-
- News
- Books
Featured Books
- smt007 Magazine
Latest Issues
Current IssueWhat's Your Sweet Spot?
Are you in a niche that’s growing or shrinking? Is it time to reassess and refocus? We spotlight companies thriving by redefining or reinforcing their niche. What are their insights?
Moving Forward With Confidence
In this issue, we focus on sales and quoting, workforce training, new IPC leadership in the U.S. and Canada, the effects of tariffs, CFX standards, and much more—all designed to provide perspective as you move through the cloud bank of today's shifting economic market.
Intelligent Test and Inspection
Are you ready to explore the cutting-edge advancements shaping the electronics manufacturing industry? The May 2025 issue of SMT007 Magazine is packed with insights, innovations, and expert perspectives that you won’t want to miss.
- Articles
- Columns
- Links
- Media kit
||| MENU - smt007 Magazine
ICT or Flying Probe: Which Test Is Best for Your Assembly?
July 10, 2019 | Russell Poppe, JJS ManufacturingEstimated reading time: 3 minutes
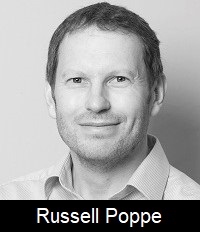
In-circuit test (ICT) and flying probe are two of the most popular types of automated test equipment (ATE) used in electronic printed circuit board assembly (PCBA). But what sets them apart? And how can you decide on the test strategy that is going to work best for your assemblies? In this article, I highlight the benefits (and the shortcomings) of both ICT and flying probe with a specific focus on three areas: product design, coverage, and cost.
1. Product Design
A good quality test program (also known as good coverage) will rely on the quality of your computer-aided design (CAD) data and schematics. The CAD data is used to generate the basic test programme, which ensures that information is sourced from the original design rather than any manual interpretation of other data. Good quality populated, and unpopulated, sample PCBAs are also vital for fine-tuning the test programmes, debugging, and making any fixtures so that the assemblies physically fit as they were intended.
Thinking about product design for a moment, what are the differences between each test solution which you may want to keep in mind? Flying probe machines, like those offered by Takaya, can probe the ends of component pads and uncovered vias to get access to the electrical networks. ICT will require at least a 50thou wide test pad per net, which has been designed into the PCB upfront and is used as a target for the fixed test probe. Double-sided fixtures can be costly, so these should, ideally, be on one side only of the PCB.
2. Coverage
When I talk about coverage, I’m referring to how much of the circuit you are actually able to test. Both ICT and flying probe carry out what is called a manufacturing defects analysis (MDA), which allows for the majority of the most common process faults that are likely to occur. These can include open circuits (due to insufficient or faulty soldering), short circuits, passive component measurements (resistors and capacitors), diode and transistor orientation, and basic supply voltage measurements.
However, given that these elements are common to both types of the testing platform, what sets them apart?
- Most flying probe systems will offer some form of limited optical inspection, which adds coverage for those components that can’t be accessed electrically; ICT fixtures usually won’t offer the option of optical inspection
- In addition to vectorless test, integrated circuits (ICs) can also include some powered (albeit basic) functional testing to check the soldering of pins to the PCB through a non-contact capacitive probe or plate; in most cases, flying probe is limited to only vectorless test
- ICT can also provide limited analogue and digital measurements, which flying probe isn't capable of due to the limited number of probes
3. Cost
The programming cost will depend on the complexity of the assembly but is broadly the same for either test solution (potentially around $2,500 or so). When it comes to other charges associated with test, however, there are some key differences to bear in mind:
- The fixture costs of flying probe are usually zero; in contrast, an ICT fixture can run to nearly $5,000
- The development lead time for flying probe is typically less than a week; ICT can take up to six weeks for fixture manufacture and programming
- In the event that your product design changes in any way, it will only require a programme change; in the case of ICT, it could well require a new fixture as well if any components or test pads have moved
- The actual machine test time of ICT is usually less than a minute, which means it is ideal for working quickly through larger batches; flying probe, on the other hand, can take several minutes, which means it's often more suited to smaller batches
- The speed of ICT also means that it is relatively inexpensive, often coming in at less than $1.24 per unit; flying probe is a much slower process and can cost $62 or more per assembly)
If you're still unsure about which test option is best for your product, you may find this simple visual checklist useful in comparing the pros and cons:
When it comes to test, each product will have its own unique requirements. But by keeping in mind the primary benefits (and points of difference) of the two platforms, you should feel much better placed to select the best test strategy for your PCBA assembly.
Russell Poppe is the director of technology at JJS Manufacturing.
Suggested Items
DownStream Acquisition Fits Siemens’ ‘Left-Shift’ Model
06/26/2025 | Andy Shaughnessy, I-Connect007I recently spoke to DownStream Technologies founder Joe Clark about the company’s acquisition by Siemens. We were later joined by A.J. Incorvaia, Siemens’ senior VP of electronic board systems. Joe discussed how he, Rick Almeida, and Ken Tepper launched the company in the months after 9/11 and how the acquisition came about. A.J. provides some background on the acquisition and explains why the companies’ tools are complementary.
Elementary Mr. Watson: Retro Routers vs. Modern Boards—The Silent Struggle on Your Screen
06/26/2025 | John Watson -- Column: Elementary, Mr. WatsonThere's a story about a young woman preparing a holiday ham. Before putting it in the pan, she cuts off the ends. When asked why, she shrugs and says, "That's how my mom always did it." She asks her mother, who gives the same answer. Eventually, the question reaches Grandma, who laughs and says, "Oh, I only cut the ends off because my pan was too small." This story is a powerful analogy for how many PCB designers approach routing today.
Connect the Dots: The Future of PCB Design and Manufacturing
07/02/2025 | Matt Stevenson -- Column: Connect the DotsFor some time, I have been discussing the increasing complexity of PCBs and how designers can address the constantly evolving design requirements associated with them. My book, "The Printed Circuit Designer’s Guide to… Designing for Reality," details best practices for creating manufacturable boards in a modern production environment.
Siemens Turbocharges Semiconductor and PCB Design Portfolio with Generative and Agentic AI
06/24/2025 | SiemensAt the 2025 Design Automation Conference, Siemens Digital Industries Software today unveiled its AI-enhanced toolset for the EDA design flow.
Cadence AI Autorouter May Transform the Landscape
06/19/2025 | Andy Shaughnessy, Design007 MagazinePatrick Davis, product management director with Cadence Design Systems, discusses advancements in autorouting technology, including AI. He emphasizes a holistic approach that enhances placement and power distribution before routing. He points out that younger engineers seem more likely to embrace autorouting, while the veteran designers are still wary of giving up too much control. Will AI help autorouters finally gain industry-wide acceptance?