-
- News
- Books
Featured Books
- pcb007 Magazine
Latest Issues
Current IssueThe Hole Truth: Via Integrity in an HDI World
From the drilled hole to registration across multiple sequential lamination cycles, to the quality of your copper plating, via reliability in an HDI world is becoming an ever-greater challenge. This month we look at “The Hole Truth,” from creating the “perfect” via to how you can assure via quality and reliability, the first time, every time.
In Pursuit of Perfection: Defect Reduction
For bare PCB board fabrication, defect reduction is a critical aspect of a company's bottom line profitability. In this issue, we examine how imaging, etching, and plating processes can provide information and insight into reducing defects and increasing yields.
Voices of the Industry
We take the pulse of the PCB industry by sharing insights from leading fabricators and suppliers in this month's issue. We've gathered their thoughts on the new U.S. administration, spending, the war in Ukraine, and their most pressing needs. It’s an eye-opening and enlightening look behind the curtain.
- Articles
- Columns
- Links
- Media kit
||| MENU - pcb007 Magazine
Electrolytic Plating: Filling Vias and Through-holes
May 28, 2019 | M. Özkök, S. Lamprecht, A. Özkök, D. Akingbohungbe, and M. Dreiza, Atotech Deutschland Gmbh; and A. Stepinski, Greensource FabricationEstimated reading time: 4 minutes
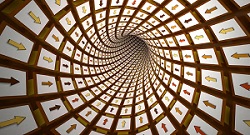
The electronics industry is further progressing in terms of smaller, faster, smarter, and more efficient electronic devices. This continuously evolving environment caused the development of various electrolytic copper processes for different applications over the past several decades.
This article describes the reasons for development and a roadmap of dimensions for copper-filled through-holes, microvias, and other copper-plated structures on PCBs. It will also discuss aspect ratios, dimensions, and results of plated through-holes used today in high-volume manufacturing for microvia and throughhole filling with electroplated copper. Furthermore, this article will also show feasibility studies of new electroplated structures for future applications, such as copper pillar plating on IC substrates.
Four Main Drivers
Four main drivers forced the chemical supply industry to introduce new electrolytic copper processes with the new feature of “filling” capability over the years. The first driver is the continuous miniaturization of electronics. The first blind microvias were introduced with HDI technology in the late 1980s and early 1990s. In 1996, the IC substrate market started to fill the microvias.
“Plugging” technologies were introduced to stack the microvias to save space or create via-in-pad structures. This plugging technology with conductive paste is very expensive because of the additional process steps required. In addition, this technology faced several disadvantages, such as “blow out,” outgassing, smear, and other quality concerns. To achieve the necessary miniaturization benefits, the industry has been leaning towards the completely copper filled blind microvia rather than a plugged microvia as the leading edge solution. Today, copper-filled microvias are the standard for almost all HDI PCB manufacturers.
The second driver is the thermal management on a substrate. One source said it this way:
“As the power and packing density of electronic components increase, the amount of waste heat generated in a small space also rises greatly. This results in dangerously high temperatures, and thus increases the failure risk of electronic devices. Today, 55% of electronic component failures are caused by increased temperatures alone.”
Solutions were needed to integrate features with high thermal conductivity to manage the heat transfer on the substrates from one side to the other to minimize hot spots on the electronic devices over a lifetime. Higher-performing chips tend to generate local hot spots, resulting in material degradation and premature field failure. Integration of thermal vias in high-performance electronics can minimize the occurrence of hot spots; therefore, their utilization in the industry has become more widespread.
In the beginning, thermal vias were nothing more than standard conformal vias, but the thermal conductivity was not good enough. Following that, plugging pastes were introduced to enhance the thermal conductivity of a standard through-hole. But in this case, similar disadvantages of plugging appeared. Meanwhile, complete copper-filled through-holes were realized in 2006 by bridge plating or X-plating technology.
Today, completely copper-filled through-hole structures are at the leading edge of technology for thermal via structures because copper has almost the best thermal conductivity—and it has to be plated, nonetheless.
The third driver is signal frequency. Electronic signal frequencies in an electronic package or inside of a PCB are increasing over time and continue to do so. Stacked microvias and fan-out vias are becoming more and more of a disadvantage for the transmission of high-frequency signals due to creating resistances at high frequencies. Thus, the push of high-frequency applications further increased the demand for technologies like copper-filled through holes. Right now, 5G infrastructure is already using the copper-filled through-hole technology in the field of smartphones.
