True-Meaning Wearable Displays: Self-Powered, Washable and Wearable
March 21, 2019 | KAISTEstimated reading time: 2 minutes
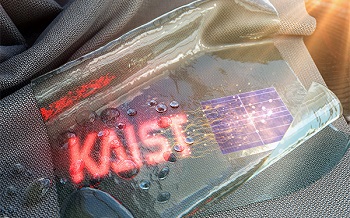
When we think about clothes, they are usually formed with textiles and have to be both wearable and washable for daily use; however, smart clothing has had a problem with its power sources and moisture permeability, which causes the devices to malfunction. This problem has now been overcome by a KAIST research team, who developed a textile-based wearable display module technology that is washable and does not require an external power source.
To ease out the problem of external power sources and enhance the practicability of wearable displays, Professor Kyung Cheol Choi from the School of Electrical Engineering and his team fabricated their wearing display modules on real textiles that integrated polymer solar cells (PSCs) with organic light emitting diodes (OLEDs).
PSCs have been one of the most promising candidates for a next-generation power source, especially for wearable and optoelectronic applications because they can provide stable power without an external power source, while OLEDs can be driven with milliwatts. However, the problem was that they are both very vulnerable to external moisture and oxygen. The encapsulation barrier is essential for their reliability. The conventional encapsulation barrier is sufficient for normal environments; however, it loses its characteristics in aqueous environments, such as water. It limits the commercialization of wearing displays that must operate even on rainy days or after washing.
To tackle this issue, the team employed a washable encapsulation barrier that can protect the device without losing its characteristics after washing through atomic layer deposition (ALD) and spin coating. With this encapsulation technology, the team confirmed that textile-based wearing display modules including PSCs, OLEDs, and the proposed encapsulation barrier exhibited little change in characteristics even after 20 washings with 10-minute cycles. Moreover, the encapsulated device operated stably with a low curvature radius of 3mm and boasted high reliability.
Finally, it exhibited no deterioration in properties over 30 days even after being subjected to both bending stress and washing. Since it uses a less stressful textile, compared to conventional wearable electronic devices that use traditional plastic substrates, this technology can accelerate the commercialization of wearing electronic devices. Importantly, this wearable electronic device in daily life can save energy through a self-powered system.
Professor Choi said, “I could say that this research realized a truly washable wearable electronic module in the sense that it uses daily wearable textiles instead of the plastic used in conventional wearable electronic devices. Saving energy with PSCs, it can be self-powered, using nature-friendly solar energy, and washed. I believe that it has paved the way for a ‘true-meaning wearable display’ that can be formed on textile, beyond the attachable form of wearable technology.”
Figure 1. Schematic and photo of a washable wearing display module
Figure 2. Cover page of Energy and Environmental Science
Suggested Items
Eiyu Electronics Launches Pre-Assembled Module Product Line to Simplify Sourcing for Embedded Projects
07/02/2025 | BUSINESS WIREEiyu Electronics Co., Ltd., a Hong Kong-based electronic component trading company, today announced the official launch of its pre-assembled module product line, designed to help engineers and procurement teams save time when sourcing complex modular components.
Kitron Receives EUR 4 Million Contract for Defense Airborne Radar Application
07/02/2025 | KitronKitron has received an order valued at EUR 4 million to produce electronics modules for airborne radar application, destined for the US market.
Horizon Sales Celebrates 10 Years of Exceptional Service by Sales Leader David Smith
07/02/2025 | Horizon SalesHorizon Sales, a premier manufacturers’ representative and distributor for the electronics assembly industry, is proud to announce that David Smith is celebrating 10 years with the company this month.
Symposium Review: Qnity, DuPont, and Insulectro Forge Ahead with Advanced Materials
07/02/2025 | Barb Hockaday, I-Connect007In a dynamic and informative Innovation Symposium hosted live and on Zoom on June 25, 2025, representatives from Qnity (formerly DuPont Electronics), DuPont, and Insulectro discussed the evolving landscape of flexible circuit materials. From strategic corporate changes to cutting-edge polymer films, the session offered deep insight into design challenges, reliability, and next-gen solutions shaping the electronics industry.
Wolfspeed Stock Soars After Filing for Chapter 11 Bankruptcy
07/01/2025 | I-Connect007 Editorial TeamOn July 1, Wolfspeed shares doubled following the company’s announcement on June 30 that it had filed for Chapter 11 bankruptcy protection.