-
- News
- Books
Featured Books
- pcb007 Magazine
Latest Issues
Current IssueThe Hole Truth: Via Integrity in an HDI World
From the drilled hole to registration across multiple sequential lamination cycles, to the quality of your copper plating, via reliability in an HDI world is becoming an ever-greater challenge. This month we look at “The Hole Truth,” from creating the “perfect” via to how you can assure via quality and reliability, the first time, every time.
In Pursuit of Perfection: Defect Reduction
For bare PCB board fabrication, defect reduction is a critical aspect of a company's bottom line profitability. In this issue, we examine how imaging, etching, and plating processes can provide information and insight into reducing defects and increasing yields.
Voices of the Industry
We take the pulse of the PCB industry by sharing insights from leading fabricators and suppliers in this month's issue. We've gathered their thoughts on the new U.S. administration, spending, the war in Ukraine, and their most pressing needs. It’s an eye-opening and enlightening look behind the curtain.
- Articles
- Columns
- Links
- Media kit
||| MENU - pcb007 Magazine
The State of Plating
September 3, 2019 | Marc Ladle, Viking Test Ltd.Estimated reading time: 3 minutes
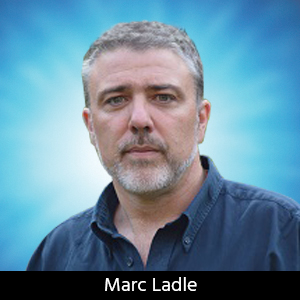
The current market for selling plating lines for panel and pattern plating circuit boards in Europe is not exactly huge. Since I have been involved in selling this type of equipment, the company I work for has probably averaged the sale of one machine per year.
Normally, this has been due to the replacement of completely worn-out equipment or reinstatement of a factory after a fire. Within the last 12 months, we have sold the first line based completely on the requirement for advancing technology. Although this sample group is not large enough to see any real trend, I have a feeling that the European PCB industry is likely to see an increasing demand for machines that can achieve results to meet the demands of the newest ideas for electronic printed circuit design.
Examples
We rarely have a blank canvas to work with. In nearly every case, we must try to fit a quart in a pint pot. Space is the enemy when it comes to integrating the best available new technology into the footprint of the previous 20-year-old plating line. To make matters worse, it is not unusual to be asked to increase the output capacity of the equipment at the same time.
Increasingly, PCB design technology utilises buried and blind via holes and plated via fill is also becoming more and more common. The buried and blind holes mean that the loading on the plating equipment is multiplied by the number of different inner layer connections. The same technology means that equipment needs to deal with thinner and thinner materials.
Plating copper via fill typically means the tank design must be larger, so it takes up more of the valuable space available and takes a long time compared to a traditional throughhole cycle. A typical through-hole plate might take 45–60 minutes where a via hole run could be 3–4 hours.
It is well known that the size of PCB factories in Europe is usually much smaller than the factories in Asia. Typically, this means there is only a single plating line available to production, and this one piece of key equipment must cover every type of work which goes through the factory. Compromises must be made, and usually, it is the work at the extremes of capability that suffer. For example, very thick heavy panels are hard to transport using commonly used top-clamping methods (they can drop out of the clamps unexpectedly). Very thin panels need extra support to stop them folding when they are dipped into the tanks and also to keep them in a stable position in the centre of the tank between the anodes (the plating will be too heavy on the side closer to the anodes and too thin on the side which is further from the anodes). For both problems, simple solutions are available, but the same fix does not suit both extremes at the same time.
The plating chemistry has also advanced when compared to the simple solutions and replenishment additives of years ago. Again, the major problem for smaller manufacturers is the sheer amount of variation in the work they have to put down the line and the fast turn arounds required by customers that prevent them from batching similar work together. The chemistry in a bath can definitely be tuned to provide even plating of a large area, such as panel plating where the whole surface of the panel is plated as well as the through-holes, but the same tuning is likely to make it very difficult to plate isolated details or very small plating areas. In the worst case, the additives have to be stripped out of the solution using a carbon filter and then added again to suit the next requirement.
Solutions and Developments
All of the previous cases are real examples I have come across during the last year, and they are very big problems for the companies involved. In some cases, the only practical solution is a larger factory and a second special-purpose plating line. Development of hardware to meet the needs of the large range of challenges facing the plating operation has recently been quite strong. There are a number of features becoming more commonplace on new equipment and some that could also be retrofitted to existing equipment.
To read the full article, which appeared in the August 2019 issue of PCB007 Magazine, click here.
Suggested Items
Trump Copper Tariffs Spark Concern
07/10/2025 | I-Connect007 Editorial TeamPresident Donald Trump stated on July 8 that he plans to impose a 50% tariff on copper imports, sparking concern in a global industry whose output is critical to electric vehicles, military hardware, semiconductors, and a wide range of consumer goods. According to Yahoo Finance, copper futures climbed over 2% following tariff confirmation.
Happy’s Tech Talk #40: Factors in PTH Reliability—Hole Voids
07/09/2025 | Happy Holden -- Column: Happy’s Tech TalkWhen we consider via reliability, the major contributing factors are typically processing deviations. These can be subtle and not always visible. One particularly insightful column was by Mike Carano, “Causes of Plating Voids, Pre-electroless Copper,” where he outlined some of the possible causes of hole defects for both plated through-hole (PTH) and blind vias.
Trouble in Your Tank: Can You Drill the Perfect Hole?
07/07/2025 | Michael Carano -- Column: Trouble in Your TankIn the movie “Friday Night Lights,” the head football coach (played by Billy Bob Thornton) addresses his high school football team on a hot day in August in West Texas. He asks his players one question: “Can you be perfect?” That is an interesting question, in football and the printed circuit board fabrication world, where being perfect is somewhat elusive. When it comes to mechanical drilling and via formation, can you drill the perfect hole time after time?
The Evolution of Picosecond Laser Drilling
06/19/2025 | Marcy LaRont, PCB007 MagazineIs it hard to imagine a single laser pulse reduced not only from nanoseconds to picoseconds in its pulse duration, but even to femtoseconds? Well, buckle up because it seems we are there. In this interview, Dr. Stefan Rung, technical director of laser machines at Schmoll Maschinen GmbH, traces the technology trajectory of the laser drill from the CO2 laser to cutting-edge picosecond and hybrid laser drilling systems, highlighting the benefits and limitations of each method, and demonstrating how laser innovations are shaping the future of PCB fabrication.
Day 2: More Cutting-edge Insights at the EIPC Summer Conference
06/18/2025 | Pete Starkey, I-Connect007The European Institute for the PCB Community (EIPC) summer conference took place this year in Edinburgh, Scotland, June 3-4. This is the third of three articles on the conference. The other two cover Day 1’s sessions and the opening keynote speech. Below is a recap of the second day’s sessions.