-
- News
- Books
Featured Books
- smt007 Magazine
Latest Issues
Current IssueWhat's Your Sweet Spot?
Are you in a niche that’s growing or shrinking? Is it time to reassess and refocus? We spotlight companies thriving by redefining or reinforcing their niche. What are their insights?
Moving Forward With Confidence
In this issue, we focus on sales and quoting, workforce training, new IPC leadership in the U.S. and Canada, the effects of tariffs, CFX standards, and much more—all designed to provide perspective as you move through the cloud bank of today's shifting economic market.
Intelligent Test and Inspection
Are you ready to explore the cutting-edge advancements shaping the electronics manufacturing industry? The May 2025 issue of SMT007 Magazine is packed with insights, innovations, and expert perspectives that you won’t want to miss.
- Articles
- Columns
- Links
- Media kit
||| MENU - smt007 Magazine
Combating ESD: The Silent Assassin in Electronics Manufacturing
September 20, 2019 | Neil Sharp, JJS ManufacturingEstimated reading time: 3 minutes
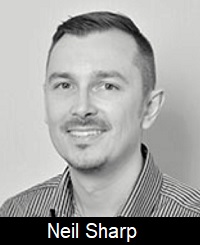
Electrostatic discharge (or ESD) is a major contributor to device failure within electronics manufacturing facilities with industry experts estimating that the average product losses due to static discharge could range anywhere from 8–33%. ESD occurs whenever the electrons on the surface of one object pass onto the surface of another object and cause it to become positively charged.
When those additional electrons come into contact with a differently charged object that allows the passing of electricity, then the result is what is called an ESD event. And ESD events are occurring around us all the time, whether it’s the static sensation we get when removing laundry from a tumble dryer, the sharp shock of touching a metal doorknob after having walked over carpet, or the spectacle of a lightning storm in full force.
In an electronics manufacturing context, however, ESD is a less obvious but far more serious threat, and the level of charge is often so low that manufacturers won’t even realize there is a problem until it is too late. Without proper static control safeguards, these silent electrostatic impulses have the power to zap digital equipment, fry networks, and make short work of circuit boards and microprocessors.
Counting the Cost of ESD
Damage from ESD can affect electronic components in a variety of ways. Sometimes, the damage will be instantaneous and catastrophic, such as in the case of an oxide failure or a metal melt; the device will stop functioning completely. In other cases, though, the effects of ESD can be less obvious, or what’s called a latent defect. When this type of damage occurs, the harm has already been done, but the fault may not be flagged as a problem during a general inspection.
But the device is now destined to malfunction or fail completely at some point over its lifespan. The cost of damage to devices can be anything from a few pennies for a simple diode to hundreds or even thousands of pounds in the case of a more complex electronic circuit. And when you also take into account the associated costs of repair and rework, labor, overheads, and shipping, it’s clear to see why it’s so important to have static control programs in place to mitigate the effects of ESD.
Combating ESD in Electronics Manufacturing
According to the ESD Association, there are six principles to bear in mind when developing an ESD control program.
- Designing in protection by making your products and assemblies as robust as possible in resisting the effects of ESD.
- Identifying the level of control that your environment needs, according to the different classes of sensitivity for the human body model (HBM) and the charged device model (CDM).
- Defining the electrostatic protected areas (EPAs) where you’re most likely to be handling ESD-sensitive parts; typical areas include receiving, inspection, assembly, warehouses, R&D, packing, repairs, laboratories, and cleanrooms.
- Reducing electrostatic charge generation by eliminating or reducing the processes that generate static and by providing suitable ground paths to reduce the generation and accumulation of static charge.
- Implementing grounding, ionization, and conductive/dissipative static control materials from the provision of ESD wrist and heel straps for staff to investing in anti-static mats and flooring, tooling, and ESD-resistant packaging solutions.
- Protecting electronic products from ESD through the use of proper grounding, shunting, and static control material handling products.
Conclusion
ESD is a constant but invisible force within electronics manufacturing that can have a powerfully detrimental impact on production yield, product and product reliability, and company profitability. And as the circuitry within electronic devices continues to get faster, smaller, and more sophisticated, their sensitivity to the effects of ESD is only likely to increase. For electronics manufacturers, the solution lies in the continual development of targeted ESD control programs to identify, define, and mitigate the most sensitive areas—and the most vulnerable processes—within their facilities.
Neil Sharp is the director of marketing for JJS Manufacturing.
Suggested Items
I-Connect007’s Editor’s Choice: Five Must-Reads for the Week
07/04/2025 | Marcy LaRont, I-Connect007For our industry, we have seen several bullish market announcements over the past few weeks, including one this week by IDC on the massive growth in the global server market. We’re also closely watching global trade and nearshoring. One good example of successful nearshoring is Rehm Thermal Systems, which celebrates its 10th anniversary in Mexico and the official opening of its new building in Guadalajara.
Hon Hai Education Foundation Continues to Promote Quantum Education
07/04/2025 | FoxconnHon Hai Education Foundation has long been committed to promoting forward-looking technology education in Taiwan's high schools, and held the "High School Quantum Teacher Training Camp" in Tainan City on July 1.
Incap UK Achieves JOSCAR Zero Accreditation
07/04/2025 | IncapIncap Electronics UK has been accredited under JOSCAR Zero, a new sustainability-focused extension of the defence and aerospace sector’s supplier assurance system.
Kitron Secures Contract for Components Supporting Unmanned Aerial Systems
07/04/2025 | KitronKitron has received a contract with an estimated value between EUR 4 and 8 million for the production and supply of advanced electronic components used in unmanned aerial systems (UAS).
NOTE Receives Order Worth 132 MSEK and Expands Collaboration with Customer within Security & Defense
07/04/2025 | NOTENOTE has received an order worth SEK 132 million from one of its existing customers operating within Security & Defense. NOTE thereby strengthens its long-term collaboration with the industry-leading customer.