Figure 1: Patented “SuperFilling” technology.
The fourth driver, especially for through-hole filling, is the quality-and-yield aspect. The alternatives for electroplated copper-filled through-holes require many additional process steps or new materials, such as plugging paste. Each of these additional process steps or materials introduces a variety of risks and manufacturing problems, resulting in a lower yield. Therefore, the “one-step” solution to fill through-holes with copper is the preferred solution without introducing new materials into the PCB.
Microvia Filling With Copper
The filling of microvias with copper was established as a standard in PCB HDI production more than 20 years ago. For example, there was the introduction of supervia filling technology with very low plated-copper thickness on the surface (Figure 1).
Figure 2: Plugged and capped microvia.
Meanwhile, the copper filling of microvias replaced many other filling technologies, such as plugging and capping realized by paste printing and overplating with copper (Figure 2). Both technologies—plugging and capping and copper- filled microvias—enable the so-called via-in-pad structure, which has the advantage for PCB designers. The advantages of the via-in-pad designs are also useful for high-speed designs.
Additionally, copper-filled microvias have significant advantages over plugging technology. For instance, the material inside the microvia is copper while other materials have the potential to outgas or introduce different CTE values. Moreover, voids in copper-filled microvias are far less common than with poorly controlled conventional plugging methods.
The development and introduction of copper-filled microvias opened the door to introduce any layer HDI technology, which enables copper-filled through-holes by stacking the copper-filled microvias. This kind of feature enables HDI board designers the flexibility to create complex signal paths through the PCB by just using copper filled microvias.
Today, almost all critical dimensions of microvias may be filled inclusion-free with copper.
To read the full article, which was published in the April 2019 issue of PCB007 Magazine, click here.
Suggested Items
Trump Copper Tariffs Spark Concern
07/10/2025 | I-Connect007 Editorial TeamPresident Donald Trump stated on July 8 that he plans to impose a 50% tariff on copper imports, sparking concern in a global industry whose output is critical to electric vehicles, military hardware, semiconductors, and a wide range of consumer goods. According to Yahoo Finance, copper futures climbed over 2% following tariff confirmation.
Happy’s Tech Talk #40: Factors in PTH Reliability—Hole Voids
07/09/2025 | Happy Holden -- Column: Happy’s Tech TalkWhen we consider via reliability, the major contributing factors are typically processing deviations. These can be subtle and not always visible. One particularly insightful column was by Mike Carano, “Causes of Plating Voids, Pre-electroless Copper,” where he outlined some of the possible causes of hole defects for both plated through-hole (PTH) and blind vias.
Trouble in Your Tank: Can You Drill the Perfect Hole?
07/07/2025 | Michael Carano -- Column: Trouble in Your TankIn the movie “Friday Night Lights,” the head football coach (played by Billy Bob Thornton) addresses his high school football team on a hot day in August in West Texas. He asks his players one question: “Can you be perfect?” That is an interesting question, in football and the printed circuit board fabrication world, where being perfect is somewhat elusive. When it comes to mechanical drilling and via formation, can you drill the perfect hole time after time?
The Evolution of Picosecond Laser Drilling
06/19/2025 | Marcy LaRont, PCB007 MagazineIs it hard to imagine a single laser pulse reduced not only from nanoseconds to picoseconds in its pulse duration, but even to femtoseconds? Well, buckle up because it seems we are there. In this interview, Dr. Stefan Rung, technical director of laser machines at Schmoll Maschinen GmbH, traces the technology trajectory of the laser drill from the CO2 laser to cutting-edge picosecond and hybrid laser drilling systems, highlighting the benefits and limitations of each method, and demonstrating how laser innovations are shaping the future of PCB fabrication.
Day 2: More Cutting-edge Insights at the EIPC Summer Conference
06/18/2025 | Pete Starkey, I-Connect007The European Institute for the PCB Community (EIPC) summer conference took place this year in Edinburgh, Scotland, June 3-4. This is the third of three articles on the conference. The other two cover Day 1’s sessions and the opening keynote speech. Below is a recap of the second day’s sessions.