-
- News
- Books
Featured Books
- smt007 Magazine
Latest Issues
Current IssueSupply Chain Strategies
A successful brand is built on strong customer relationships—anchored by a well-orchestrated supply chain at its core. This month, we look at how managing your supply chain directly influences customer perception.
What's Your Sweet Spot?
Are you in a niche that’s growing or shrinking? Is it time to reassess and refocus? We spotlight companies thriving by redefining or reinforcing their niche. What are their insights?
Moving Forward With Confidence
In this issue, we focus on sales and quoting, workforce training, new IPC leadership in the U.S. and Canada, the effects of tariffs, CFX standards, and much more—all designed to provide perspective as you move through the cloud bank of today's shifting economic market.
- Articles
- Columns
- Links
- Media kit
||| MENU - smt007 Magazine
The Jefferson Institute of Technology: Facts and Updates
July 5, 2019 | The Jefferson ProjectEstimated reading time: 2 minutes
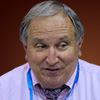
Founded by Tom Borkes, the Jefferson Project—through the Jefferson Institute of Technology (JIT)—aims to build and maintain a world class workforce for the domestic electronics manufacturing industry, while showcasing state-of-the-art equipment and developing emerging assembly technologies.
Based on the principles of Concurrent Education, JIT will use a state-of-the-art not-for-profit business—the Jefferson Electronic Manufacturing Center (JEM Center)—as the environment for learning during the entire tenure of a student's education. Students will receive an intensive, continually updated academic program, using the manufacturing business as their classroom. Hands-on experience in every facet of the manufacturing operation will teach real-world skills and problem solving. In addition, product developers and equipment manufacturers can observe the latest electronic packaging technologies in a real-world application.
Here are some JIT facts:
1. JIT will be co-located with the JEM Center, a contract manufacturing (EMS) business.
2. The JEM Center will provide the student with a real-world classroom to supplement the traditional undergraduate engineering education.
3. Over four years, JIT students will participate in every aspect of the JEM Center operation—and, be paid for their contributions.
4. Successful completion of the four-year JIT program will result in a B.S. in Applied Product Design and Production Sciences.
5. Each product assembly process step continues to be scrutinized and assigned to a traditional applicable engineering class, e.g., printing solder paste to chemistry, fluid dynamics, etc. The JIT class is then supplemented with process-related content.
6. The JIT academic year will consist of three, 16-week trimesters.
7. Students will graduate with APICS (Material & Supply Chain Management) and ASQ (Including 6-Sigma Black Belt) certifications. They also will have taken the Fundamentals in Engineering (FE) Exam that can lead to a P.E license.
8. Real world issues encountered by the student in the JEM Center operation will be addressed in real time. These issues, many without closed-form solutions, will permit the student to develop a crucial skill: good judgment—invaluable to their future employers.
9. Corporate sponsors will provide leading edge automation equipment and supplies. Students will always be learning in a state-of-the art environment.
10. Basic student tuition is $5,000/trimester. Corporate student sponsorships, scholarships and the paid work in the JEM Center can reduce this cost.
11. Curriculum development is partially based on Mortimer Adler’s Paideia Proposal and The Great Books, but with a blending of Learning for Learning, AND Learning for Earning.
12. The School’s development borrows from the Jeffersonian strategy he used for The University of Virginia.
13. Formal contracts between students and JEM’s clients will guarantee students a job upon graduation, and guarantee the client companies employees with a world class education—those educated by building the company’s products.
A freshman, Trimester 1 class listing has already been released, where “Civics” and “Organizational & Personal Ethics in an Engineering Environment” classes have been added. For more information, contact Tom Borkes at jeffer2@earthlink.net.
Testimonial
"The I-Connect007 team is outstanding—kind, responsive, and a true marketing partner. Their design team created fresh, eye-catching ads, and their editorial support polished our content to let our brand shine. Thank you all! "
Sweeney Ng - CEE PCBSuggested Items
Indium Promotes Huang to Senior Manager, Marketing Communications
08/28/2025 | Indium CorporationWith its commitment to innovation and growth through employee development, Indium Corporation announces the promotion of Jingya Huang to Senior Manager, Marketing Communications, to continue to lead the company’s branding and promotional efforts.
Rehm Academy Expands Its Training Program
08/28/2025 | Rehm Thermal SystemsThe demands on modern industrial companies and employees continue to rise, and therefore, the topic of further education is becoming increasingly important today.
MacDermid Alpha Awarded for Innovation: Driving Process Optimization and Efficiency with Major Indian EMS Provider
08/28/2025 | MacDermid Alpha Electronics SolutionsMacDermid Alpha Electronics Solutions, a leading global supplier of integrated materials for the electronics industry, is recognized by one of India’s top EMS providers, Syrma SGS, with an award for innovation that advanced process optimization, enhanced operational efficiency, and yield gains.
Integrated Solutions for Board-level Reliability: A Smarter Path Forward
08/27/2025 | Alan Gardner, MacDermid Alpha Electronics SolutionsIn today’s electronics manufacturing landscape, reliability is no longer just a benchmark but a business imperative. As industries such as automotive, aerospace, and high-performance computing (HPC) push the boundaries of innovation, the demand for dependable board-level performance under extreme conditions has never been greater.
ZESTRON Expands Capabilities with Addition of the EPS by i-Tech AG 75 Pallet Cleaning System
08/26/2025 | ZESTRONZESTRON, the global leader in high-precision cleaning solutions and services, is excited to announce the addition of a new capability in its Technical Center in Manassas, VA: