-
- News
- Books
Featured Books
- smt007 Magazine
Latest Issues
Current IssueWhat's Your Sweet Spot?
Are you in a niche that’s growing or shrinking? Is it time to reassess and refocus? We spotlight companies thriving by redefining or reinforcing their niche. What are their insights?
Moving Forward With Confidence
In this issue, we focus on sales and quoting, workforce training, new IPC leadership in the U.S. and Canada, the effects of tariffs, CFX standards, and much more—all designed to provide perspective as you move through the cloud bank of today's shifting economic market.
Intelligent Test and Inspection
Are you ready to explore the cutting-edge advancements shaping the electronics manufacturing industry? The May 2025 issue of SMT007 Magazine is packed with insights, innovations, and expert perspectives that you won’t want to miss.
- Articles
- Columns
- Links
- Media kit
||| MENU - smt007 Magazine
Data: Key to Automating Right the First Time
June 14, 2019 | Barry Matties, I-Connect007Estimated reading time: 6 minutes
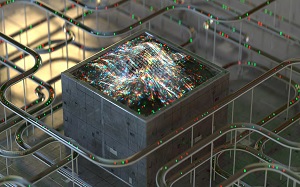
In this interview, Michael Ford, senior director of emerging industry strategy, reflects on his first two years with Aegis Software Corporation and looks to the future of the data-driven manufacturing environment. It is imperative that manufacturers streamline their manufacturing process to stay competitive. Michael shares how the CFX and data collection model can play an important role in the streamlining processes, including Industry 4.0 and the supply chain.
Barry Matties: You’ve been at Aegis for two years now. How have the first two years been?
Michael Ford: It has been a great experience because I love that my work is related to global industry standards, which has been very fulfilling. Only a couple of years ago, everybody was competing against each other, trying to work out their advantages with data when it was in its infancy. Since then, I’ve enjoyed the opportunity to be a friend of the industry as more companies are coming together.
In my role, I’ve worked with hundreds of companies across the world—especially in China—where the Connected Factory Exchange (CFX) is becoming extremely popular. Manufacturers have been approaching, saying, “For the last five years of Industry 4.0, only 5% of companies in the world have started to adopt it.” And this was not part of their five-year plan. They wanted it to go much faster, but it simply didn’t happen. Aegis has been providing the opportunity for the industry to understand what the standard means in terms of the defined data content, which is the first time this has ever been done.
And people thought it was impossible because nobody would agree. If you brought three machine vendors in competition with each other on a phone call, were they going to agree on what the data is going to be? Well, they have. They were guided a little bit because we need to see the big picture and keep the context, but we went through them one by one, hundreds of times over, and the standard is now published.
Matties: There’s a lot of fear that they were giving away proprietary information, but that was dispelled.
Ford: Right. It’s surprising that people would do that, considering the amount of antagonism that went on before because people differentiated themselves about what they could do. Now, we’re telling people, “You all need to provide the same data so that your customers will understand it all.” There are no hidden secrets anymore or proprietary pieces of data that can be used as we see in other formats; that doesn’t exist in CFX. This standard represents a genuine step forward. The next phase of the story is starting because hundreds of machine vendors have been developing CFX, and we need to bring the context to that data because machines only know what happens inside.
What’s in it for the machine vendors is the ability to see beyond the four walls of their machine or, in some machine vendors’ case, the four walls of their software controlling the line. But they also want to know about the materials coming in from the warehouse. At some point, every vendor wants to know what’s happening beyond—upstream or downstream on their line, what’s blocking them; what their quality results are; where their materials are coming from; and their plans, schedules, and customers’ needs. They want to optimize their machines automatically and meet that customer demand for automated manufacturing.
Now, they realize they can do this, but don’t know how because they are experts in machine software—not MES software. CFX becomes the bridge that connects the machines to the MES environment so that they don’t need to understand about MES and we don’t need to get involved with the machine side. We’re clearly aligned and collaborating together through CFX. The stage we’re at right now is hundreds of machine vendors are saying, “Let’s do something. What should we do? How are we going to do this?”
Matties: Putting the infrastructure in place is one thing, but implementation is another issue. There’s not necessarily a manual out there that says, “Here’s step one through to the final step.” The challenges include how do you choose, where do you start, what’s the right strategy?
Ford: Yes, because if you get it right the first time, you have very little cost or risk and a lot of gain.
Matties: And there’s a lot of fear because we know if we get it wrong the first time, the opposite of all that you just said happens.
