-
- News
- Books
Featured Books
- smt007 Magazine
Latest Issues
Current IssueWhat's Your Sweet Spot?
Are you in a niche that’s growing or shrinking? Is it time to reassess and refocus? We spotlight companies thriving by redefining or reinforcing their niche. What are their insights?
Moving Forward With Confidence
In this issue, we focus on sales and quoting, workforce training, new IPC leadership in the U.S. and Canada, the effects of tariffs, CFX standards, and much more—all designed to provide perspective as you move through the cloud bank of today's shifting economic market.
Intelligent Test and Inspection
Are you ready to explore the cutting-edge advancements shaping the electronics manufacturing industry? The May 2025 issue of SMT007 Magazine is packed with insights, innovations, and expert perspectives that you won’t want to miss.
- Articles
- Columns
- Links
- Media kit
||| MENU - smt007 Magazine
Two Full CFX Demo Lines at IPC APEX EXPO 2019
March 5, 2019 | Dan Feinberg, Technology Editor, I-Connect007Estimated reading time: 4 minutes
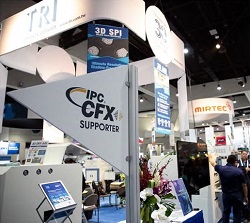
During IPC APEX EXPO, Editor Dan Feinberg spoke with David Bergman, IPC VP of standards and technology, about CFX, IPC’s Connected Factory Exchange software for machine-to-machine communication. With more than companies now supporting CFX, IPC set up two full lines for demonstration at the show.
Dan Feinberg: It’s good to see you again, David. Let’s talk about CFX. This is something that has been relatively new to me, but as I’ve looked at it over the past couple of days knowing that you were going to be here, it’s something that I find very interesting. And I see a tremendous amount of interest in it here at the show. Why don’t we start by assuming that there are a lot of people like me who don’t know what CFX is in detail.
David Bergman: It’s good to talk to you, Dan. At its basic level, CFX stands for the Connected Factory Exchange. What it’s intended to do is facilitate machine-to-machine and machine-to-manufacturing-execution-systems communication and become the common language between these systems. IPC CFX will serve as the foundation of Industry 4.0, the fourth industrial revolution. Industry 4.0 and smart factories are used somewhat interchangeably.
What the industry recognized was there had been multiple attempts over the years to facilitate machine-to-machine communication. IPC’s Board of Directors brought up 4.0 at one meeting about four years ago, I didn’t know anything about it. I read a lot—as much as I could find on Google—and it seemed like a marketing effort. When they said, “We have to get equipment companies all to agree to work together and have their machines speak the same language,” I thought, “There’s no way that’s going to happen.” Some companies have been working on 4.0 implementations, but they want you to buy everything from them.
Three years ago, we had a meeting in Las Vegas. I entered the meeting room, and approximately 80% of the world’s capital equipment companies were represented. They were serious about finding some way to work together. What had changed was the customer demand. The customer said, “This is needed. We’re not going to buy everything from you. We need to mix and match. It’s too difficult to get our machines to communicate with each other now, so we need a better way. We need a standard.”
Now, there were standards out there, but the committee concluded these were inadequate.
“We’re trying to do more. There’s more IoT coming and communication taking place. We need something that’s going to be somewhat future proof. How are we going to approach this?” They spent over a year looking at different formats because there are many communication standards out there. SEMI has one, IPC had CAMX—which the committee considered upgrading—so there were a number of formats out there. But the question was, “Will the options be sufficient? Which direction should we go?”
After a year and a half, they finally decided. They needed something secure because everybody was worried about data security in their factories. They also wanted a protocol that allowed customizing a piece of equipment such as adding a bar code reader or vision system or not. They wanted to have all these options to communicate to the system. The committee concluded to look at the approach as a series of building blocks or in other words to say, “I have building blocks. We’re going to create messages for all of these different blocks.”
The building block concept gained traction. We ended up selecting AMQP, which is a communication protocol that the banking industry uses. We felt it enabled significant security. AMQP also doesn’t require a broker, so every message doesn’t have to go through a central point. You can have machine-to-machine communication, which is perfect for the smart factory. If solder paste inspection equipment can talk to a solder paste printer, one can start to build feedback loops.
Feinberg: Or maybe even a soldering robot such as those being shown here.
Bergman: Correct. They felt that they were onto something. As they started to talk about individual messages, more companies became involved and the standard began to take form. The industry worked very hard on this. Some key events made this significantly easier than previous efforts. We had a company develop a software development kit (SDK). The SDK makes it easier for a company to output CFX messages—to go from their native machine language into CFX.
Our first CFX demonstration was at IPC APEX EXPO 2018 because we wanted to show CFX was possible. At that time, we managed to show 22 companies with 34–40 machines on the show floor pushing CFX messages to the cloud and back to attendees’ cellphones so they could monitor what was going on. If you went to one of the booths and they had a piece of machinery speaking CFX, it was running or simulating running. When they opened it, it stopped. They could monitor the status using their mobile device. All of those messages being pushed with CFX.
The success of the 2018 demo launch created even more interest. We’ve implemented more CFX demonstrations now, including in two in Europe and one in China. All along the process, we’ve added companies that have expressed interest. Right now, we have about 80 companies that are listed on our IPC-CFX website that indicate they support the CFX effort. Several large OEMs have allowed us to include their logo as they believe CFX will help their company implement Industry 4.0. So, we’re building awareness.
To read the full interview, which appeared in the Real Time with... IPC APEX EXPO 2019 Show & Tell magazine, click here.
Suggested Items
Driving Innovation: Direct Imaging vs. Conventional Exposure
07/01/2025 | Simon Khesin -- Column: Driving InnovationMy first camera used Kodak film. I even experimented with developing photos in the bathroom, though I usually dropped the film off at a Kodak center and received the prints two weeks later, only to discover that some images were out of focus or poorly framed. Today, every smartphone contains a high-quality camera capable of producing stunning images instantly.
Hands-On Demos Now Available for Apollo Seiko’s EF and AF Selective Soldering Lines
06/30/2025 | Apollo SeikoApollo Seiko, a leading innovator in soldering technology, is excited to spotlight its expanded lineup of EF and AF Series Selective Soldering Systems, now available for live demonstrations in its newly dedicated demo room.
Indium Corporation Expert to Present on Automotive and Industrial Solder Bonding Solutions at Global Electronics Association Workshop
06/26/2025 | IndiumIndium Corporation Principal Engineer, Advanced Materials, Andy Mackie, Ph.D., MSc, will deliver a technical presentation on innovative solder bonding solutions for automotive and industrial applications at the Global Electronics A
Fresh PCB Concepts: Assembly Challenges with Micro Components and Standard Solder Mask Practices
06/26/2025 | Team NCAB -- Column: Fresh PCB ConceptsMicro components have redefined what is possible in PCB design. With package sizes like 01005 and 0201 becoming more common in high-density layouts, designers are now expected to pack more performance into smaller spaces than ever before. While these advancements support miniaturization and functionality, they introduce new assembly challenges, particularly with traditional solder mask and legend application processes.
Knocking Down the Bone Pile: Tin Whisker Mitigation in Aerospace Applications, Part 3
06/25/2025 | Nash Bell -- Column: Knocking Down the Bone PileTin whiskers are slender, hair-like metallic growths that can develop on the surface of tin-plated electronic components. Typically measuring a few micrometers in diameter and growing several millimeters in length, they form through an electrochemical process influenced by environmental factors such as temperature variations, mechanical or compressive stress, and the aging of solder alloys.