-
-
News
News Highlights
- Books
Featured Books
- smt007 Magazine
Latest Issues
Current IssueSpotlight on India
We invite you on a virtual tour of India’s thriving ecosystem, guided by the Global Electronics Association’s India office staff, who share their insights into the region’s growth and opportunities.
Supply Chain Strategies
A successful brand is built on strong customer relationships—anchored by a well-orchestrated supply chain at its core. This month, we look at how managing your supply chain directly influences customer perception.
What's Your Sweet Spot?
Are you in a niche that’s growing or shrinking? Is it time to reassess and refocus? We spotlight companies thriving by redefining or reinforcing their niche. What are their insights?
- Articles
- Columns
- Links
- Media kit
||| MENU - smt007 Magazine
Estimated reading time: 5 minutes
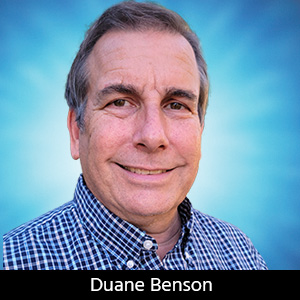
Powerful Prototypes: 5 Common Myths About Solder Mask
Before parts are added, a typical printed circuit board (PCB) has four ingredients: substrate, metal, solder mask, and silkscreen. Each of those four ingredients comes in a host of variations, and each has varying degrees of “requiredness.” All four should be required, but the latter two—especially solder mask—are sometimes seen as primarily aesthetic in nature. Solder mask, in particular, seems to be looked at as a great place to cut when costs are tight, and I resent that thought.
Spending my days in an assembly house, as I do, I regularly see the results of that type of cost-cutting. There was a time when parts were big, PCBs were chiseled with stone tools, and solder mask wasn’t too important, but these days (with 0.4-mm pitch and smaller components being commonplace), it is very important. With that in mind, here are five common myths about solder mask that I will attempt to dispel.
Myth #1
Solder mask is just paint, and details like thickness aren’t important.
Well, that might have been true in 1981, but not now. When you’re dealing with very small parts—such as 0201 or 01005 passive components—thick solder mask may hold the component up high enough so that the metal ends don’t make good contact with the solder paste. If one side makes good contact and the other doesn’t, the surface tension of the melted solder on the side with contact may tug on the part, pulling it up vertical, which is called tombstoning.
Figure 1: Solder mask thickness.
In Example A of Figure 1, the solder mask is thin enough so the part can rest on the paste and will reflow properly. In Example B, the part may rest upon the solder mask and not fully contact the solder paste on one or the other side. This can cause an open or lead to tombstoning, especially if the mask has bumps or variations in the thickness.
Good mask registration will help. Using a board vendor that has tight tolerances and delivers a thin flat mask surface will also help. In some cases, with the smallest parts, you may want to keep the solder mask off the pads. Consider using non-solder mask defined (NSMD) pads. Capacitors and resistors have two leads; both need to be soldered for them to do their job.
Myth #2
As long as your via is not directly on the component land pad, a short bit of distance between the via and the pad is good enough to prevent solder from wicking down the via, so there’s no need to worry about solder mask between the pad and via.
Certainly, lead-free solder, as is common today, wicks less than leaded solder, but that isn’t enough to prevent problems. Solder will spread out from the pad and may wick down the via. If it wicks down the via, your solder joint will likely not have enough solder, and you may get some solder on the far side of the PCB. You need at least a thin line of solder mask between the pad and the via. This is especially important with BGAs where you might have the via very close, but just off the pad between the BGA ball lands.
Myth #3
Solder mask doesn’t affect the solder joint.
Well, that might have been true in—wait, I’ve already used that phrase— so yes, it does affect the solder joint. Component manufacturers calculate land patterns based largely on the amount of solder required to make a reliable electrical and mechanical connection. The solder paste stencil cut-outs are sized to match the land and deposit just the right amount of solder on the pad.
During reflow, the solder will spread out and fill the metal area. When your land pad has traces connected to it, the solder mask is what keeps the solder from spreading out down the trace, which could result in an insufficient solder joint.
Figure 2. Solder mask vs. no solder mask.
In Figure 2, the board on the left has everything the two boards on the right do plus a bit more, and it was also machine assembled. Solder mask is required when using smaller surface-mount parts.
Myth #4
Ball grid arrays (BGAs) always require NSMD pads.
Common theme alert here: What once was true may not always be true anymore. With BGAs that have a ball pitch of 0.5 mm or larger, conventional wisdom says that you need to use NSMD pads. This means that the solder mask opening is larger than the copper pad. The solder paste and BGA ball can sag a little and grip the sides of the round copper pad in addition to the surface of it. Good for big BGAs, but not necessarily for super small BGAs.
With 0.4-mm pitch and smaller BGAs, the NSMD pad will allow the BGA ball to spread out too wide and can lead to bridging. It does depend on the size of the ball and pad, and your component manufacturer should be the ultimate authority on this, but solder mask defined pads are often the way to go with these new super small pitch BGAs. If you don’t have a datasheet that tells you otherwise, use solder mask defined pads with BGAs 0.4-mm pitch and smaller.
Myth #5
Solder mask exists only for utilitarian purposes.
You might think this based on what I’ve written so far, but like so many other things in the world of electronics today, it’s no longer true. A few decades ago, virtually all PCBs were hidden by an enclosure. Today, we see a lot of boards that are open to the air. Most of these exist in the education and development world, but that doesn’t make them any less important.
I’ve always thought that a good PCB layout is a work of art; it’s a bridging of art and science. By careful use of solder mask, choice of color, and the use of silkscreen (not the subject of this column, but it fits here), a designer can express some of their personality and enhance the artistic component of their product.
It may seem frivolous do so at first glance, and many may say that the function is the only important thing. But it’s not form over function, nor function over form. It is that form (good or bad) must not interfere with function. Good engineering is an art form as well as science. If you have the time, go ahead and let it show.
Duane Benson is marketing manager and CTO at Screaming Circuits.
More Columns from Powerful Prototypes
Powerful Prototypes: Small Computer ModulesPowerful Prototypes: A Trip Back to the Basics
Powerful Prototypes: The Work World in 2021
Powerful Prototypes: Why Datasheets Matter
Powerful Prototypes: Manufacturing in an Uncertain World
Powerful Prototypes: An Open-Source Adventure
Powerful Prototypes: Five Technological Shifts in the New Decade
Powerful Prototypes: Cost Reduction in Design