Samsung Receiving Industry’s First Global Recognition for Environmental Sustainability
December 3, 2019 | Samsung Electronics Co., Ltd.Estimated reading time: 1 minute
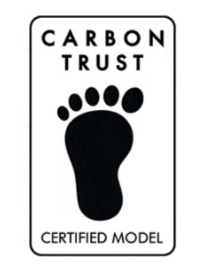
Samsung Electronics, a world leader in advanced memory technology, announced that its 512-gigabyte (GB) embedded Universal Flash Storage (eUFS) 3.0 was awarded Carbon Footprint and Water Footprint Certifications from the highly respected UK-based Carbon Trust during a ceremony at the British Embassy in Seoul, Korea. Samsung’s 512GB eUFS 3.0 is the first mobile memory in the industry to be recognized by an international certifying organization, which was made possible through the company’s extensive efforts to reduce carbon and water footprints.
The Carbon Trust is a globally accredited non-profit certification body established by the British government to accelerate the move to a sustainable, low-carbon economy. Each certification by the Carbon Trust was made after a thorough assessment of the environmental impact of carbon emissions and water usage before and throughout the production cycle, based on international standards*.
“We are extremely pleased that our cutting-edge memory technologies not only demonstrate our capability to overcome more challenging process complexities, but also are recognized for their environmental sustainability,” said Chanhoon Park, executive vice president and head of Giheung Hwaseong Pyeongtaek Complex at Samsung Electronics. “Samsung will continue to create memory solutions that provide the highest levels of speed, capacity and power efficiency at extremely small geometries for end-users worldwide.”
Samsung’s Semiconductor Innovations Enable Sustainable Production
Based on the company’s fifth-generation (90+ layers) V-NAND, Samsung’s 512GB eUFS 3.0 provides optimal speed, power efficiency and productivity to deliver twice the capacity and 2.1 times the sequential speed of its fourth generation (64 layers) V-NAND-based 256GB eUFS 2.1, while requiring 30 percent less operating voltage. Additionally, Samsung’s fifth-generation V-NAND utilizes a unique etching technology that pierces more than 90 cell layers in a single precise step. This allows the chip to have nearly 1.5 times more stacked layers than the previous generation and accommodate a 25-percent reduction in chip size. Such innovations help to minimize the overall increase in carbon and water footprints for each V-NAND cell layer.
Samsung is also being awarded Environmental Product Declaration (EPD) labels for its ‘1-terabyte (TB) eUFS 2.1’ and its ‘fifth-generation 512-gigabit (Gb) V-NAND’ by the Korean Ministry of Environment at today’s ceremony.
Samsung plans to actively expand the adoption of its highly sustainable, high-capacity premium memory solutions into many more flagship smartphones and further strengthen global partnerships for its next-generation memory technologies.
Suggested Items
The Chemical Connection: Through-glass Vias in Glass Substrates
06/24/2025 | Don Ball -- Column: The Chemical ConnectionThis month’s theme is vias and how best to ensure via quality and reliability. I don’t have much expertise in this process area or much to contribute that most of you don’t already know. However, I’ve recently become peripherally involved in a via technology that may be of more than academic interest to some of us. It entails putting vias in a material not usually associated with PCB manufacturing: through-glass vias (TGVs) in glass substrates.
In Pursuit of Perfection: Defect Reduction—May 2025 PCB007 Magazine Now Available
05/15/2025 | I-Connect007 Editorial TeamFor bare PCB board fabrication, defect reduction is a critical aspect of a company's bottom line profitability. In the May 2025 issue of PCB007 Magazine, we examine the imaging, etching, and plating processes, as well as product traceability on the shop floor, providing information and insight into how you can reduce your defects and increase yields.
DuPont to Showcase Advanced Semiconductor Wet Etching Innovations at the Surface Preparation and Cleaning Conference
05/13/2025 | DuPontDuPont announced that it will present its latest developments in semiconductor wet etching technologies at the upcoming Surface Preparation and Cleaning Conference (SPCC) in Chandler, Arizona, beginning May 20.
The Chemical Connection: Common Misconceptions in Wet Processing
04/28/2025 | Don Ball -- Column: The Chemical ConnectionInitially, I thought an April Fool’s column would be fun this month. I could highlight some of the crazier ideas and misconceptions I’ve witnessed over the years from potential customers and we could all have a good laugh. For example, there was a first-time buyer of a ferric chloride etcher (with no regeneration system) who was astonished to learn that he had to put fresh etchant in the system occasionally to maintain production.
Lam Research Donates Leading-Edge Etch System to Accelerate Nanofabrication R&D at UC Berkeley
04/17/2025 | PRNewswireLam Research Corp. announced the donation of its innovative multi-chamber semiconductor etching system to the Marvell Nanofabrication Laboratory at the University of California, Berkeley to advance research and development (R&D) for next-generation chip technologies.