DuPont on Materials Challenges and New Opportunities
June 11, 2019 | I-Connect007 Editorial TeamEstimated reading time: 5 minutes
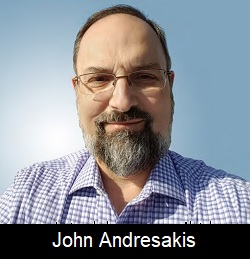
John Andresakis, senior marketing technologist in the Interconnect Solutions (ICS) Group of DuPont, and Jonathan Weldon, RF applications engineer also in ICS at DuPont, spoke with the I-Connect007 editorial team about trends the company is seeing, what challenges their customers are facing with materials today, and future opportunities with new technologies, including 5G, electric cars, IoT, etc.
Andy Shaughnessy: Starting with John Andresakis, could you talk about materials from a higher level, and then we’ll go to Jon to hear about some of your work with 5G in more detail?
Patty Goldman: Also, can you tell us a little bit about your division at DuPont? I’m interested in that and your perspective regarding flex circuits.
John Andresakis: Dow and DuPont merged August 31, 2017; now, we’re doing the spinoff into three different companies. In April, Dow split off and became their own company. In June, DuPont and Corteva—which is the agricultural business—will split off, which will complete the transition to three separate companies. We are going to be part of the new DuPont, which has several different divisions. Our division is Electronics and Imaging, and within that, we are part of Interconnect Solutions (ICS), which includes Pyralux laminates for flex materials and Kapton films. It also includes the Riston photoresist and the combined chemistry of Dow and DuPont for plating, final transitions, etc.—overall, the chemical processing for making PCBs.
Jonathan Weldon: In addition to the plating, we handle final finish, so for the most part, ICS contains everything for making a flex PCB from the ground up from Pyralux flexible copper-clad laminate through the final finish of the board.
Goldman: Okay, so what’s coming down the pike with new materials?
Andresakis: Everybody is looking for lower loss materials; that has been the major focus, especially in the rigid market. Customers are looking at what they can do to keep driving the losses lower to the point where they’re getting materials that are thermostats with properties getting close to Teflon-based (PTFE) materials. There has been a lot of work on resin chemistries. And when you get into this type of performance, the number of choices you have is somewhat limited. Now, it’s starting to get harder and harder to have an incremental improvement in the loss due to resins.
Weldon: We’re seeing an increase in the number of issues in high-speed digital. As they go to higher data rates, skew, signal levels, and SNR are becoming more of a problem, which goes back to what John was mentioning with low-loss materials. Glass-free materials have also started to become a hot topic as skew is no longer manageable by adjusting the glass weave or using traditional techniques. Even homogenous materials, such as polyimides, are becoming interesting to the high-speed digital community.
From the traditional RF, high-frequency side of things, we’re seeing an increase in the frequencies of interest. Traditional 4G LTE and consumer electronics applications were relatively low in frequency between 1–6 GHz. They’re still operating there today, but now we’re looking at the 28–39 GHz bands for 5G, which is changing the game.
It used to be that dielectric loss wasn’t the primary player while constant and conductor loss would have been fairly dominant, especially in thin constructions and flex. But with those higher frequencies now, dielectric loss itself starts to rear its ugly head, and traditional materials that might have been relatively lossy from a dissipation factor standpoint may not be sufficient for all applications. There is a definite need for improved materials.
Further, we’re seeing some interesting things in terms of design space where people are starting to increase package densities. There have been a lot of changes in substrate height requirements for certain designs that may have been very thick before but are trying to get thinner as well as things that have been thin that people are trying to make thicker to improve performance. Overall, we’re seeing changes in how people are approaching design challenges due to these higher frequencies.
Feinberg: What is the most used thickness of dry-film resist right now? Back in the day, it was 0.5 mil, 1 mil, or 1.3 mils.
Andresakis: Not much has changed as far as thickness; the range you mentioned is still very common. We still sell a lot of traditional Riston products because the lines and spaces for servers and routers haven’t changed appreciably either. I think it switches over when you go to the consumer world with modified semiadditive processes, etc. They’re using the thinner resists and switching from subtractive to additive processing. doing a plate up versus an etching. However, more people are using laser direct imaging for regular products because of the benefits you have removing the photo tool. Almost every board shop now has some degree of laser direct imaging, even if it is just for quick turns and prototypes.
