-
- News
- Books
Featured Books
- smt007 Magazine
Latest Issues
Current IssueSupply Chain Strategies
A successful brand is built on strong customer relationships—anchored by a well-orchestrated supply chain at its core. This month, we look at how managing your supply chain directly influences customer perception.
What's Your Sweet Spot?
Are you in a niche that’s growing or shrinking? Is it time to reassess and refocus? We spotlight companies thriving by redefining or reinforcing their niche. What are their insights?
Moving Forward With Confidence
In this issue, we focus on sales and quoting, workforce training, new IPC leadership in the U.S. and Canada, the effects of tariffs, CFX standards, and much more—all designed to provide perspective as you move through the cloud bank of today's shifting economic market.
- Articles
- Columns
- Links
- Media kit
||| MENU - smt007 Magazine
Saki to Showcase AOI Solutions for Ensuring Soldering Quality at Productronica 2019
November 1, 2019 | Saki CorporationEstimated reading time: 2 minutes
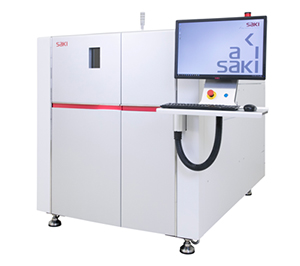
Saki Corporation, an innovator in the field of automated optical and X-ray inspection and measurement equipment, introduces a compact, lightweight, inline 3D-CT automated X-ray inspection machine, the 3Xi-M110, for inspection of printed circuit board assemblies (PCBAs). The 3Xi-M110 reduces the dose and exposure to X-rays during inspection and features new soldering quality inspection functions for PCB assembly applications. Saki will demonstrate the PCB inspection capabilities of the 3Xi-M110 at productronica 2019, being held in Munich, Germany from November 12-15, in stand A2.259.
Saki's new X-ray inspection system ensures the quality of hidden solder joints for bottom-electrode packages, such as BGAs, LGAs, and QFNs, which are found in advanced embedded devices, telecommunications, and automotive products. Saki's Planar Computed Tomography (PCT) provides precise volumetric measurements and shape reconstruction to find voids, head-in-pillow (HiP), and other defects that are extremely difficult to identify.
The 3Xi-M110 hardware platform is 1,380mm wide and weighs 3,100kg, making it 40% lighter and reducing its footprint by 25% over its predecessor. Manufacturing floorspace is saved, it's easy to install, and production-line operation is significantly improved. Although the cast iron frame is lighter in weight, it maintains the rigidity needed for stable operation and accuracy, while the imaging range has been optimized to handle board sizes up to 360 x 330mm (W x L). For larger 360 x 510mm (W x L) boards, 2-step image capture is available.
The 3Xi-M110 delivers exceptional speed and accuracy by utilizing a double motor-driven system equipped with a high-precision linear scale manufactured by Magnescale Co., Ltd. to optimize power and precision. Saki's enhanced PCT technology algorithm improves image capture speed by 30%, reducing production-line takt time.
One of the most significant features of the new system is Saki's revolutionary X-ray tube, which can reduce X-ray exposure up to 70% by powering on the X-rays only at the moment of image capture. An exposure dose simulator allows the user to monitor the radiation dose. Based on that information, the method and magnification for releasing the X-rays can be set. The new X-ray tube design does not require periodic maintenance or spare parts, and the built-in monitoring system reports when the tube needs replacing.
"In the automotive and communications industries, where quality assurance is important, the effectiveness of high-precision, high-quality PCB X-ray inspection has become critical," said Masahide Iino, director and head of the sales division of Saki Corporation. "Saki will continue to respond to the needs of the market by leveraging the accumulated knowledge and experience it has gained through its history as a leading innovator in the field of 2D/3D automated optical inspection and X-ray inspection."
For more information on the 3Xi-M110, please contact Saki at pr@sakicorp.com, or visit our website at www.sakicorp.com or www.sakiglobal.com.
Testimonial
"In a year when every marketing dollar mattered, I chose to keep I-Connect007 in our 2025 plan. Their commitment to high-quality, insightful content aligns with Koh Young’s values and helps readers navigate a changing industry. "
Brent Fischthal - Koh YoungSuggested Items
Indium Promotes Huang to Senior Manager, Marketing Communications
08/28/2025 | Indium CorporationWith its commitment to innovation and growth through employee development, Indium Corporation announces the promotion of Jingya Huang to Senior Manager, Marketing Communications, to continue to lead the company’s branding and promotional efforts.
Rehm Academy Expands Its Training Program
08/28/2025 | Rehm Thermal SystemsThe demands on modern industrial companies and employees continue to rise, and therefore, the topic of further education is becoming increasingly important today.
MacDermid Alpha Awarded for Innovation: Driving Process Optimization and Efficiency with Major Indian EMS Provider
08/28/2025 | MacDermid Alpha Electronics SolutionsMacDermid Alpha Electronics Solutions, a leading global supplier of integrated materials for the electronics industry, is recognized by one of India’s top EMS providers, Syrma SGS, with an award for innovation that advanced process optimization, enhanced operational efficiency, and yield gains.
Integrated Solutions for Board-level Reliability: A Smarter Path Forward
08/27/2025 | Alan Gardner, MacDermid Alpha Electronics SolutionsIn today’s electronics manufacturing landscape, reliability is no longer just a benchmark but a business imperative. As industries such as automotive, aerospace, and high-performance computing (HPC) push the boundaries of innovation, the demand for dependable board-level performance under extreme conditions has never been greater.
ZESTRON Expands Capabilities with Addition of the EPS by i-Tech AG 75 Pallet Cleaning System
08/26/2025 | ZESTRONZESTRON, the global leader in high-precision cleaning solutions and services, is excited to announce the addition of a new capability in its Technical Center in Manassas, VA: