-
- News
- Books
Featured Books
- smt007 Magazine
Latest Issues
Current IssueSupply Chain Strategies
A successful brand is built on strong customer relationships—anchored by a well-orchestrated supply chain at its core. This month, we look at how managing your supply chain directly influences customer perception.
What's Your Sweet Spot?
Are you in a niche that’s growing or shrinking? Is it time to reassess and refocus? We spotlight companies thriving by redefining or reinforcing their niche. What are their insights?
Moving Forward With Confidence
In this issue, we focus on sales and quoting, workforce training, new IPC leadership in the U.S. and Canada, the effects of tariffs, CFX standards, and much more—all designed to provide perspective as you move through the cloud bank of today's shifting economic market.
- Articles
- Columns
- Links
- Media kit
||| MENU - smt007 Magazine
Ultra-Clean Fabrication Platform Produces Nearly Ideal 2D Transistors
May 20, 2019 | Columbia EngineeringEstimated reading time: 3 minutes
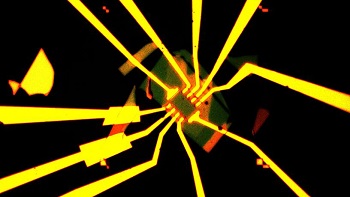
Semiconductors, which are the basic building blocks of transistors, microprocessors, lasers, and LEDs, have driven advances in computing, memory, communications, and lighting technologies since the mid-20th century. Recently discovered two-dimensional (2D) materials, which feature many superlative properties, have the potential to advance these technologies, but creating 2D devices with both good electrical contacts and stable performance has proved challenging.
Image Caption: A Hall-bar device structure (see inset) is wire-bonded to a 16-pin chip-carrier. The chip-carrier allows for extensive electrical characterization of the device at both low temperatures and high magnetic fields.
Researchers at Columbia Engineering report that they have demonstrated a nearly ideal transistor made from a two-dimensional material stack—with only a two-atom-thick semiconducting layer—by developing a completely clean and damage-free fabrication process. Their method shows vastly improved performance compared to 2D semiconductors fabricated with a conventional process, and could provide a scalable platform for creating ultra-clean devices in the future.
“Making devices out of 2D materials is a messy business,” says James Teherani, assistant professor of electrical engineering. “Devices vary wildly from run to run and often degrade so fast that you see performance diminish while you’re still measuring them.”
Having grown tired of the inconsistent results, Teherani’s team set out to develop a better way to make stable devices. “So,” he explains, “we decided to separate the pristine device from the dirty fabrication processes that lead to variability.”
As shown in this new study, Teherani and his colleagues developed a two-step, ultra-clean nanofabrication process that separates the “messy” steps of fabrication—those that involve “dirty” metallization, chemicals, and polymers used to form electrical connections to the device—from the active semiconductor layer. Once they complete the messy fabrication, they could pick up the contacts and transfer them onto the clean active device layer, preserving the integrity of both layers.
“The thinness of these semiconductors is a blessing and a curse,” says Teherani. “While the thinness allows them to be transparent and to be picked up and placed wherever you want them, the thinness also means there's nearly zero volume—the device is almost entirely surface. Because of this, any surface dirt or contamination will really degrade a device.”
Currently, most devices are not encapsulated with a layer that protects the surface and contacts from contamination during fabrication. Teherani’s team showed that their method can now not only protect the semiconductor layer so that they don't see performance degradation over time, but it can also yield high performance devices.
Teherani collaborated with Jim Hone, Wang Fong-Jen Professor of Mechanical Engineering, making use of the fabrication and analysis facilities of the Columbia Nano Initiative and the National Science Foundation-funded Materials Research Science and Engineering Center at Columbia. The team made the transferred contacts from metal embedded in insulating hexagonal boron nitride (h-BN) outside a glovebox and then dry-transferred the contact layer onto the 2D semiconductor, which was kept pristine inside a nitrogen glovebox. This process prevents direct-metallization-induced damage while simultaneously providing encapsulation to protect the device.
The fabrication process for transferred contacts that yield nearly ideal transistors. Transferred contacts prevent contamination and damage to the 2D semiconductor that occur during fabrication of conventional contacts.
Video on the differences between 2D and 3D materials
Video on the step-by-step nanofabrication of 2D material stacks
Now that the researchers have developed a stable, repeatable process, they are using the platform to make devices that can move out of the lab into real-world engineering problems.
“The development of high performance 2D devices requires advances in the semiconductor materials from which they are made,” Teherani adds. “More precise tools like ours will enable us to build more complex structures with potentially greater functionality and better performance.”
About Columbia Engineering
Columbia Engineering, based in New York City, is one of the top engineering schools in the U.S. and one of the oldest in the nation. Also known as The Fu Foundation School of Engineering and Applied Science, the School expands knowledge and advances technology through the pioneering research of its more than 220 faculty, while educating undergraduate and graduate students in a collaborative environment to become leaders informed by a firm foundation in engineering. The School’s faculty are at the center of the University’s cross-disciplinary research, contributing to the Data Science Institute, Earth Institute, Zuckerman Mind Brain Behavior Institute, Precision Medicine Initiative, and the Columbia Nano Initiative. Guided by its strategic vision, “Columbia Engineering for Humanity,” the School aims to translate ideas into innovations that foster a sustainable, healthy, secure, connected, and creative humanity.
Testimonial
"Advertising in PCB007 Magazine has been a great way to showcase our bare board testers to the right audience. The I-Connect007 team makes the process smooth and professional. We’re proud to be featured in such a trusted publication."
Klaus Koziol - atgSuggested Items
Advint and SanRex Expand High-Performance DC Rectifier Access for North American PCB Fabricators
08/12/2025 | Advint IncorporatedAdvint Incorporated has entered a strategic partnership with SanRex Corporation, enhancing access to industrial-grade DC rectifiers for the US printed circuit board industry. With a legacy of power innovation and performance across the globe, SanRex rectifiers are available through Advint’s proficient distribution network.
Advint and Sayron Bring Advanced Rectifier Solutions to High-Reliability PCB Manufacturers
08/01/2025 | Advint IncorporatedAdvint Incorporated has partnered with Sayron, a leading global rectifier manufacturer, to supply cutting-edge IGBT-based DC rectifiers to high-performance PCB manufacturers across North America and beyond. Sayron’s precision-engineered rectifiers align with the stringent requirements of advanced PCB processes.
Trouble in Your Tank: Metallizing Flexible Circuit Materials—Mitigating Deposit Stress
08/04/2025 | Michael Carano -- Column: Trouble in Your TankMetallizing materials, such as polyimide used for flexible circuitry and high-reliability multilayer printed wiring boards, provide a significant challenge for process engineers. Conventional electroless copper systems often require pre-treatments with hazardous chemicals or have a small process window to achieve uniform coverage without blistering. It all boils down to enhancing the adhesion of the thin film of electroless copper to these smooth surfaces.
Magnalytix’s Dr. Mike Bixenman to Guide PDC at SMTA High-Reliability Cleaning and Conformal Coating Conference
07/31/2025 | MAGNALYTIXMagnalytix, providing real-time reliability solutions for electronics manufacturing, is excited to announce that Dr. Mike Bixenman will present the professional development course “The Effects of Flux Residues and Process Contamination on the Reliability of the Electronic Assembly” on Wednesday, Aug. 13 at 9:00 AM CST to open the second day of the STMA High-Reliability Cleaning and Conformal Coating Conference.
Setting Design Constraints Effectively
07/31/2025 | Stephen V. Chavez, Siemens EDAPCB design requires controlling energy within the medium of a PCB. The manner in which we control the chaos of energy is by implementing and utilizing physical and electrical rules, known as constraints, along with a specific structure and material(s) that make up what is known as the foundation of the design. These rules govern everything within the PCB structure and generally fall into two camps: performance and manufacturability. Setting this foundation correctly is extremely important and the key to success.