-
- News
- Books
Featured Books
- pcb007 Magazine
Latest Issues
Current IssueIn Pursuit of Perfection: Defect Reduction
For bare PCB board fabrication, defect reduction is a critical aspect of a company's bottom line profitability. In this issue, we examine how imaging, etching, and plating processes can provide information and insight into reducing defects and increasing yields.
Voices of the Industry
We take the pulse of the PCB industry by sharing insights from leading fabricators and suppliers in this month's issue. We've gathered their thoughts on the new U.S. administration, spending, the war in Ukraine, and their most pressing needs. It’s an eye-opening and enlightening look behind the curtain.
The Essential Guide to Surface Finishes
We go back to basics this month with a recount of a little history, and look forward to addressing the many challenges that high density, high frequency, adhesion, SI, and corrosion concerns for harsh environments bring to the fore. We compare and contrast surface finishes by type and application, take a hard look at the many iterations of gold plating, and address palladium as a surface finish.
- Articles
- Columns
Search Console
- Links
- Media kit
||| MENU - pcb007 Magazine
Estimated reading time: 1 minute
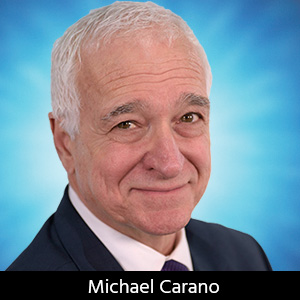
Contact Columnist Form
Trouble in Your Tank: Working With Flexible Circuits
Flexible circuits were first introduced as a replacement for wire harnesses. The earliest versions date back to World War II. Today, flex and rigid-flex circuits are filling an important role across multiple industries, including applications in the medical, automotive, and telecommunications fields.
Even though they are a smaller part of the circuit board industry, flex and rigid-flex circuits have been growing in popularity over the last decade, and for good reasons. These circuits are made to be thin, flexible, and durable. However, in addition to the opportunities that come with flex and rigid-flex circuits, there are also challenges. Generally, these occur with the processing part of the technology.
Characteristics of Flex and Rigid-flex Circuits
Flex and rigid-flex circuits have become a go-to solution for a variety of applications because they offer capabilities that simply aren’t available from alternatives. They can be manufactured to very thin specifications, and they will survive bending and folding without error.
These circuits can be run over long distances to make a connection. For example, some users have designed 14–18-foot flexible cables.
Some of the most sought-after features of flex and rigid-flex circuits include the following:
- Thin-core capability
- Improved dielectric constant
- Low dielectric constant (Dk) and dissipation factor (Df) critical concerns
- Ultra-fine line capable (L/S decreasing to less than 15 microns)
- Shorter interconnect distances
Flexible circuits have the same capabilities of their rigid counterparts, including repeatability, reliability, and high density. In addition, they have characteristics that make them more versatile than rigid circuits. For example, they are flexible, of course, and can resist vibration more effectively. One of the most popular features of flexible circuits is that they can be designed into three-dimensional configurations.
Rigid-flex circuits combine the best features of flexible and rigid circuits to meet a variety of needs. The rigid areas make it possible to mount stationary components while the flexible areas can be custom configured and serve as protection against vibration.
Despite the fact that flex boards can be extremely thin, they are remarkably durable. These circuits are capable of repeating the same bends through millions of cycles without interruption. This is a critical point when it comes to applications that face intense vibration and/or acceleration.
To read the full article, which appeared in the September 2019 issue of PCB007 Magazine, click here.
More Columns from Trouble in Your Tank
Trouble in Your Tank: Yield Improvement and ReliabilityTrouble in Your Tank: Causes of Plating Voids, Pre-electroless Copper
Trouble in Your Tank: Organic Addition Agents in Electrolytic Copper Plating
Trouble in Your Tank: Interconnect Defect—The Three Degrees of Separation
Trouble in Your Tank: Things You Can Do for Better Wet Process Control
Trouble in Your Tank: Processes to Support IC Substrates and Advanced Packaging, Part 5
Trouble in Your Tank: Materials for PWB Fabrication—Drillability and Metallization
Trouble in Your Tank: Supporting IC Substrates and Advanced Packaging, Part 5