-
- News
- Books
Featured Books
- pcb007 Magazine
Latest Issues
Current IssueSales: From Pitch to PO
From the first cold call to finally receiving that first purchase order, the July PCB007 Magazine breaks down some critical parts of the sales stack. To up your sales game, read on!
The Hole Truth: Via Integrity in an HDI World
From the drilled hole to registration across multiple sequential lamination cycles, to the quality of your copper plating, via reliability in an HDI world is becoming an ever-greater challenge. This month we look at “The Hole Truth,” from creating the “perfect” via to how you can assure via quality and reliability, the first time, every time.
In Pursuit of Perfection: Defect Reduction
For bare PCB board fabrication, defect reduction is a critical aspect of a company's bottom line profitability. In this issue, we examine how imaging, etching, and plating processes can provide information and insight into reducing defects and increasing yields.
- Articles
- Columns
- Links
- Media kit
||| MENU - pcb007 Magazine
Estimated reading time: 4 minutes
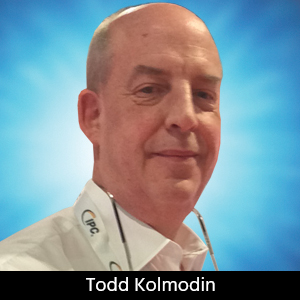
Confidence in Inspection
In the world of planning, manufacturing, and consumerism, we rely on the fact that what we design or purchase meets the requirements set forth. For a consumer, it really is a leap of faith that what we buy does what the label or manufacturer says it will do. For consumable goods, that is basically it; if it doesn’t work or do what it should, we don’t care—just return it.
However, in the second tier of this scenario are durable goods. For housing, construction, and other trades that have safety and health concerns, we rely on independent inspection to make sure things are being done correctly and to the standards for which the work must conform. An example could be home electrical or plumbing. The work is performed by licensed tradespeople but requires an inspection by a third party. This guarantees what was done is compliant with health and safety standards. If something is found to be incorrect, the third-party inspector will not pass the work performed until corrections are made. This stops the possibility of unsafe or incorrect work being hidden. Of course, in this case, the consumer cannot pick the third-party inspector or have a say in how the work is performed other than the plan or scope.
Now, in our third scenario, we have total control of the product. We design it and decide who manufactures it. We give the design and performance requirements and the final criteria. However, this is where the control falters. When we receive our product from the manufacturer, we have to assume that it was manufactured to our specifications. Sure, it may work, but will it work for the long term? It was inspected by the manufacturer and even has their stamp of approval, but that doesn’t tell us much.
Many quality accreditations state that an auditor cannot audit their own work. Remember, within a manufacturing facility, all employees work for the same company, the same monthly revenue goals, and the same deadlines. Here is where the game gets a little fuzzy. Imagine that the shipping deadline is 4:00 p.m., the delivery is already late, the customer is demanding their product, and the identification ink on the product is blurred. Now, someone in that manufacturing facility is going to make a call on whether they ship it anyway since it’s only ink and it’s close enough, or scrap it and make it right. Oh, did I mention it was the end of the month too? They are short on their revenue target.
How confident are you now?
This is where third-party inspection provides you the missing confidence. Many end-user companies require in-process or out-of-the-box inspections. These are cases where an end user dispatches one of their own inspectors to physically go to the manufacturing plant and inspect their product in one of the two aforementioned ways. This inspection process puts the burden on the end-use customer because they must incur the cost of their inspector traveling to the manufacturing plant. However, this does satisfy the customer since they do inspect their own product to audit it is manufactured properly. Again, this is not the ultimate solution.
Independent, third-party inspection is where all the pieces fall into place. The third party must remain neutral to either side. The job of third-party inspection is to provide an unbiased review of the customer requirements versus the final product manufactured. This inspection can include both physical and functional criteria. In the instance of PCBs, this can be cosmetic, dimensional, electrical, and in some cases, functional. In this neutral playing field, the customer provides the requirements and/or inspection criteria to the third-party inspection entity as well as the procurement order to the manufacturer, which also includes the deliverables.
When the product has completed its manufacturing cycle, it is sent to the third-party inspection entity. This entity may be local to the manufacturer or located elsewhere. When the product arrives at the third-party inspection entity, it is given an unbiased review based on the requirements of the end-use customer as previously described. When the inspection is complete, the product is either certified to meet the customer requirements or is found to be non-conforming. The strong point here is that the review is unbiased, and the results are binary—either conforming or non-conforming based on the requirements set forth as deliverables.
The customer is then briefed on the results and provided objective evidence regarding any non-conformances. If all product is conforming, it is then shipped to the customer or duly designated receiver. Non-conformance issues require resolution, and after review, the customer either accepts the product under an authorized deviation or the product is returned to the manufacturer for resolution and/or disposition. There is no grey area with third-party inspection. Ultimately, the product is shipped conforming to the end-use customer, or it is returned non-conforming to the manufacturer. Another key point is that some referee testing can be accomplished. These may be specific to plating (latent voiding), TDR, and other tests that may not be possible at the manufacturing facility.
Conclusion
With our earlier example regarding third-party inspection in the construction industry, which is required, we see the growing acceptance and requirement of third-party inspection in many areas of the manufacturing industry. This is becoming more prevalent with military, aerospace, and medical. When high reliability is an absolute necessity, the requirement of independent inspection also becomes the necessity.
Todd Kolmodin is VP of quality for Gardien Services USA and an expert in electrical test and reliability issues.
Editor's Note: This article originally appeared in the March 2019 issue of PCB007 Magazine.
More Columns from Testing Todd
Testing Todd: Why 4-wire Kelvin?Testing Todd: Why TDR?
Testing Todd: Positivity Boosts Employee Morale
Testing Todd: Preparing Employees for the Long Haul
Testing Todd: Where Can We Improve?
Testing Todd: Turning Into the Wind
Testing Todd: Coming Back to Life—Design Recovery
Testing Todd: Decision Time—Invest or Delegate?