-
- News
- Books
Featured Books
- pcb007 Magazine
Latest Issues
Current IssueIn Pursuit of Perfection: Defect Reduction
For bare PCB board fabrication, defect reduction is a critical aspect of a company's bottom line profitability. In this issue, we examine how imaging, etching, and plating processes can provide information and insight into reducing defects and increasing yields.
Voices of the Industry
We take the pulse of the PCB industry by sharing insights from leading fabricators and suppliers in this month's issue. We've gathered their thoughts on the new U.S. administration, spending, the war in Ukraine, and their most pressing needs. It’s an eye-opening and enlightening look behind the curtain.
The Essential Guide to Surface Finishes
We go back to basics this month with a recount of a little history, and look forward to addressing the many challenges that high density, high frequency, adhesion, SI, and corrosion concerns for harsh environments bring to the fore. We compare and contrast surface finishes by type and application, take a hard look at the many iterations of gold plating, and address palladium as a surface finish.
- Articles
- Columns
Search Console
- Links
- Media kit
||| MENU - pcb007 Magazine
Estimated reading time: 1 minute
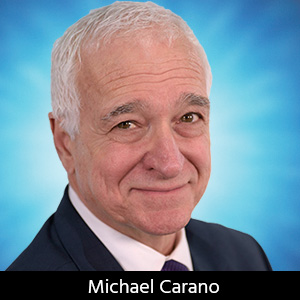
Contact Columnist Form
Trouble in Your Tank: Moving Into Microvias, Part 3
If we have learned anything about moving into HDI manufacturing, it is that it takes a great deal of thought and discipline to be successful. Unfortunately, as the following bullet points delineate, all too often, the fabricator underestimates the scope of HDI and what this manufacturing strategy truly entails.
Here are a few common mistakes to avoid:
- Bootstrapping it
- Designers treating microvia technology like small through-holes
- Being afraid to invest in process improvements
- Failing to bring the “total package” to the end user
- Continuing to do the same things for the last 30+ years
- Thinking HDI is only for smartphones
These are common mistakes that companies, engineers, and managers make, and are left wondering why they are not participating in the HDI market successfully. These misconceptions lead many firms to miss the HDI opportunity.
So, let’s frame up the strategic choices, and begin by discussing desmear and metallization. Desmear and Metalization Not a whole lot is different here. It is all about removing drill smear and any laser drill debris from the capture pad, and ensuring that subsequent plating adheres to the resin and copper surfaces. Essentially, you should strive for the quality of the plating. There is no evidence of plating adhesion issues or defects or debris at the capture pad.
However, notice the lateral resin removal where the capture pad meets the side wall of the vias. This can be controlled by adjusting the via formation parameters, desmear chemistry concentrations, and operating temperatures. Note the shape of the via. Yes, it is preferred for quality plating purposes to ensure a “V” shape to the blind via. If the via is more or less shaped like a coffee cup, plating is challenged.
If the via has a smaller diameter at the top, then widens as the opening leads down to the capture pad, uniform plating will be difficult if not impossible to achieve.
To read the full version of this article which originally appeared in the January issue of PCB007 Magazine, click here.
More Columns from Trouble in Your Tank
Trouble in Your Tank: Yield Improvement and ReliabilityTrouble in Your Tank: Causes of Plating Voids, Pre-electroless Copper
Trouble in Your Tank: Organic Addition Agents in Electrolytic Copper Plating
Trouble in Your Tank: Interconnect Defect—The Three Degrees of Separation
Trouble in Your Tank: Things You Can Do for Better Wet Process Control
Trouble in Your Tank: Processes to Support IC Substrates and Advanced Packaging, Part 5
Trouble in Your Tank: Materials for PWB Fabrication—Drillability and Metallization
Trouble in Your Tank: Supporting IC Substrates and Advanced Packaging, Part 5