-
- News
- Books
Featured Books
- smt007 Magazine
Latest Issues
Current IssueWhat's Your Sweet Spot?
Are you in a niche that’s growing or shrinking? Is it time to reassess and refocus? We spotlight companies thriving by redefining or reinforcing their niche. What are their insights?
Moving Forward With Confidence
In this issue, we focus on sales and quoting, workforce training, new IPC leadership in the U.S. and Canada, the effects of tariffs, CFX standards, and much more—all designed to provide perspective as you move through the cloud bank of today's shifting economic market.
Intelligent Test and Inspection
Are you ready to explore the cutting-edge advancements shaping the electronics manufacturing industry? The May 2025 issue of SMT007 Magazine is packed with insights, innovations, and expert perspectives that you won’t want to miss.
- Articles
- Columns
- Links
- Media kit
||| MENU - smt007 Magazine
Jennie Hwang: Get Ready for Disruptive Technologies
March 27, 2019 | Nolan Johnson, I-Connect007Estimated reading time: 10 minutes
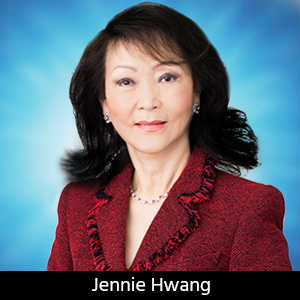
At IPC APEX EXPO 2019, I met with Dr. Jennie S. Hwang, a columnist, author, and all-around an expert in PCB assembly. We discussed some of the changes she has seen since joining the industry, and disruptive technologies that technologists we are going to have to face in the near future. Are you ready for the future?
Nolan Johnson: You have been one of our columnists for a long time with SMT007 Magazine. You were saying before that you might be our most tenured columnist.
Dr. Jennie Hwang: Yes, I started at age six (laughs). I’ve been in this industry for nearly four decades. I have observed and participated in its most dynamic, challenging, and rewarding times, and I am continuing to do so. I would be glad to share some of my retrospective and prospective thoughts about our industry. Surface-mount technology (SMT) has served as the backbone of electronic products and enabled the printed circuit board (PCB) manufacturing industry to thrive since PCBs are the brains of electronic products. SMT was implemented in the early ‘80s, give or take a couple of years, which made personal computers possible, sitting on the desktop, instead of occupying a whole room.
For the last three or four decades, the industry has had periods of abundant breakthroughs or drastic changes, as well as the periods of incremental changes and gradual advancements throughout the industry hierarchy in materials, design, equipment, processes, and manufacturing infrastructure. The 1987 Montreal Protocol on eliminating the ozone-depleting CFCs led to the development of no-clean chemistry for soldering, solder paste, and overall CFC-free cleaning. Also, the 2001 lead-free legislation initiated by EU ROHS that implemented lead-free electronics is another example of an event that led to major industry changes.
Concerning SMT, we experienced continued changes in packaging and component design, from PLCC and SOIC components to QFPs, fine-pitch QFPs, BGAs, fine-pitch BGAs, small form factor bottom-termination components, PoP, and other 2.5D and 3D packages. Thus, the evolution of new package designs affects solder paste formulation, the printer and stencil design, the equipment, and all of the accessories and supporting services, which involved a large number of suppliers. Accordingly, I have seen countless refinements and improvements and worked hard on them to serve the industry.
One of my professional development courses or industry lectures is under the title, “Emerging Technologies of the Electronic Industry.” In this lecture, one of the viewgraphs that I have often used to illustrate the industry from the manufacturing perspective is the hierarchy of the electronic industry, which includes semiconductors, IC packages and passive components, the module level, the PCB level, and the system level. SMT essentially focuses on the packages and components, the module level, and the PCB level, and to a lesser degree, the system level.
Practically speaking, the SMT industry is driven by the semiconductor sector. However, those phenomenal semiconductor chips would have no use if they couldn’t be reliably connected to the real world to deliver the intended performance. That’s where the critical role of SMT comes into play—to connect semiconductor chips to the real world to deliver performance through a PCB.
Johnson: I come from the IC design tools side. I wrote code as an engineer for for a major EDA company for a number of years, specializing in IC design. I think you’re exactly right. You need to have that conversation. “What can you do on the wafer? What can you do on the silicon? What package does that require to get it out in the real world, and how does that interface with the board?” You were just touching a little while ago on new product development. Where do you see us right now?
Hwang: With the incessant introduction of new packages and components, surface mount manufacturing has been relentlessly improved and refined. Today, we are moving into advanced manufacturing using IoT and AI to truly move into what I call intelligence-teaming manufacturing.
Johnson: We’re starting to talk about the dimensions now on the PCB that were the dimensions we designed to with integrated circuits when I was working in that industry. We have dramatically reduced the dimensions, and that changes what you need to do as far as fabrication on the boards; assembly drastically changes.
Hwang: Yes, the miniaturized dimensions drive all sectors of the industry—materials suppliers, PCB fabricators, SMT production operations, equipment manufacturers, and others.