Ford: We’re aiming to gather a few case studies from customers and machine vendors to show how achievable and easy it is to put something together. Signs are coming up already. There’s a lot of scope in the pipeline to see these things, and IPC is supporting the exchange of information. We’re setting up “A” teams to focus on different application areas, software development kits, and even a manual to help people get started. It’s all coming together through cooperation.
Matties: We’re looking at streamlining processes. Automation is a part of that, but what thought process should they follow?
Ford: I’ve always been suspicious about anybody who says, “Optimize your process,” because nobody defined the process. If you think about your process as a machine, it’s easy to do that. You bring in your Lean experts and start to analyze the waste and the value stream mapping, etc., but the process has dependencies. You have a machine before and after as well as materials coming in, so is that part of the process? I would say it is because, without those under control, you can’t do anything else. That has been the fundamental concept of manufacturing for quite a long time.
Your final assembly line does not stop no matter what, and to guarantee that process continues in the most efficient way, all of your dependencies have to be controlled to supply in time. I see all of this optimization as being a part of that. That’s where Aegis comes in because we have this unique, holistic program where we have one database over the entire manufacturing process—quality, materials, execution, everything. We can build the context of all of the different data points coming and provide that information as a tool for those who want to optimize their process, however they define it. They may want to do the machine, do a group of products on the line, or include all aspects of the factory, maintenance, and materials. The nice thing about it is you can do all of those with the data that we provide, and we’re not going to tell you how to do it.
CFX doesn’t say, “This is the way you do OEE and measure this.” We’re providing that contextual information from the machines. One thing that people don’t understand with the analysis of data is that in manufacturing, it’s not as simple as taking the data from the machine and analyzing it. That’s the wrong thing to do because the machines aren’t running most of the time.
The time that you’re optimizing is 20% of the day, in which the machine was running. You improved that by 5%, but it doesn’t make much difference. What you need to focus on is the 80% of the time that the machine wasn’t running, and that’s the time that you don’t get data from the machine, so how are you supposed to know? That’s the value of the MES cycle because maybe the problem was the materials, a changeover, the schedule, or that the customer doesn’t want anything or there’s maintenance going on. How can we optimize that to reduce 10% of the 80%, which is so much more value than 10% of the 20%?
To read the full article, which appeared in the June 2019 issue of SMT007 Magazine, click here.
Suggested Items
The Global Electronics Association Releases IPC-8911: First-Ever Conductive Yarn Standard for E-Textile Application
07/02/2025 | Global Electronics AssociationThe Global Electronics Association announces the release of IPC-8911, Requirements for Conductive Yarns for E-Textiles Applications. This first-of-its-kind global standard establishes a clear framework for classifying, designating, and qualifying conductive yarns—helping to address longstanding challenges in supply chain communication, product testing, and material selection within the growing e-textiles industry.
IPC-CFX, 2.0: How to Use the QPL Effectively
07/02/2025 | Chris Jorgensen, Global Electronics AssociationIn part one of this series, we discussed the new features in CFX Version 2.0 and their implications for improved inter-machine communication. But what about bringing this new functionality to the shop floor? The IPC-CFX-2591 QPL is a powerful technical resource for manufacturers seeking CFX-enabled equipment. The Qualified Product List (QPL) helps streamline equipment selection by listing models verified for CFX compliance through a robust third-party virtual qualification process.
Advancing Aerospace Excellence: Emerald’s Medford Team Earns Space Addendum Certification
06/30/2025 | Emerald TechnologiesWe’re thrilled to announce a major achievement from our Medford, Oregon facility. Andy Abrigo has officially earned her credentials as a Certified IPC Trainer (CIT) under the IPC J-STD-001 Space Addendum, the leading industry standard for space and military-grade electronics manufacturing.
Magnalytix and Foresite to Host Technical Webinar on SIR Testing and Functional Reliability
06/26/2025 | MAGNALYTIXMagnalytix, in collaboration with Foresite Inc., is pleased to announce an upcoming one-hour Webinar Workshop titled “Comparing SIR IPC B-52 to Umpire 41 Functional & SIR Test Method.” This session will be held on July 24, 2025, and is open to professionals in electronics manufacturing, reliability engineering, and process development seeking insights into new testing standards for climatic reliability.
IPC Rebrands as Global Electronics Association: Interview With Dr. John W. Mitchell
06/22/2025 | Marcy LaRont, I-Connect007Today, following a major announcement, IPC is embracing the rapid advancement of technology with a bold decision to change its name to the Global Electronics Association. This name more accurately reflects the full breadth of its work and the modern realities of electronics manufacturing. In this exclusive interview, Global Electronics Association President and CEO Dr. John W. Mitchell shares the story behind the rebrand: Why now, what it means for the industry, and how it aligns with the organization’s mission.