-
- News
- Books
Featured Books
- smt007 Magazine
Latest Issues
Current IssueWhat's Your Sweet Spot?
Are you in a niche that’s growing or shrinking? Is it time to reassess and refocus? We spotlight companies thriving by redefining or reinforcing their niche. What are their insights?
Moving Forward With Confidence
In this issue, we focus on sales and quoting, workforce training, new IPC leadership in the U.S. and Canada, the effects of tariffs, CFX standards, and much more—all designed to provide perspective as you move through the cloud bank of today's shifting economic market.
Intelligent Test and Inspection
Are you ready to explore the cutting-edge advancements shaping the electronics manufacturing industry? The May 2025 issue of SMT007 Magazine is packed with insights, innovations, and expert perspectives that you won’t want to miss.
- Articles
- Columns
- Links
- Media kit
||| MENU - smt007 Magazine
The Long Road to a New Standard
September 17, 2019 | Barry Matties, I-Connect007Estimated reading time: 4 minutes
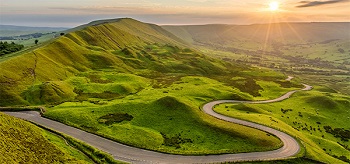
Graham Naisbitt, chairman and CEO of Gen3 Systems, has spent decades leading cleanliness testing standards in a number of different standards organizations like IPC, IEC, and ISO around an assortment of testing methods, such as CAF, SIR, and even introducing a new standard this year for his own testing method—process ionic contamination testing (PICT). Naisbitt breaks down his long involvement with standards and where they stand currently.
Barry Matties: Please start by telling us about your company, Gen3 Systems.
Graham Naisbitt: For nearly 40 years, we have designed, engineered, manufactured, and distributed our test and measurement equipment into the electronics industry. Back in 2009–2010, we lost 50% revenue overnight in the downturn. It was as though somebody flicked a switch. To bolster what we’re doing in the U.K., looking for distribution of other people’s products was a natural extension, so we lined up with two or three key players. Peter Marshall, who was the chairman of the SMART Group (a trade association in the U.K.), was at a crossroads. He had his own distribution business and wanted to retire. Peter and I came to an agreement, and I took over that business, which brought in additional distribution points.
Matties: As you told me earlier, there was one event that changed the course of your work.
Naisbitt: An important point for the industry was when Dr. Wally Rubin, who was then the technical director of a company called Multicore Solders, invented no-clean flux. Wow, that was a success. But how much longer that can continue has now come into question.
Matties: Are there some practical applications that need to be addressed?
Naisbitt: Absolutely. And it’s fair to say that the vast majority of the industry is running successful no-clean processes, but it doesn’t avoid the risks associated with electrochemi cal migration notably, which takes so many different forms.
Matties: And with HDI coming into a stronger play in the market, are we seeing more failures?
Naisbitt: Yes. That was why we became involved with the conformal coating because it helped to protect the circuitry. That was the first introduction I had into what makes electronic circuits reliable. That was the key feature of our business.
I became more involved at that point to figure out how to control the production process. One of the main elements of this is that all fluxes leave residues. Surface insulation resistance (SIR) testing was developed and used to try to evaluate whether it was acceptable or not when you were using a no-clean process. With a new process and test, then you need to develop the standards. In 2007, I finally managed to publish the first meaningful documents, which was the IPC test method, and coincidentally, the IEC standard. From there, we have developed even further. The issue came into play around 2010–2012 as the industry was migrating more into increased packaging density and insulation resistance testing became a necessity if you needed to establish product reliability.
But the question that kept coming back to me is how do you control a process? You can’t use SIR testing because it takes too long and it’s too cumbersome and complex. But what you can do is use that to establish a reliable production process, and then take it from there. You need to be able to measure any mobile ionic species left on the surface that can compromise performance because if you put electricity through a product in a damp environment—and you have ionics present as well as the perfect electrolytic cell—funny stuff happens.
During this time, there was some research into this subject, and a stake was stuck in the ground that said anything above 1.56 micrograms per centimeter squared of sodium chloride equivalent is bad and below is good. Now, unfortunately, the industry started without any hesitation to adopt the term “cleanliness testing,” and it isn’t. It never was.
The challenge is the simplified ion chromatograph test, aka ROSE testing, doesn’t differentiate species; it simply looks at a value of conductivity of the solution as to whether or not it falls within acceptable limits. I have spent 25 years of my life trying to explain this to people. You have to stop thinking of it as a cleanliness test because it isn’t, but it’s an excellent method to control a process.
Around 2013, we received a call from Robert Bosch. They require Six Sigma for their production process. It’s automotive electronics that are ultra-high reliability and safety-critical. We took on the project, and in five years of work, we achieved Six Sigma verification uniquely for the first time in the history of this entire subject. To do this, the instrument needs to be sufficiently capable of detecting changes in the process as fast as possible. We use a merit-to-fit algorithm. It means that we were able to give an accurate go/no-go answer within typically three to five minutes. What we’re looking for are only those mobilizable ionic species. Cleanliness is something entirely different.
Matties: After your five years of work, the current pass-fail approach doesn’t make sense as a standard. What was the response, and how do you carry that change in the standard process to the industry and get support?
Naisbitt: There are two answers to that. One, I’m silly.
Matties: That was a short answer (laughs).
To read the full version of this article which originally appeared in the September 2019 issue of SMT007 Magazine, click here.
Suggested Items
SIA Applauds Passage of Strengthened Semiconductor Investment Credit
07/04/2025 | SIAThe Semiconductor Industry Association (SIA) released the following statement from SIA President and CEO John Neuffer following passage in the U.S. House of Representatives of the One Big Beautiful Bill Act (H.R. 1).
Horizon Sales Celebrates 10 Years of Exceptional Service by Sales Leader David Smith
07/02/2025 | Horizon SalesHorizon Sales, a premier manufacturers’ representative and distributor for the electronics assembly industry, is proud to announce that David Smith is celebrating 10 years with the company this month.
I-Connect007 Editor’s Choice: Five Must-Reads for the Week
06/27/2025 | Nolan Johnson, I-Connect007While news outside our industry keeps our attention occupied, the big news inside the industry is the rechristening of IPC as the Global Electronics Association. My must-reads begins with Marcy LaRont’s exclusive and informative interview with Dr. John Mitchell, president and CEO of the Global Electronics Association. For designers, have we finally reached the point in time where autorouters will fulfill their potential?
Reflections and Priorities: An Update to I-Connect007 Readers
06/24/2025 | Marcy LaRont, I-Connect007The electronics and manufacturing industry is evolving rapidly—with new technologies, deeper global connections, and a growing drive toward sustainability. To reflect these changes and our place in this dynamic space, we’re refreshing our brand.
The Knowledge Base: Building the Workforce of Tomorrow With EMAC
06/24/2025 | Mike Konrad -- Column: The Knowledge BaseAs the electronics manufacturing industry races to meet rising global demand and technological complexity, the need for a highly skilled, future-ready workforce has never been greater. At the forefront of addressing this challenge is The Electronics Manufacturing & Assembly Collaborative (EMAC)—a national initiative dedicated to strengthening the talent pipeline through strategic collaboration with SMTA, education, and government stakeholders.