-
- News
- Books
Featured Books
- smt007 Magazine
Latest Issues
Current IssueWhat's Your Sweet Spot?
Are you in a niche that’s growing or shrinking? Is it time to reassess and refocus? We spotlight companies thriving by redefining or reinforcing their niche. What are their insights?
Moving Forward With Confidence
In this issue, we focus on sales and quoting, workforce training, new IPC leadership in the U.S. and Canada, the effects of tariffs, CFX standards, and much more—all designed to provide perspective as you move through the cloud bank of today's shifting economic market.
Intelligent Test and Inspection
Are you ready to explore the cutting-edge advancements shaping the electronics manufacturing industry? The May 2025 issue of SMT007 Magazine is packed with insights, innovations, and expert perspectives that you won’t want to miss.
- Articles
- Columns
- Links
- Media kit
||| MENU - smt007 Magazine
Reliability Testing in Automotive and Digital Factories
December 11, 2019 | Barry Matties, I-Connect007Estimated reading time: 10 minutes
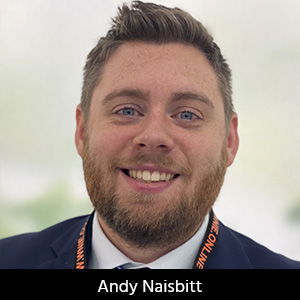
Barry Matties spoke with Gen3’s Andrew Naisbitt about what readers should know about SIR and CAF testing, what to consider if you’re thinking of bringing it in-house, and how reliability testing fits into automotive and the digital factory.
Barry Matties: Andy, why don’t you start with a little bit about Gen3 and what you do.
Andrew Naisbitt: We manufacture equipment that tests reliability in electronics, so we focus on aspects such as solderability testing, surface insulation resistance (SIR) testing, and conductive anodic filament (CAF) testing as well as our ionic contamination testers. We also have our Gensonic stencil cleaning center that has proved to be very popular in America.
Matties: You’re selling the equipment, and a lot of the services would be your largest customers. Do you see OEMs?
Naisbitt: It’s quite mixed. We have a wide variety of customers and we have 41 distributors looking after our stuff around the world. We sell into all sorts of different industries and we’re finding ourselves a lot with some of the large board manufacturers. Reliability in testing is so critical in the industry, and we do a lot to help with that as well.
Matties: Reliability is a huge and growing issue as we see with autonomous vehicles, aerospace advancements, etc. If you were to tell somebody what they really need to know about reliability testing, what would that be?
Naisbitt: There’s quite a significant amount. The critical nature is always going to be in the circuits and how reliable the circuits are. You need to know if it is going to last. The test methods that we build for are for hypercritical stuff used by companies from aviation to automotive. There’s a lot of work on standards being done right now and changes being made; we need to focus our time and attention and know where the industry is going. There’s going to be more of a need for SIR and CAF testing with high-voltage testing, especially for automotive. You should ensure that those tests are done in the right way to enable you to have a far more accurate understanding of how reliable your products are that you’re building on the boards.
Matties: If someone thinks they need reliability testing, to set it up and bring it in-house, what do they need to know?
Naisbitt: First, you need to validate your products, so make sure you have a benchmark. With J-STD-001, there has always been a number of 1.56 micrograms of sodium chloride per centimeter squared on your board, so that has been the pass-fail limit. If you’re looking into the reliability, that limit is now gone. The pass-fail limit has been rendered obsolete in the standards. You need to make sure that you validate your process in terms of what numbers are you going to get from your boards or what are you going to do with the terms of the reliability. Then, you need to use process control tools to enable you to reliably reproduce the results that you get. There are two essential steps: validation, and then making sure that your production line is using the data that you get from the validation.
Matties: As companies consider digital factories, and they begin to come online, how does testing fit into that?
Naisbitt: We have a lot of customers who ask us the same sort of questions. The pass-fail limit number I mentioned has always been on the shop floor. What we do has traditionally always been in the labs, and we provide a lot of data. There are all sorts of graphs. It’s quite analytical and very different from having a red light/green light situation. We’re finding more and more and looking at what we’re developing with our products moving forward. New tests might come out, but it’s going to take a long time. The industry would appreciate another yes/no question on the shop floor, but whether or not that’s a realistic scenario, I don’t know because the testing doesn’t really do that at this moment in time.
