece, RRM3 will begin operations in the next few months. Dextre will use the tools to transfer the cryogenic fuel to an empty tank and monitor the process. The technology demonstration will help make future exploration missions sustainable and prove that the whole is indeed greater than the sum of its parts.
RRM3 builds on the first two phases of International Space Station technology demonstrations that tested tools, technologies and techniques to refuel and repair satellites in orbit. It is developed and operated by the Satellite Servicing Projects Division at NASA’s Goddard Space Flight Center in Greenbelt, Maryland, and managed by the Technology Demonstration Missions program office within NASA’s Space Technology Mission Directorate.
Top: RRM3 tools (left to right) — Visual Inspection Poseable Invertebrate Robot 2, Cryogen Servicing Tool, Multi-Function Tool 2 — during ground testing; Bottom: Astronauts Anne McClain and David Saint-Jacques pose with the corresponding RRM3 tools aboard the International Space Station.
By Vanessa Lloyd
NASA's Goddard Space Flight Center, Greenbelt, Md.
Suggested Items
Forge Nano Secures $40M to Scale U.S. Battery Manufacturing and Commercial Semiconductor Equipment Businesses
05/02/2025 | Forge NanoForge Nano, Inc., a technology company pioneering domestic battery and semiconductor innovations, announced the successful close of $40 million in new funding.
MICROOLED Announces Partnership with Vortex Optics and Brand New US Headquarters
05/02/2025 | BUSINESS WIREMICROOLED Inc., the leading global supplier of AMOLED displays, is proud to announce their partnership with Vortex Optics to advance the development of high-performance weapon sights for optical sighting systems.
Indium Wins EM Asia Innovation Award
05/01/2025 | Indium CorporationIndium Corporation, a leading materials provider for the electronics assembly market, recently earned an Electronics Manufacturing (EM) Asia Innovation Award for its new high-reliability Durafuse® HR alloy for solder paste at Productronica China in Shanghai.
Elephantech, Logitech Together Drive Disruptive Electronics Innovation
05/01/2025 | ElephantechElephantech Inc. announced a groundbreaking collaboration with Logitech International to revolutionize peripherals manufacturing and the printed circuit board (PCB) industry.
Summit Interconnect Hollister Elevates PCB Prototyping with New TiTAN Direct Imaging System from Technica USA
05/01/2025 | Summit Interconnect, Inc.Summit Interconnect’s Hollister facility has recently enhanced its quick-turn PCB prototyping capabilities by installing the TiTAN PSR-H Direct Imaging (DI) system.