-
- News
- Books
Featured Books
- pcb007 Magazine
Latest Issues
Current IssueSales: From Pitch to PO
From the first cold call to finally receiving that first purchase order, the July PCB007 Magazine breaks down some critical parts of the sales stack. To up your sales game, read on!
The Hole Truth: Via Integrity in an HDI World
From the drilled hole to registration across multiple sequential lamination cycles, to the quality of your copper plating, via reliability in an HDI world is becoming an ever-greater challenge. This month we look at “The Hole Truth,” from creating the “perfect” via to how you can assure via quality and reliability, the first time, every time.
In Pursuit of Perfection: Defect Reduction
For bare PCB board fabrication, defect reduction is a critical aspect of a company's bottom line profitability. In this issue, we examine how imaging, etching, and plating processes can provide information and insight into reducing defects and increasing yields.
- Articles
- Columns
- Links
- Media kit
||| MENU - pcb007 Magazine
Estimated reading time: 3 minutes
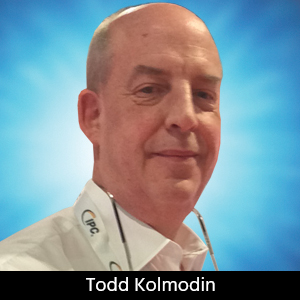
Testing Todd: Understanding the Fine Print
New technologies are emerging each day with more stringent requirements than the past. Also, reversals in obsolescence programs bring products back to the market for which the original documentation and/or requirements are ancient compared to today’s standards; in some cases, this documentation is even lost. Further, it is not uncommon to find that original artwork isn’t available or that the part must be recreated from a finished circuit board sample. This involves learning a netlist profile and then scanning layer by layer to recreate the actual film layers, but that is a whole different subject that I’ll discuss in a future column.
Specifications and Drawings
With specifications and drawings, it gets complicated very quickly. When printed circuits are procured, the purchase order (PO) is sent along with the master drawing and other deliverable requirements. In most cases, this is a straightforward process. The PO states what is being purchased, and the master drawing outlines the specifics and instructions on what is required for the build. Usually, the master drawing will specify industry specifications and requirements, which may include a special OEM specification. This is where it can get tricky, especially for historic or obsolete rebuilds. These old specifications may not be available. Now what? For the fabrication house, this often requires consulting with the OEM and either obtaining the lost document or acquiring a deviation or waiver for the lost document.
Even though the product may be a new build, there’s a chance that the master drawing calls out for an older specification. Diligence is required by the fabrication house to make sure that the proper specification is used. It cannot be assumed that the latest specification and/or methods are to be used. This becomes increasingly important when processing military products. One cannot assume the latest build specification is to be used. Older designs by OEM military contractors may call for older revisions of say MIL-PRF-31032, 55110, and 50884. For electrical test (ET), this can be especially significant.
Advances in test technology have brought new methodologies that were not allowed or even known in the older revisions of specifications. Just because the latest revision of a specification allows the use of these technologies, one cannot assume the new options apply. If an older specification is called, the requirements of that specification shall be used. This can be challenging for a third-party ET contractor.
Many times, the ET contractor may have access to the master drawing only when the order is being processed. Job-specific notes may be added to the ET database for future reference, but special notes may be lost when the job returns to the fabrication house. This is where it is crucial to save the notes or retain a copy of the master drawing. Most ET contractors will have NDAs with their fabrication houses, so this isn’t usually a problem. However, this becomes extremely important when the fabrication house or ET contractor is audited and allows absolute traceability and assurance that the product was built and tested as originally designed.
Certificate of Compliance Documents
This brings up another item that comes up quite frequently on the certificate of compliance (C of C) documents for ET. What specification should appear on the C of C for ET is a confusing topic. A master drawing may state, “Build to IPC-6012D.” Should the ET C of C state IPC-6012D? The answer is no. If the C of C were to say IPC-6012D, it could be interpreted that the ET C of C is certifying the entire build, which it is not; it is only certifying the product was tested.
To read the full article, which appeared in the September 2019 issue of PCB007 Magazine, click here.
More Columns from Testing Todd
Testing Todd: Why 4-wire Kelvin?Testing Todd: Why TDR?
Testing Todd: Positivity Boosts Employee Morale
Testing Todd: Preparing Employees for the Long Haul
Testing Todd: Where Can We Improve?
Testing Todd: Turning Into the Wind
Testing Todd: Coming Back to Life—Design Recovery
Testing Todd: Decision Time—Invest or Delegate?