-
- News
- Books
Featured Books
- smt007 Magazine
Latest Issues
Current IssueWhat's Your Sweet Spot?
Are you in a niche that’s growing or shrinking? Is it time to reassess and refocus? We spotlight companies thriving by redefining or reinforcing their niche. What are their insights?
Moving Forward With Confidence
In this issue, we focus on sales and quoting, workforce training, new IPC leadership in the U.S. and Canada, the effects of tariffs, CFX standards, and much more—all designed to provide perspective as you move through the cloud bank of today's shifting economic market.
Intelligent Test and Inspection
Are you ready to explore the cutting-edge advancements shaping the electronics manufacturing industry? The May 2025 issue of SMT007 Magazine is packed with insights, innovations, and expert perspectives that you won’t want to miss.
- Articles
- Columns
- Links
- Media kit
||| MENU - smt007 Magazine
Synergy Between Smart Manufacturing and the Secure Supply Chain (Part 2)
June 5, 2019 | Michael Ford, Aegis Software Corp.Estimated reading time: 17 minutes
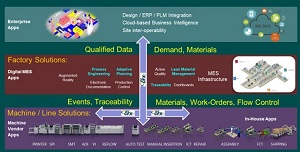
Editor’s Note: To read Part 1 of this article series, click here.
With the trend of shortening lead-times within the material ordering process, and the frequency with which urgent orders for materials from the grey market are made, there is increased opportunity for the ingress of counterfeit materials. The situation is made far worse when a genuine shortage of materials in the supply chain occurs. In many cases, the reaction to material supply issues in the market are addressed by the over-ordering of the affected materials in order to ensure supply for as long as possible, which only makes the problem worse, in general, across the industry, quickly escalating serious shortages to critical levels.
At these times, assembly manufacturers become desperate for material supply, which is also felt by material distributors where contracts are in place to assure supply. The search for eligible materials to satisfy the volatile demand goes far and wide, creating motivation and opportunity to fulfil materials orders with materials that are not of the standard or quality specified. Since most assembly manufacturers have trusted supplier agreements in place, incoming inspection of materials on receipt at the factory is no longer comprehensively performed.
Any counterfeit materials are likely not to be detected until the end of the assembly process as the product is tested; and often, not even then. Counterfeiters have been found to utilize techniques that specifically defeat incoming inspection procedures and create enough confusion to render the assembly company unable to find responsibility for the counterfeit material ingress. One example was found where the first 100 parts on a reel of materials were genuine, and then every seventh part was found to be counterfeit. Incoming inspection, were it to be in place for passive devices, would normally look at only the first materials in the reel. Having each seventh part counterfeit produces a random enough pattern to cause maximum confusion, should any defect be found during assembly and test. As these are cheap passive components in this example, little effort would be expected to manage them within the factory. The number of instances of counterfeit materials with passive components is, however, increasing rapidly. Even though the passive material itself may be insignificant as compared to, for example, high value ICs, the shortage of, or defect in, just one will prevent the product, and potentially the whole work order, from being shipped. With many counterfeit materials having an equivalent function, but to a lower specification than that of the genuine materials, it is very easy for counterfeit materials to go undetected through assembly and test processes—and become a part of safety critical products. Though it is possible to detect counterfeits through the use of inspection, test, and even X-ray processes, it is simply not practical to test all of the millions of material components that are placed by the average factory every day. Manufacturing could never bear the cost of that in today’s competitive world.
On the flip side, the use of electronics has become critical to virtually every aspect of human society, being a key part of every appliance and communication device, mode of transport, defense systems, etc. The consequences of not being able to eliminate the risk of defects getting through into the market will be disastrous for individuals as well as for the company brand image, not to mention the associated costs of recovery. It is only a matter of time, unless something very significant changes.
The Smart Factory
Discussion of traceability as part of the smart factory is not high on the agenda in most conversations. The focus of the smart factory is to deliver on the goals of providing flexible manufacturing, free of legacy constraints, which can deliver highly optimized use of assets, even with a high mix of products in small lots. A key aspect of the smart factory, however, is the ability to be in full control of production dependencies, which includes material flow. Industry 4.0 represents digitalization across all operational processes, sharing data seamlessly. An Industrial Internet of Things (IIoT) standard such as the Connected Factory Exchange (CFX) from IPC is the most effective way of achieving this.
Figure 1. The Smart Factory, Industry 4.0.
Within the smart factory, data is exchanged between automated machine processes, as well as manual assembly and test processes, so as to provide clear visibility of the operation of the factory. Data is exchanged at the execution level, allowing machine or line-based software to self-optimize their operations. Data is also exchanged between the execution layer and the factory layer, providing machines with specific material and work-order information, as well as providing exact material usage and spoilage information in the opposite direction. Many MES functions work together within the factory layer to provide an overall factory optimization, working in real-time, as customer demand changes. Data is then also exchanged with the high-level business systems, which potentially includes ERP and MRP, to ensure that they have the very latest information of what products have been made, are to be made in the near term, and what materials have been used and physically allocated at each operation.
For the scope of this article, the focus is on just four of the many areas that are the key elements belonging to the smart factory:
- Process engineering
- Adaptive planning
- Lean material logistics
- Traceability
The approach to process engineering in the smart factory is the complete opposite of what has been done traditionally. Instead of the assembly configuration being set in advance by process engineering, a common digital product model is created up-front, which can then be easily exported into data ready for any capable line configuration as required. The process starts with the elimination of all the disparate documents previously used to transfer the design and bill of materials (BOM) information into manufacturing.
Page 1 of 3
Suggested Items
Horizon Sales Celebrates 10 Years of Exceptional Service by Sales Leader David Smith
07/02/2025 | Horizon SalesHorizon Sales, a premier manufacturers’ representative and distributor for the electronics assembly industry, is proud to announce that David Smith is celebrating 10 years with the company this month.
EU Defence Electronics Ecosystem Highlighted in Brussels
07/01/2025 | I-Connect007 Editorial TeamIn this interview, Alison James, senior director of Global Electronics Association—Europe (formerly IPC), discusses the European Defence & Security Summit in Brussels, June 9–13, as well as the first IPC–ASD Europe Defense Electronics Summit, June 10th, which brought together 70 leaders from across the electronics manufacturing supply chain. ASD is the Aerospace, Security and Defence Industries Association of Europe, and co-hosted both the larger and smaller events.
Europlacer Expands U.S. Reach with New Eastern Region Representative
06/30/2025 | EuroplacerEuroplacer, a global leader in flexible SMT assembly solutions for High-Mix manufacturers, is pleased to announce the appointment of Photo Chemical Systems as its new representative for the Eastern United States.
PCBA Market to Reach $147.5 Billion by 2035, Growing at a CAGR of 4.7% from 2025
06/27/2025 | PRNewswireThe Printed Circuit Board Assembly market is projected to reach $147.5 billion by 2035, up from an estimated $90.91 billion in 2025, growing at a steady CAGR of 4.7% during the forecast period.
Indium Corporation Expert to Present on Automotive and Industrial Solder Bonding Solutions at Global Electronics Association Workshop
06/26/2025 | IndiumIndium Corporation Principal Engineer, Advanced Materials, Andy Mackie, Ph.D., MSc, will deliver a technical presentation on innovative solder bonding solutions for automotive and industrial applications at the Global Electronics A