-
- News
- Books
Featured Books
- smt007 Magazine
Latest Issues
Current IssueSupply Chain Strategies
A successful brand is built on strong customer relationships—anchored by a well-orchestrated supply chain at its core. This month, we look at how managing your supply chain directly influences customer perception.
What's Your Sweet Spot?
Are you in a niche that’s growing or shrinking? Is it time to reassess and refocus? We spotlight companies thriving by redefining or reinforcing their niche. What are their insights?
Moving Forward With Confidence
In this issue, we focus on sales and quoting, workforce training, new IPC leadership in the U.S. and Canada, the effects of tariffs, CFX standards, and much more—all designed to provide perspective as you move through the cloud bank of today's shifting economic market.
- Articles
- Columns
- Links
- Media kit
||| MENU - smt007 Magazine
Mycronic Demonstrates Expanded Portfolio of Products at productronica 2019
October 27, 2019 | PR NewswireEstimated reading time: 3 minutes
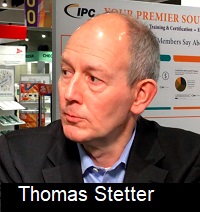
For the first time since multiple acquisitions in recent years, Mycronic AB will demonstrate its full portfolio of electronics assembly solutions at productronica in Munich, November 12-15, 2019. In addition to the latest integrated SMT line, jet printing, dispensing, 3D inspection and material handling solutions, the company will highlight its industry-leading automotive camera module assembly and high-precision die bonding solutions.
Enhancing quality, flexibility and productivity
As electronics assembly continues to grow more complex, Mycronic will be showcasing more ways than ever before to improve quality, flexibility and productivity in a range of electronics manufacturing applications. PCB manufacturers will experience new advances in machine-to-machine communication, full SMT line capabilities and automated material handling systems. Automotive electronics manufacturers will gain expertise in the industry-leading Camera Module Assembly and Test (CMAT) system. And manufacturers of advanced photonic and radio-frequency devices will learn more about the industry's first 1.5 micron die bonder for high-precision, high-volume manufacturing.
"All of these state-of-the-art solutions are part of our vision to enable zero-defect assembly with the highest utilization for any product mix," says Thomas Stetter, Sr. VP, Assembly Solutions. "From integrated SMT production lines to advanced packaging and automotive sensors, our aim is to enhance our customers' control over the data, processes and material flows that matter most to their success."
New production insights with enhanced M2M communication
As an active member of the Hermes Standard Initiative, the majority of Mycronic's machine models will now be Hermes compliant. This standardized machine-to-machine communication protocol represents an important step in enabling customers to look beyond discrete manufacturing process steps and gain holistic insights into factory-wide productivity. It will also allow greater vendor-independent capabilities, enabling customer processes and programming to become increasingly driven by board requirements.
Full SMT line solution with expanded capabilities
The recently launched MYPro Line, the company's latest full SMT line solution, will demonstrate a number of new software and automation capabilities at productronica. The SIGMA Link software, which correlates data between solder paste inspection and automated optical inspection, now features more intuitive process controls to further improve inspection efficiency and first pass yield. A new AOI platform with 2x faster programming. A new solder paste inspection and jet printing repair system closes several data feedback loops to automatically increase yield and product quality over time. And a new dashboard and analysis software will demonstrate new ways to simplify production scheduling and enhance overall equipment effectiveness.
New advances in conformal coating and plasma treatment
As part of Mycronic's rapidly evolving MYSmart series of dispensing and conformal coating robots, a number of new hardware and software innovations will be on display at productronica 2019. The industry-leading MYC50 conformal coating system, with its new intuitive user interface, precision spray valve and flow monitoring system, promises to deliver even higher levels of precision, repeatability and yield. In addition, a new series of MYS plasma systems will be launched. The MYS systems offer all the benefits of traditional vacuum plasma systems at atmospheric pressure, with safer, cleaner operations and up to 50 times faster cleaning speeds.
Collaborative robotics for autonomous material handling
In a significant step towards improving labor utilization, Mycronic will also demonstrate a next-generation collaborative robotics system. The solution, developed in collaboration with industry-leading partners, will show the potential for entirely operator-independent retrieval, kitting and distribution of component reels.
High-performance automotive camera module assembly
In addition to these new SMT capabilities, Mycronic will also present the manufacturing solutions and experts behind the industry-leading CMAT system. The millions of sensor modules assembled every year by manufacturers using this system are enabling enhanced automotive safety and, ultimately, autonomous driving. Mycronic's process experts will answer questions regarding design for manufacturing, rapid prototyping, application enhancement and full-scale manufacturing optimization.
Advanced die bonding systems
Finally, visitors to productronica will have the opportunity to learn about the industry's leading high-precision die bonding systems for flexible high-speed assembly of optoelectronics and microelectronics. Mycronic's die bonding experts will be on hand to discuss their complete, cost-effective assembly solutions for all levels of advanced packaging.
To experience live demos and to learn more about Mycronic's MYPro Line, CMAT, die bonding and other assembly solutions, visit Booth A3 341 at productronica in Munich, November 12-15, 2019.
Contact at Mycronic: mycronic.com.
Testimonial
"Advertising in PCB007 Magazine has been a great way to showcase our bare board testers to the right audience. The I-Connect007 team makes the process smooth and professional. We’re proud to be featured in such a trusted publication."
Klaus Koziol - atgSuggested Items
Indium Promotes Huang to Senior Manager, Marketing Communications
08/28/2025 | Indium CorporationWith its commitment to innovation and growth through employee development, Indium Corporation announces the promotion of Jingya Huang to Senior Manager, Marketing Communications, to continue to lead the company’s branding and promotional efforts.
Rehm Academy Expands Its Training Program
08/28/2025 | Rehm Thermal SystemsThe demands on modern industrial companies and employees continue to rise, and therefore, the topic of further education is becoming increasingly important today.
MacDermid Alpha Awarded for Innovation: Driving Process Optimization and Efficiency with Major Indian EMS Provider
08/28/2025 | MacDermid Alpha Electronics SolutionsMacDermid Alpha Electronics Solutions, a leading global supplier of integrated materials for the electronics industry, is recognized by one of India’s top EMS providers, Syrma SGS, with an award for innovation that advanced process optimization, enhanced operational efficiency, and yield gains.
Integrated Solutions for Board-level Reliability: A Smarter Path Forward
08/27/2025 | Alan Gardner, MacDermid Alpha Electronics SolutionsIn today’s electronics manufacturing landscape, reliability is no longer just a benchmark but a business imperative. As industries such as automotive, aerospace, and high-performance computing (HPC) push the boundaries of innovation, the demand for dependable board-level performance under extreme conditions has never been greater.
ZESTRON Expands Capabilities with Addition of the EPS by i-Tech AG 75 Pallet Cleaning System
08/26/2025 | ZESTRONZESTRON, the global leader in high-precision cleaning solutions and services, is excited to announce the addition of a new capability in its Technical Center in Manassas, VA: