First Programmable Memristor Computer Aims to Bring AI Processing Down from the Cloud
July 18, 2019 | Michigan State UniversityEstimated reading time: 4 minutes
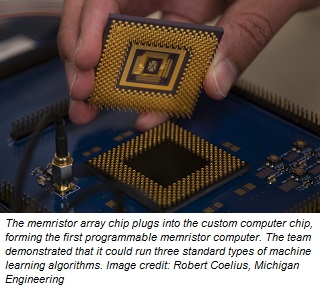
The memristor array chip plugs into the custom computer chip, forming the first programmable memristor computer. The team demonstrated that it could run three standard types of machine learning algorithms. Image credit: Robert Coelius, Michigan Engineering.
ANN ARBOR—The first programmable memristor computer—not just a memristor array operated through an external computer—has been developed at the University of Michigan.
It could lead to the processing of artificial intelligence directly on small, energy-constrained devices such as smartphones and sensors. A smartphone AI processor would mean that voice commands would no longer have to be sent to the cloud for interpretation, speeding up response time.
“Everyone wants to put an AI processor on smartphones, but you don’t want your cell phone battery to drain very quickly,” said Wei Lu, U-M professor of electrical and computer engineering and senior author of the study in Nature Electronics.
In medical devices, the ability to run AI algorithms without the cloud would enable better security and privacy.
Why Memristors are Good for Machine Learning
The key to making this possible could be an advanced computer component called the memristor. This circuit element, an electrical resistor with a memory, has a variable resistance that can serve as a form of information storage. Because memristors store and process information in the same location, they can get around the biggest bottleneck for computing speed and power: the connection between memory and processor.
This is especially important for machine-learning algorithms that deal with lots of data to do things like identify objects in photos and videos—or predict which hospital patients are at higher risk of infection. Already, programmers prefer to run these algorithms on graphical processing units rather than a computer’s main processor, the central processing unit.
“GPUs and very customized and optimized digital circuits are considered to be about 10-100 times better than CPUs in terms of power and throughput.” Lu said. “Memristor AI processors could be another 10-100 times better.”
GPUs perform better at machine learning tasks because they have thousands of small cores for running calculations all at once, as opposed to the string of calculations waiting their turn on one of the few powerful cores in a CPU.
A memristor array takes this even further. Each memristor is able to do its own calculation, allowing thousands of operations within a core to be performed at once. In this experimental-scale computer, there were more than 5,800 memristors. A commercial design could include millions of them.
Memristor arrays are especially suited to machine learning problems. The reason for this is the way that machine learning algorithms turn data into vectors—essentially, lists of data points. In predicting a patient’s risk of infection in a hospital, for instance, this vector might list numerical representations of a patient’s risk factors.
Then, machine learning algorithms compare these “input” vectors with “feature” vectors stored in memory. These feature vectors represent certain traits of the data (such as the presence of an underlying disease). If matched, the system knows that the input data has that trait. The vectors are stored in matrices, which are like the spreadsheets of mathematics, and these matrices can be mapped directly onto the memristor arrays.
What’s more, as data is fed through the array, the bulk of the mathematical processing occurs through the natural resistances in the memristors, eliminating the need to move feature vectors in and out of the memory to perform the computations. This makes the arrays highly efficient at complicated matrix calculations. Earlier studies demonstrated the potential of memristor arrays for speeding up machine learning, but they needed external computing elements to function.
Wei Lu stands with first author Seung Hwan Lee, an electrical engineering PhD student, who holds the memristor array. Image credit: Robert Coelius, Michigan Engineering
Page 1 of 2
Testimonial
"Advertising in PCB007 Magazine has been a great way to showcase our bare board testers to the right audience. The I-Connect007 team makes the process smooth and professional. We’re proud to be featured in such a trusted publication."
Klaus Koziol - atgSuggested Items
Macronix Introduces Cutting-Edge Secure-Boot NOR Flash Memory
08/08/2025 | PRNewswireMacronix International Co., Ltd., a leading integrated device manufacturer in the non-volatile memory (NVM) market, announced ArmorBoot MX76, a robust NOR flash memory combining in a single device, the essential performance and an array of security features that deliver rapid boot times and iron-clad data protection.
Inside the AI Hardware Boom: Servers, Substrates and Advanced Packaging
08/07/2025 | Edy Yu, Printed Circuit Information, China, and Marcy LaRont, I-Connect007AI is rewriting the hardware playbook, marrying complex software and algorithms to run and improve machine and equipment operations. Sorting through, managing, and utilizing massive amounts of data takes tremendous data storage and processing power. Enter the new generation of supercomputers and data servers. The data servers being built today are not your momma’s server, as they say.
AI Is the Golden Track Reviving Electronics and PCBs
08/06/2025 | Edy Yu, Chief Editor, ECIO, and the I-Connect007 Editorial TeamRemember 2021? Despite COVID, the electronics industry hit a high. Then came the slide. By 2023, the industry was deep in the red. With inflation, policy shifts, and exchange rate shocks, the problems were long, and the outlook was bleak. Recovery finally appeared in 2024, but it was fragile. Automotive electronics slumped, wireless demand stayed soft, and the ride up was anything but smooth. Yet, amid the uncertainty, one bright track emerged: artificial intelligence (AI).
Brent Laufenberg Appointed CIO of the Global Electronics Association, Advancing Technology and Member Services
07/31/2025 | Global Electronics AssociationThe Global Electronics Association (formerly IPC International Inc.) announces the appointment of Brent Laufenberg as its new Chief Information Officer (CIO).
SES AI Accelerates Timeline for Revenue Growth and Profitability with Acquisition of UZ Energy
07/31/2025 | BUSINESS WIRESES AI Corporation, a global leader in the development and manufacturing of AI-enhanced high-performance Li-Metal and Li-ion batteries, today announced it has executed a definitive agreement to acquire 100% of UZ Energy, an energy storage systems (“ESS”) provider, for a purchase price of approximately $25.5 million, subject to earnout adjustment based on the achievement of specified financial targets.