Johnson: There’s a lot of attention at IPC APEX EXPO this year on CFX and Hermes, being able to pass data, having machine-to-machine interoperability. Where does that fit in your perspective? Is that disruptive or a refinement?
Hwang: The future factory is driven by the nascent Industry 4.0 and its ultimate goal to achieve intelligence-teaming manufacturing or operations in an integrated manner. In manufacturing—such as surface mount—reliability, agility, flexibility, efficiency, and desirable costs are the name of the game. However, becoming truly automated is a daunting task.
Johnson: That’s a provocative comment. Let’s go into that.
Hwang: We always say, “Surface mount is an advanced manufacturing technology,” and that is true. In many ways, it enables us to produce the electronics we have today. But true automation in the realm of Industry 4.0 must deliver all of the features I previously mentioned: high reliability, agility, flexibility, efficiency, and low cost. Over the years, surface mount equipment and processes—such as the printing, inspection, reflow—have advanced tremendously, which have possessed some level of automation. But if you look at surface mount as a whole operating system, it’s modulized and not integrated. We need to have advanced manufacturing, which means intelligence-teaming automation.
One caveat in automation is that it can produce a substandard product, which is certainly not an outcome that we want to have. Reliability, particularly for electronics, is critical. Even for consumer products, such as smartphones that are not mission critical, we still don’t want them to malfunction or “die” on us (except the battery).
Johnson: To pick up your point, I was amazed at the automotive executive forum. Someone commented that the field failure rate we have in phones is very good, but for automotive, they need to be something like two orders of magnitude lower in field failure rate. That’s the reliability that the industry needs to strive for. So, if someone is thinking that it’s challenging to get to cellphone requirements, that’s nothing compared to automotive.
Hwang: Right. In automotive, safety is the top priority, which is another level of reliability. We’re assessing from every functionality. For example, looking at the solder joint, I just taught a course yesterday titled, “Preventing Production Defects and Product Failure.” Interestingly, a lot of the attendees came from the automotive industry, military, and high-reliability electronics manufacturers. Obviously, they are concerned about potential product failure. So, we keenly care about the premise behind reliability. How you define reliability and look at it? Each industry has a different level of reliability they’re seeking or required to deliver. Not all products and industry sectors need the same level of reliability.
In my lecture, I always remind the audience that reliability is relative to your product service environment. Aerospace is different from the design of a dishwasher. Further, reliability is correlated to cost. How to optimize reliability to balance the performance features, manufacturability, cost, and time to market is a challenging question to address. After all, we produce electronics products where the business goal is often focused on introducing them to the market in a timely manner. Therefore, we must balance those factors. For a car, we want the electronics to perform whether it’s for engine control or the glove compartment. So, how do we produce that? It’s about making tradeoffs and reaching a balance with manufacturability, reliability and time to market. We can say, “We will design a most reliable product,” but if it will take another 15 years, that may make the product not viable anymore.
Page 1 of 2
Suggested Items
Driving Innovation: Direct Imaging vs. Conventional Exposure
07/01/2025 | Simon Khesin -- Column: Driving InnovationMy first camera used Kodak film. I even experimented with developing photos in the bathroom, though I usually dropped the film off at a Kodak center and received the prints two weeks later, only to discover that some images were out of focus or poorly framed. Today, every smartphone contains a high-quality camera capable of producing stunning images instantly.
Hands-On Demos Now Available for Apollo Seiko’s EF and AF Selective Soldering Lines
06/30/2025 | Apollo SeikoApollo Seiko, a leading innovator in soldering technology, is excited to spotlight its expanded lineup of EF and AF Series Selective Soldering Systems, now available for live demonstrations in its newly dedicated demo room.
Indium Corporation Expert to Present on Automotive and Industrial Solder Bonding Solutions at Global Electronics Association Workshop
06/26/2025 | IndiumIndium Corporation Principal Engineer, Advanced Materials, Andy Mackie, Ph.D., MSc, will deliver a technical presentation on innovative solder bonding solutions for automotive and industrial applications at the Global Electronics A
Fresh PCB Concepts: Assembly Challenges with Micro Components and Standard Solder Mask Practices
06/26/2025 | Team NCAB -- Column: Fresh PCB ConceptsMicro components have redefined what is possible in PCB design. With package sizes like 01005 and 0201 becoming more common in high-density layouts, designers are now expected to pack more performance into smaller spaces than ever before. While these advancements support miniaturization and functionality, they introduce new assembly challenges, particularly with traditional solder mask and legend application processes.
Knocking Down the Bone Pile: Tin Whisker Mitigation in Aerospace Applications, Part 3
06/25/2025 | Nash Bell -- Column: Knocking Down the Bone PileTin whiskers are slender, hair-like metallic growths that can develop on the surface of tin-plated electronic components. Typically measuring a few micrometers in diameter and growing several millimeters in length, they form through an electrochemical process influenced by environmental factors such as temperature variations, mechanical or compressive stress, and the aging of solder alloys.