Functional Thin-Film Structures for Integrated Radar Sensors
May 3, 2019 | Fraunhofer IBMTEstimated reading time: 3 minutes
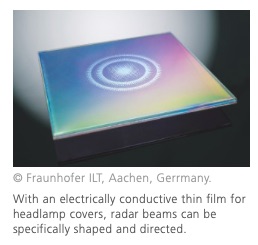
It is only an inconspicuous piece of paper, but it is an important milestone for autonomous driving: At the end of 2018 the three partners from the joint research project RadarGlass applied for a patent for an innovative radar system. The Fraunhofer Institute for Laser Technology ILT from Aachen, the Fraunhofer Institute for Organic Electronics, Electron Beam and Plasma Technology FEP from Dresden and the Institute of High Frequency Technology IHF of RWTH Aachen University have developed a coating process chain that enables radar sensors to be integrated in car headlights. After almost two years in development they have manufactured a working prototype.
With an electrically conductive thin film for headlamp covers, radar beams can be specifically shaped and directed.
Completely autonomous vehicles pose an enormous challenge for sensor technology because, in principle, the supporting system must hear, see and feel better than humans. While the corresponding sensors are available—in particular since a large number of assistance systems have already been installed—developers are always faced with the question of where they can be placed best. In the case of radar sensors, it makes sense to install them in the front headlamps. “It's the perfect position because they completely cover the near and far range and allow you to look to the side,“ explains Dipl.-Phys. Patrick Gretzki, scientist in the Micro and Nano Structuring group at Fraunhofer ILT. “Since the light source generates so much heat, the sensors are also always free of snow and water even under harsh weather conditions.”
Coating Directs the Radar Beam
The three institutes cover all the necessary expertise from developing a suitable coating system to designing the high-frequency components all the way to precisely producing them with laser radiation. Together, they have developed a functional, electrically conductive thin film placed inside the headlamp cover, a film that can be used to specifically shape and direct the radar beam. The layer can manipulate the beam selectively depending on the type of application: In order to detect and recognize pedestrians, the radar beam is directed to the side. Like an eye, the beam can also be focused on the near or far range. The RadarGlass project is investigating which thin-film system can be used to control radar waves with low loss and without limiting the main purpose of the headlamp.
Precise Laser-based Structuring in the 10 µm Range
In joint development work, the partners have developed a coating system that meets the criteria for headlamp and radar use and that can be applied and structured on typical automobile headlamps.
In order to guide and shape the radar beam, small patches of the coating have to be structured. These patches act as small antennas for the radar waves. For that, a laser process was developed at Fraunhofer ILT to shape the antenna elements. In a preliminary study, the structuring of antenna elements was utilized to make it possible for high-frequency waves to pass through thermal glazing selectively, e. g. the glazing can be used for WLAN and mobile radio networks. The laser-manufactured structures—with a resolution of up to 10 µm—are much more precise than any conventional printing process. Moreover, conventional lithography processes require more steps in the process chain and are limited to flat (or slightly curved) surfaces, two hindrances overcome by the new laser-based process.
Implementation Planned with Industrial Partners
With the help of simulations, the partners are developing structures for the targeted manipulation of radar waves in the range around 77 GHz. Using demonstrators, they will show the functionality of the technology and then continue to develop it. “With the demonstrators, we have shown that we can simulate, design and produce the antennas in such a way that they fulfil the desired properties,” says Gretzki. “Currently, we are already presenting the solution to industry representatives in order to tackle further steps to exploit the process. In the next phase of the project, we will install the solution in real headlamps.”
Suggested Items
2025 ASEAN IT Spending Growth Slows to 5.9% as AI-Powered IT Expansion Encounters Post-Boom Normalization
06/26/2025 | IDCAccording to the IDC Worldwide Black Book: Live Edition, IT spending across ASEAN is projected to grow by 5.9% in 2025 — down from a robust 15.0% in 2024.
DownStream Acquisition Fits Siemens’ ‘Left-Shift’ Model
06/26/2025 | Andy Shaughnessy, I-Connect007I recently spoke to DownStream Technologies founder Joe Clark about the company’s acquisition by Siemens. We were later joined by A.J. Incorvaia, Siemens’ senior VP of electronic board systems. Joe discussed how he, Rick Almeida, and Ken Tepper launched the company in the months after 9/11 and how the acquisition came about. A.J. provides some background on the acquisition and explains why the companies’ tools are complementary.
United Electronics Corporation Advances Manufacturing Capabilities with Schmoll MDI-ST Imaging Equipment
06/24/2025 | United Electronics CorporationUnited Electronics Corporation has successfully installed the advanced Schmoll MDI-ST (XL) imaging equipment at their advanced printed circuit board facility. This significant technology investment represents a continued commitment to delivering superior products and maintaining their position as an industry leader in precision PCB manufacturing.
Insulectro & Dupont Host Technology Symposium at Silicon Valley Technology Center June 25
06/22/2025 | InsulectroInsulectro, the largest distributor of materials for use in the manufacture of PCBs and printed electronics, and DuPont, a major manufacturer of flex laminates and chemistry, invite fabricators, OEMS, designers, and engineers to attend an Innovation Symposium – Unlock the Power - this Wednesday, June 25, at DuPont’s Silicon Valley Technology Center in Sunnyvale, CA.
OKI, NTT Innovative Devices Establish Mass Production Technology for High-Power Terahertz Devices by Heterogeneous Material Bonding
06/21/2025 | BUSINESS WIREOKI, in collaboration with NTT Innovative Devices Corporation, has established mass production technology for high-power terahertz devices using crystal film bonding (CFB) technology for heterogeneous material bonding to bond indium phosphide (InP)-based uni-traveling carrier photodiodes (UTC-PD) onto silicon carbide (SiC) with excellent heat dissipation characteristics for improved bonding yields.