Matties: When you consider real-time testing as the board is produced, it’s a good or bad kind of thing, in simple terms. When you look at reliability testing currently, do they test every single board or a panel from a lot?
Naisbitt: With SIR and CAF testing, they test coupons, which are representative of their final product. But the future of it will need to be production boards as well. As I said, there are different test methods that we’re developing. It’s an exciting time. I can’t say too much in terms of what we’re looking to move toward but based on where we think the industry is going with electric vehicles, etc., testing will change and need to become quicker and easier. Trying to balance science and what people want can be tricky.
Matties: When you look at autonomous vehicles, reliability is critical because it’s not just one passenger that could be injured; it’s potentially groups of people.
Naisbitt: Absolutely.
Matties: So, it better be right. I would think that the OEMs in such situations would want every board tested if possible, in a cost-effective way.
Naisbitt: From my point of view, it’s both yes and no. We’re talking hundreds of thousands of millions of boards being produced.
Matties: That’s where I’m looking to the future. If you’re looking at an inline situation and it was available, what would you say?
Naisbitt: There are so many different tests and ways to measure reliability. We only do a small fraction of the ones out there, and the processes that companies have at the moment, the likelihood is there’s nothing wrong with them. But with more development going into smaller and smaller components, you have to look at your testing, including how to do it and where to improve. And it’s the same for us as the manufacturer of those pieces of equipment and the tests and types of testing; you have to move with the time. In the future, maybe you will test the board, but maybe there will be a test that makes life even easier than it necessarily is right now.
Matties: That’s what you’re working toward.
Naisbitt: We have some good ideas floating around.
Matties: With the digital factory, lot sizes of one, and recipe-driven manufacturing, that makes sense. But I don’t know all the economics behind it from an investment cycle time process.
Naisbitt: It’s such a huge topic, and we’re making significant industry advancements. It’s a big change to go from fossil fuels to electric vehicles, and they’re looking at developing some crazy things with airplanes, so who knows where we will go. But there’s so much education that needs to be done, and people need to learn it’s not as simple as some might think.Page 1 of 2
Suggested Items
S&K Aerospace Awarded Major Contract Under DLA Maritime Acquisition Advancement Program
07/02/2025 | BUSINESS WIRES&K Aerospace, LLC has been awarded a significant contract under the Defense Logistics Agency’s (DLA) Maritime Acquisition Advancement Program, managed by the U.S. Naval Supply Command - Weapon Systems Support (NAVSUP WSS) in Mechanicsburg, PA.
Green Circuits to Exhibit Full-Service Electronics Manufacturing Solutions at 2025 SMD Symposium
07/02/2025 | Green CircuitsGreen Circuits, a full-service Electronics Manufacturing Services (EMS) partner to leading OEMs, is pleased to announce its participation in the 2025 SMD Symposium, taking place August 5-7 at the Von Braun Center in Huntsville, Alabama.
I-Connect007 Editor’s Choice: Five Must-Reads for the Week
06/27/2025 | Nolan Johnson, I-Connect007While news outside our industry keeps our attention occupied, the big news inside the industry is the rechristening of IPC as the Global Electronics Association. My must-reads begins with Marcy LaRont’s exclusive and informative interview with Dr. John Mitchell, president and CEO of the Global Electronics Association. For designers, have we finally reached the point in time where autorouters will fulfill their potential?
Knocking Down the Bone Pile: Tin Whisker Mitigation in Aerospace Applications, Part 3
06/25/2025 | Nash Bell -- Column: Knocking Down the Bone PileTin whiskers are slender, hair-like metallic growths that can develop on the surface of tin-plated electronic components. Typically measuring a few micrometers in diameter and growing several millimeters in length, they form through an electrochemical process influenced by environmental factors such as temperature variations, mechanical or compressive stress, and the aging of solder alloys.
RTX, the Singapore Economic Development Board Sign MOU Outlining 10-year Growth Roadmap
06/20/2025 | RTXRTX and the Singapore Economic Development Board (EDB) have signed a Memorandum of Understanding (MoU) which outlines a 10-year roadmap to further long-term strategic collaboration in Singapore.