-
- News
- Books
Featured Books
- pcb007 Magazine
Latest Issues
Current IssueInventing the Future with SEL
Two years after launching its state-of-the-art PCB facility, SEL shares lessons in vision, execution, and innovation, plus insights from industry icons and technology leaders shaping the future of PCB fabrication.
Sales: From Pitch to PO
From the first cold call to finally receiving that first purchase order, the July PCB007 Magazine breaks down some critical parts of the sales stack. To up your sales game, read on!
The Hole Truth: Via Integrity in an HDI World
From the drilled hole to registration across multiple sequential lamination cycles, to the quality of your copper plating, via reliability in an HDI world is becoming an ever-greater challenge. This month we look at “The Hole Truth,” from creating the “perfect” via to how you can assure via quality and reliability, the first time, every time.
- Articles
- Columns
- Links
- Media kit
||| MENU - pcb007 Magazine
Estimated reading time: 5 minutes
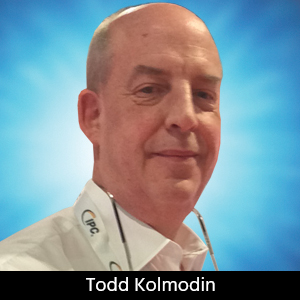
Testing Todd: The Evolution of Probers and Fixture Testers: Blinded by Science
Electrical test today has changed dramatically since the "pin-in-hole" technology of yesteryear. Although you may still find these designs today, predominantly you will run across the mind-altering designs of our current generation. It boggles the brain to think that computers once inhabited entire rooms to process just "bits" and "bytes" of data. Now, your smartwatch processes more data than many of those computers combined! The smartphone that you use every day has more computing power than the computers used in the Apollo 13 spacecraft!
It's no wonder that today's requirements have become immensely important in guaranteeing success in the products produced. Shorts, opens, impedance, capacitance, dielectric breakdown, and resistance are all major factors in the success or failure of today's PCBs.
With that said, the evolution of the PCB has come a long way in the last 30 years. The science of electrical test has had to travel that road as well. It's not just a question of screening for opens and shorts. Today, the library extends to interrogating passive components, efficiently and cost-effectively evaluating dielectrics with multiple planes and pairs involved, and adhering to strict requirements from the military, export regulations, and OEMs alike. So, it is easy to understand that ET has become much more of a science than history remembers.
Probers Versus Fixture Testers Probers
Today's probers (flying probes) are much more advanced than their distant relatives of days gone by. Probers not only provide the standard opens and shorts test but also buried passive, four-wire Kelvin, and HiPot testing. They can still provide the strict, resistive-only test still required by some OEMs and high-reliability applications, but probers can also provide indirect testing by signature comparison. This is accomplished by developing a capacitive master from a test specimen that has gone through and passed the strict resistive test. The subsequent boards have their capacitive signature compared to the master, and any nets that are atypical compared to the master are retested in resistive mode to guarantee they are acceptable.
Historic requirements of PCBs did not allow probers in some military requirements or performance classes. This was due, in part, to the lack of ability to detect defects in the 3D environment. Probers of today have the ability to scan the horizon as well as the third dimension or the Z axis. This is known as “line of sight” horizontal or “Z-axis” vertical adjacency. Statistical probabilities have been accepted that if a defect is going to occur, it will occur in a given window between two adjacent nets. This is referred to as the “adjacency window.” Historically, this was limited to the horizontal axis or the same layer. This window can now be expanded to layers adjacent in the vertical axis. This enhancement in prober technology is one of the main reasons that some military and higher-performance class products can now be tested utilizing flying probes. This has allowed quicker turn time and reduced cost for electrical test.
However, you will not find this technology available in older probers. Software and metering systems in older equipment just didn’t have the capacity to perform some of the required tests of today. One needs to inquire about the capabilities of the given prober versus the requirements you may have. Remember your deliverables. Some equipment may provide only some of your solutions while others may deliver the full package and more!
Fixture Testers
There is still no question that fixture testers provide the ultimate opens and shorts test. The fixture tester still provides the full parametric test. The simultaneous compression and test of all nets will still detect possible defects that no flying probe will ever find. This is because the fixture tester applies stress to the PCB. The simultaneous compression may detect microfractures to traces and/or barrels during the test that a flying probe may not. They also do not have the limitation of the adjacency windows as the flying probes have. The isolation test covers all nets to all nets regardless of proximity. A gross short defect covering a long distance will be detected where on a flying probe, it may be out of the adjacency window and not tested. Although rare and statistically low in occurrence, this type of defect would always be detected on a fixture tester.
Fixture testers are still the answer to high-volume production. Automation and dedicated fixtures process thousands of boards per time segment compared to a much smaller amount with flying probes. Although automation does exist for flying probes, they will never be able to handle the volume per capita compared to the fixture tester.
Conclusion
As you can see, the evolution of the PCB and electrical test have come a long way in the last few decades. The advances in PCB manufacturing and design have forced the evolution of ET and the methods used. ET has become as much of a new science as the new manufacturing designs coming from the OEMs. Just checking for opens and shorts is no longer enough. Requirements now not only include the opens and shorts test but also the guard zones of buried passives that are independent of the IPC performance class continuity requirement. Along comes multiple voltage requirements within the same board, HiPot requirements, and in many cases, time domain reflectometry (TDR.) Again, ET needs to supply all these services as efficiently and cost-effectively as possible, which is why finding the right equipment solution is imperative.
Test requirements continue to change as the designs advance. When searching for the right solution, gauge your requirements against the deliverables of the equipment. The advancements in prober technology will now provide multiple solutions within the same package. Do your homework, and you may find that the science of electrical test is not as ominous as you thought. As a colleague of mine once said, “I can’t even spell ET.” We can find answers to black holes. Whether you are doing electrical test yourself or have a partner to turn-key it for you, I hope this bit of knowledge I’ve passed along helps in decision making and understanding some of the science behind ET. ET is a much bigger process than what it used to be, so give those folks a chance when the delivery heat is on. It takes a little more time nowadays to "git 'er done!"
Todd Kolmodin is VP of quality for Gardien Services USA and an expert in electrical test and reliability issues.
This column was originally published in the May 2019 issue of PCB007 Magazine.
More Columns from Testing Todd
Testing Todd: Why 4-wire Kelvin?Testing Todd: Why TDR?
Testing Todd: Positivity Boosts Employee Morale
Testing Todd: Preparing Employees for the Long Haul
Testing Todd: Where Can We Improve?
Testing Todd: Turning Into the Wind
Testing Todd: Coming Back to Life—Design Recovery
Testing Todd: Decision Time—Invest or Delegate?