Feinberg: We used to look at 10-mil lines and spaces being very, very fine line with 15–20-mil lines and spaces being more typical. Is that still the same for both the standard circuit boards as well as the ones where you’re trying to shrink all of the circuitry down? Because the average person wants more space in their phone for a battery than they do for a circuit board, but yet still want all of the functions. What kind of resolutions do you see now, and what are your customers asking for?
Andresakis: I haven’t checked in that space in a while. But when it comes to traditional high layer count, servers and routers, they’ve been doing 3-mil lines and spaces for a long time with traditional photoresist, so that’s not an issue. When it gets to the consumer, the big switch is that the resolutions have improved so you can do the subtractive process down to a finer point than before. But below a certain point (maybe 20–25 microns), the subtractive product starts to have issues. It has been reported that companies like Apple and their iPhones are using the modified semi-additive process. There’s more of a switch from a subtractive world to an additive or semi-additive world to get that next level of resolution. And the photoresists are capable of doing that; it’s just a matter of the overall process. As we start getting into those fine lines and spaces, everything becomes an issue. The materials, processes, environment, and pretty much everything must be under tight control. It has been reported that the initial yields have not been very good, but they are getting better.
To read the full article, which appeared in the May 2019 issue of PCB007 Magazine, click here.
Testimonial
"Advertising in PCB007 Magazine has been a great way to showcase our bare board testers to the right audience. The I-Connect007 team makes the process smooth and professional. We’re proud to be featured in such a trusted publication."
Klaus Koziol - atgSuggested Items
How Good Design Enables Sustainable PCBs
08/21/2025 | Gerry Partida, Summit InterconnectSustainability has become a key focus for PCB companies seeking to reduce waste, conserve energy, and optimize resources. While many discussions on sustainability center around materials or energy-efficient processes, PCB design is an often overlooked factor that lies at the heart of manufacturing. Good design practices, especially those based on established IPC standards, play a central role in enabling sustainable PCB production. By ensuring designs are manufacturable and reliable, engineers can significantly reduce the environmental impact of their products.
50% Copper Tariffs, 100% Chip Uncertainty, and a Truce
08/19/2025 | Andy Shaughnessy, I-Connect007If you’re like me, tariffs were not on your radar screen until a few months ago, but now political rhetoric has turned to presidential action. Tariffs are front-page news with major developments coming directly from the Oval Office. These are not typical times. President Donald Trump campaigned on tariff reform, and he’s now busy revamping America’s tariff policy.
Global PCB Connections: Understanding the General Fabrication Process—A Designer’s Hidden Advantage
08/14/2025 | Markus Voeltz -- Column: Global PCB ConnectionsDesigners don’t need to become fabricators, but understanding the basics of PCB fabrication can save you time, money, and frustration. The more you understand what’s happening on the shop floor, the better you’ll be able to prevent downstream issues. As you move into more advanced designs like HDI, flex circuits, stacked vias, and embedded components, this foundational knowledge becomes even more critical. Remember: the fabricator is your partner.
MKS’ Atotech to Participate in IPCA Electronics Expo 2025
08/11/2025 | AtotechMKS Inc., a global provider of enabling technologies that transform our world, announced that its strategic brands ESI® (laser systems) and Atotech® (process chemicals, equipment, software, and services) will showcase their latest range of leading manufacturing solutions for printed circuit board (PCB) and package substrate manufacturing at the upcoming 17th IPCA Show to be held at Pragati Maidan, New Delhi from August 21-23, 2025.
MKS Showcases Next-generation PCB Manufacturing Solutions at the Thailand Electronics Circuit Asia 2025
08/06/2025 | MKS Instruments, Inc.MKS Inc, a global provider of enabling technologies that transform our world, today announced its participation in Thailand Electronics Circuit Asia 2025 (THECA 2025), taking place August 20–22 at BITEC in Bangkok.