-
- News
- Books
Featured Books
- smt007 Magazine
Latest Issues
Current IssueSupply Chain Strategies
A successful brand is built on strong customer relationships—anchored by a well-orchestrated supply chain at its core. This month, we look at how managing your supply chain directly influences customer perception.
What's Your Sweet Spot?
Are you in a niche that’s growing or shrinking? Is it time to reassess and refocus? We spotlight companies thriving by redefining or reinforcing their niche. What are their insights?
Moving Forward With Confidence
In this issue, we focus on sales and quoting, workforce training, new IPC leadership in the U.S. and Canada, the effects of tariffs, CFX standards, and much more—all designed to provide perspective as you move through the cloud bank of today's shifting economic market.
- Articles
- Columns
- Links
- Media kit
||| MENU - smt007 Magazine
Hermes Standard to Replace SMEMA—Available with Rehm
May 29, 2019 | Rehm Thermal SystemsEstimated reading time: 3 minutes
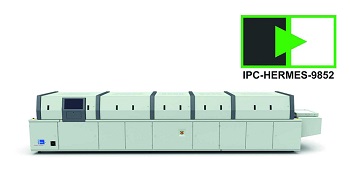
Adaptability to demand, efficiency, simplicity, networking—these are the defining buzzwords for today’s industry. In a smart factory it is essential for the entire production system to be networked and able to access all process and assembly data at any time. It is particularly important for SMT lines made up of systems from different manufacturers to guarantee that such networking also remains independent of the manufacturer. All of this can be achieved easily with the “Hermes Standard”. For the convection soldering system VisionXP+, Rehm Thermal Systems offers two variants with “The Hermes Standard”.
Image Caption: A picture of the convection soldering system VisionXP+ from Rehm Thermal Systems has been added
Fast, network-based communication between the individual machines is enabled by the Hermes Standard: an option that was unavailable with the previous SMEMA standard. For this reason, an independent group of leading SMT equipment manufacturers, including Rehm Thermal Systems, has come together to develop a new interface: The Hermes Standard. With the previous SMEMA interface, communication from individual machines was reduced to digital signals: Machines did not communicate directly with each other; instead, the circuit board data was held in the MES systems at a higher level. A scanner was required in front of each machine to identify the assemblies.
By contrast, the Hermes Standard links the individual machines together via a direct form of horizontal communication. Data is exchanged throughout the entire SMT line, directly from machine to machine (M2M), and the data packets move through the machine together with the circuit boards. The Hermes data package is initially created at the start of the production line. There the barcode is printed, lasered or read in via a scanner. This data package is now communicated from machine to machine together with the circuit board. The new extension of the vertical interface introduced with Hermes 1.2 allows the circuit boards to be tracked in a production line or provides the option of synchronising the assembly’s data with an MES. This new form of interface communication is via TCP/IP and XML-based protocol, which uses standardised Ethernet hardware components and a flexible data format. This simplifies the integration process and reduces costs. In addition to the barcode of the assembly, other types of data (e.g. product, width, transport speed and similar) are communicated.
Customers of Rehm Thermal Systems seeking Hermes interface communication for the convection soldering system VisionXP+ can choose between two versions: one with a scanner on the outfeed conveyor and one without. Without the scanner on the outfeed conveyor it is not possible to manually reinsert a board. This reduces the risk of data being lost or being assigned to the wrong assemblies. If a scanner is present on the outfeed conveyor, boards can be removed after soldering and reinserted as the user requires. This is particularly important if a visual inspection is performed manually or if random samples are to be taken for quality assurance purposes. The correct assignment of data to the correct board is nevertheless preserved.
The convection soldering systems of the VisionX series from Rehm are also CFX-ready. With the CFX interface (IPC-CFX), communication is vertical and network-based. While the Hermes Standard is used primarily for M2M communication, the CFX is used for data uploading and downloading and for data analysis. The combination of horizontal Hermes communication and vertical CFX communication is absolutely necessary for a smart factory in the long run and represents a further step towards standardization.
About Rehm Thermal Systems
Rehm is a technology and innovation leader in the state-of-the-art, cost-effective manufacturing of electronic assembly groups and specialises in thermal system solutions for the electronics and photovoltaics industry. Rehm is a globally active manufacturer of reflow soldering systems using convection, condensation or vacuum, drying and coating systems, functional test systems, equipment for the metallisation of solar cells and numerous customised systems. We have a presence in all key growth markets and, as a partner with almost 30 years of industry experience, we are able to implement innovative production solutions that set new standards.
Testimonial
"Advertising in PCB007 Magazine has been a great way to showcase our bare board testers to the right audience. The I-Connect007 team makes the process smooth and professional. We’re proud to be featured in such a trusted publication."
Klaus Koziol - atgSuggested Items
Flexible Circuit Technologies to Host Free Flex Heater Webinar
08/18/2025 | Flexible Circuit TechnologiesGlobal Supplier of flexible circuits, flex design services, and assembly/box-build services, Flexible Circuit Technology will host their latest webinar, "Thermal Precision Meets Flexibility: The Technology Behind Heater Circuits" on Tuesday, August 26th, 2025 at 11 AM EDT.
A.R.T. Ltd. Nominated in Four Categories at 2025 Instrumentation and Electronics Industry Awards
08/11/2025 | A.R.T. Ltd.Advanced Rework Technology Ltd. (A.R.T. Ltd.), a leading provider of electronics training and consultancy, has been shortlisted in four categories at the 2025 Instrumentation and Electronics Industry Awards, including Industry Personality, Academic Support, Rising Star, and Best Customer Service.
EMC Taiwan Receives IPC-4101 Qualified Products Listing Certification
08/08/2025 | Global Electronics AssociationIPC’s Validation Services Program has awarded an IPC-4101 Qualified Products Listing (QPL) to Elite Materials Co. (EMC), an electronics base material manufacturing company headquartered in Taoyuan City, Taiwan.
Global Excellence in PCB Design: The Global Electronics Association Expands to Italy
08/07/2025 | Global Electronics AssociationIn today's rapidly evolving electronics industry, printed circuit boards (PCBs) serve as the critical backbone influencing the success, reliability, and time-to-market of countless products. Recognizing this essential role, the Global Electronics Association (formerly IPC), a worldwide leader in electronics standards, certification, and education, is now expanding its internationally acclaimed PCB design training to Italy.
Dana on Data: Best Practices in Interpreting Drawing Notes—‘Use Latest Revision’
08/07/2025 | Dana Korf -- Column: Dana on DataThe global nature of electronics manufacturing requires clear, consistent, and precise communication, particularly in technical documentation. An area where miscommunication often arises is in interpreting drawing notes—small lines of text with the potential to dramatically impact product quality, manufacturing efficiency, and customer satisfaction.