IPC Panel on Bottom-terminated Components
September 27, 2019 | Andy Shaughnessy, I-Connect007Estimated reading time: 7 minutes
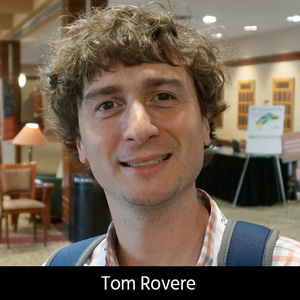
During the IPC Summer Meetings in Raleigh, North Carolina, I sat down with Tom Rovere, a materials and process engineer at Lockheed Martin in Owego, New York. We explored a panel discussion on bottom-terminated components (BTCs) that Tom participated in as well as the challenges and issues related to BTCs and the important role that designers play in that process.
Andy Shaughnessy: Tom, it’s nice to meet you. You were on the BTC panel this morning, which was pretty interesting. Can you give us some background on yourself and how you acquired such a cool bio that says you know all about BTCs?
Tom Rovere: Looking back, I graduated from college with a material science and engineering degree. Then, I moved to Owego, New York, and started working at Lockheed. At that point, I didn’t have any experience with electronics assembly. I was lucky to have some great mentors, and over the past 10+ years of working on the manufacturing line, I’ve learned a great deal about ball grid arrays (BGAs), surface-mount technology, and bottom-terminated components. Over time, you use IPC standards, so I figured that I should start attending some of the IPC conferences. Most recently, I wanted to get more involved, so I kindly emailed the IPC Conference Manager and said, “Put me on a panel!” That’s how I got this opportunity.
Shaughnessy: It was a great panel. Everyone agreed that BTCs are very robust; they’re bulletproof, etc., but they have problems too. We know the pros, but can you talk about some of the cons?
Rovere: My expertise with BTCs is more related to the solder joint reliability and rework. We also had Dave Hillman, who’s probably one of the best industry experts to have on a panel with regards to BTCs and soldering. It was nice having him there because he answered a lot of the questions, and I could sit and nod my head in agreement. The assembly and reflow portion seems to be fairly robust. With mechanical reliability, voiding also doesn’t seem to be an issue either, according to Dave’s data.
Now, we’ve started to look back and think, “What about the cleanliness of these?” With such a low-profile part, it’s not as easy to get cleaning solution into those crevices and under those parts to get residual material out. We joked, saying that one option is to stop using flux, but you can’t do that yet. So, you’re stuck with flux or the byproduct of whatever is left after the soldering process, and you have to get that out. That’s one of the bigger challenges with low-profile parts, such as BTCs.
Now, there are design changes to improve cleanliness. One example we’ve talked about is removing the masking underneath. But at the same time, there’s a trade-off. Removing the masking could potentially create solder bridges underneath the component. When manufacturing, I would rather not remove that masking because it creates a different defect, one that may be more difficult to fix.
Shaughnessy: That’s one of the things where everybody blames or credits the designer, depending on if things go well or poorly. But there were certain things designers can do, like removing the solder mask, as you mentioned.
Rovere: Yes, and there are other issues with those parts as well; a lot of information is run through them, and they tend to get fairly hot on the board, which requires a lot of cooling. The parts are typically cooled through the board with the bottom termination. Unfortunately, since this termination is underneath the part, it’s tough to see an issue before it actually happens.
Shaughnessy: You said that designers would come to you and say, “Well, this one burned up!” And that’s how they know it failed?
Rovere: Right, they’ll say, “This one fried, so we need to take it off and put it back on.” By that time, it’s too late to do any failure analysis.” I wanted to know what the other panelists thought, so even though I was on the panel, I was almost part of the audience because I was interested in learning more and asked the other panelists questions too. For example, I asked, “Is there anything else we can do testing-wise to isolate these issues and screen out these parts before they burn up, and we have to replace them?”
Shaughnessy: Someone pointed out that the designer could play a big part in BTCs.
Rovere: Sometimes, designers need something that manufacturers would not prefer, but if it’s necessary, you have to reach a compromise. A designer might say that the ground pad underneath the BTC must have several vias in it to improve cooling. A manufacturer might ask, “Can we fill those vias with epoxy and plate over them? This will limit potential voiding, but it costs a little bit more money. That’s the compromise you have to make for a better surface underneath, so you don’t lose all of your solder down the vias.” Again, there’s a trade-off between cost, manufacturing, and design.
Page 1 of 2
Suggested Items
BEST Inc. Introduces StikNPeel Rework Stencil for Fast, Simple and Reliable Solder Paste Printing
06/02/2025 | BEST Inc.BEST Inc., a leader in electronic component rework services, training, and products is pleased to introduce StikNPeel™ rework stencils. This innovative product is designed for printing solder paste for placement of gull wing devices such as quad flat packs (QFPs) or bottom terminated components.
See TopLine’s Next Gen Braided Solder Column Technology at SPACE TECH EXPO 2025
05/28/2025 | TopLineAerospace and Defense applications in demanding environments have a solution now in TopLine’s Braided Solder Columns, which can withstand the rigors of deep space cold and cryogenic environments.
INEMI Interim Report: Interconnection Modeling and Simulation Results for Low-Temp Materials in First-Level Interconnect
05/30/2025 | iNEMIOne of the greatest challenges of integrating different types of silicon, memory, and other extended processing units (XPUs) in a single package is in attaching these various types of chips in a reliable way.
E-tronix Announces Upcoming Webinar with ELMOTEC: Optimizing Soldering Quality and Efficiency with Robotic Automation
05/30/2025 | E-tronixE-tronix, a Stromberg Company, is excited to host an informative webinar presented by Raphael Luchs, CEO of ELMOTEC, titled "Optimize Soldering Quality and Efficiency with Robotic Automation," taking place on Wednesday, June 4, 2025 at 12:00 PM CDT.
CE3S Launches EcoClaim Solutions to Simplify Recycling and Promote Sustainable Manufacturing
05/29/2025 | CE3SCumberland Electronics Strategic Supply Solutions (CE3S), your strategic sourcing, professional solutions and distribution partner, is proud to announce the official launch of EcoClaim™ Solutions, a comprehensive recycling program designed to make responsible disposal of materials easier, more efficient, and more accessible for manufacturers.