-
- News
- Books
Featured Books
- pcb007 Magazine
Latest Issues
Current IssueThe Hole Truth: Via Integrity in an HDI World
From the drilled hole to registration across multiple sequential lamination cycles, to the quality of your copper plating, via reliability in an HDI world is becoming an ever-greater challenge. This month we look at “The Hole Truth,” from creating the “perfect” via to how you can assure via quality and reliability, the first time, every time.
In Pursuit of Perfection: Defect Reduction
For bare PCB board fabrication, defect reduction is a critical aspect of a company's bottom line profitability. In this issue, we examine how imaging, etching, and plating processes can provide information and insight into reducing defects and increasing yields.
Voices of the Industry
We take the pulse of the PCB industry by sharing insights from leading fabricators and suppliers in this month's issue. We've gathered their thoughts on the new U.S. administration, spending, the war in Ukraine, and their most pressing needs. It’s an eye-opening and enlightening look behind the curtain.
- Articles
- Columns
- Links
- Media kit
||| MENU - pcb007 Magazine
Focusing on Surface Sensitivity for Reliability
August 20, 2019 | Andy Shaughnessy, I-Connect007Estimated reading time: 3 minutes
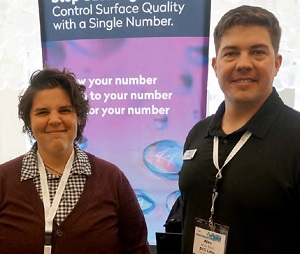
During the IPC High-Reliability Forum and Microvia Summit, I spoke with Customer Applications Scientist Elizabeth Kidd and Sales Engineer Alex Bien, both of BTG Labs, about their presentation on the challenges of working with highly sensitive surfaces, such as the risk of contamination. We also discussed the various surface characterization techniques that BTG Labs uses to identify such contaminants, and some PCB design strategies for creating a better surface—and a more reliable board.
Andy Shaughnessy: Elizabeth, it’s nice to meet you. I know you’re giving a presentation in a few days, but tell us about the company, and then we’ll talk about your presentation.
Elizabeth Kidd: Sure. BTG labs is a materials science company specializing in surface science and adhesion technologies. We have our roots in being a research and development lab and scoping root cause analyses for people who are scratching their heads at these industrial adhesion problems. From there, we develop the technology to make manufacturing floor inspections of materials as they go through their critical surface process points.
Alex Bien: We help folks to hone in on one area—the surface—that they’ve never had eyes on nor had a way to quickly evaluate surface chemistry in a fast, point-and-shoot manner. Our opening speaker today is addressing this lack of insight into the three nanometers that we need to control to create reliable adhesion. Thus, our focus is putting that technology to the floor in the hands of people who are making dollars-and-cents decisions every day.
Kidd: And taking the high sensitivity of R&D techniques—such as XPS, X-ray photoelectron spectroscopy, and FTIR, which is Fourier transform infrared spectroscopy—that have their eyes on the top molecular layer of a surface, and being able to scale that to a method or technique that can be taken onto the manufacturing floor.
Shaughnessy: Can you also tell us about your presentation?
Kidd: The presentation addressed what we just mentioned—controlling your surface process to better your wire bonding, die pad bonding, laminate coating adhesion, and all of those things. We even have some applications for the coupling agents that we were speaking of known as a conversion coating, and other industries use those organosilanes to increase adhesion between organic material and inorganic material.
Shaughnessy: Are you talking about copper, FR-4, and any sort of surface?
Kidd: Yes. We’ll have some applications in metallics, polymers, and in composites as well.
Bien: That’s a good point, though. It’s particularly difficult to control surface chemistry and match surface chemistry between dissimilar materials. It’s very easy to bond metal to metal, and it’s pretty easy to bond composite to composite, but metal to polymer, glass to polymer, and those material interfaces are more challenging to create to promote adhesion.
Shaughnessy: What are the biggest takeaways from your talk?
Kidd: Namely, the sensitivity of this surface. As Alex mentioned, we have a monomolecular layer that we’re trying to control, and that layer is highly sensitive to contamination events. Contact contaminants from the manufacturing process—things like upstream process aids from stamping or anything left over from any wash process from a chemical etch bath—have a huge impact. Or perhaps you’ve had a change in your supply chain where supplier X used chemical X, and now supplier Y is using chemical Y, and all of a sudden, you have more random failures or successes, and you don’t know why.
It’s drawing attention to those small changes in a process that can affect that monolayer that we’re trying to adhere to. We’ll mainly be talking about contamination, how to look for it, how to characterize that, using various surface characterization techniques—such as FTIR, XPS, and contact angle measurements—and surface activation and detection of coatings. The main takeaway is to increase the awareness of the sensitivity and how you can change—negatively or positively—that surface, even unknowingly.
Shaughnessy: With one small thing having a large influence on the process.
Bien: A small change in the process creates a snowball effect downstream.
Kidd: Exactly. Think about a fingerprint. If you put a fingerprint on the surface, that’s 1,000–10,000 molecules thick. If you try to stick something to it now, you’re not sticking to the surface; you’re sticking to the chemicals and the oil from that person’s fingers. That kind of sensitivity is important.
To read the full article, which appeared in the July 2019 issue of PCB007 Magazine, click here.
Suggested Items
Trump Copper Tariffs Spark Concern
07/10/2025 | I-Connect007 Editorial TeamPresident Donald Trump stated on July 8 that he plans to impose a 50% tariff on copper imports, sparking concern in a global industry whose output is critical to electric vehicles, military hardware, semiconductors, and a wide range of consumer goods. According to Yahoo Finance, copper futures climbed over 2% following tariff confirmation.
Happy’s Tech Talk #40: Factors in PTH Reliability—Hole Voids
07/09/2025 | Happy Holden -- Column: Happy’s Tech TalkWhen we consider via reliability, the major contributing factors are typically processing deviations. These can be subtle and not always visible. One particularly insightful column was by Mike Carano, “Causes of Plating Voids, Pre-electroless Copper,” where he outlined some of the possible causes of hole defects for both plated through-hole (PTH) and blind vias.
Trouble in Your Tank: Can You Drill the Perfect Hole?
07/07/2025 | Michael Carano -- Column: Trouble in Your TankIn the movie “Friday Night Lights,” the head football coach (played by Billy Bob Thornton) addresses his high school football team on a hot day in August in West Texas. He asks his players one question: “Can you be perfect?” That is an interesting question, in football and the printed circuit board fabrication world, where being perfect is somewhat elusive. When it comes to mechanical drilling and via formation, can you drill the perfect hole time after time?
The Evolution of Picosecond Laser Drilling
06/19/2025 | Marcy LaRont, PCB007 MagazineIs it hard to imagine a single laser pulse reduced not only from nanoseconds to picoseconds in its pulse duration, but even to femtoseconds? Well, buckle up because it seems we are there. In this interview, Dr. Stefan Rung, technical director of laser machines at Schmoll Maschinen GmbH, traces the technology trajectory of the laser drill from the CO2 laser to cutting-edge picosecond and hybrid laser drilling systems, highlighting the benefits and limitations of each method, and demonstrating how laser innovations are shaping the future of PCB fabrication.
Day 2: More Cutting-edge Insights at the EIPC Summer Conference
06/18/2025 | Pete Starkey, I-Connect007The European Institute for the PCB Community (EIPC) summer conference took place this year in Edinburgh, Scotland, June 3-4. This is the third of three articles on the conference. The other two cover Day 1’s sessions and the opening keynote speech. Below is a recap of the second day’s sessions.