-
- News
- Books
Featured Books
- pcb007 Magazine
Latest Issues
Current IssueIn Pursuit of Perfection: Defect Reduction
For bare PCB board fabrication, defect reduction is a critical aspect of a company's bottom line profitability. In this issue, we examine how imaging, etching, and plating processes can provide information and insight into reducing defects and increasing yields.
Voices of the Industry
We take the pulse of the PCB industry by sharing insights from leading fabricators and suppliers in this month's issue. We've gathered their thoughts on the new U.S. administration, spending, the war in Ukraine, and their most pressing needs. It’s an eye-opening and enlightening look behind the curtain.
The Essential Guide to Surface Finishes
We go back to basics this month with a recount of a little history, and look forward to addressing the many challenges that high density, high frequency, adhesion, SI, and corrosion concerns for harsh environments bring to the fore. We compare and contrast surface finishes by type and application, take a hard look at the many iterations of gold plating, and address palladium as a surface finish.
- Articles
- Columns
Search Console
- Links
- Media kit
||| MENU - pcb007 Magazine
Estimated reading time: 1 minute
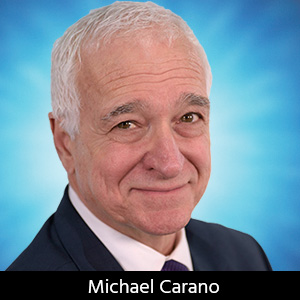
Contact Columnist Form
Trouble in Your Tank: Changes and Concerns Regarding HDI Technology
One does not have to look too far back to point out some significant changes that have taken place in our industry over the past few years. Processes, materials, equipment, and board designs continue to change. If I were to pick one to focus on for this column, it would be in the ever-increasing trends toward higher circuit density. This relates to finer lines and spaces, smaller diameter blind vias, and even multilevel stacked and staggered vias. All of these changes will continue to place significant pressures on bare PCB fabricators to increase their investment and onboard new and critical skill sets.
What Is Driving These Changes?
The semiconductor packaging industry is driving changes to higher density for both the bare board as well as IC substrates, system integration, SiP, and very large-scale integration (VLSI). Increased device complexity has been a primary driving factor for future designs. To keep the component package size small, component lead spacing was decreased. Further increases in semiconductor integration (VLSI), requiring more than 196 I/Os, can drive packages to even closer perimeter lead spacing such as 0.5 mm, 0.4 mm, 0.3 mm, and 0.25 mm. The array package format has become standard for high I/O count devices. To support these requirements, wiring density is increased.
To read this entire column, which appeared in the November 2019 issue of PCB007 Magazine, click here.
More Columns from Trouble in Your Tank
Trouble in Your Tank: Yield Improvement and ReliabilityTrouble in Your Tank: Causes of Plating Voids, Pre-electroless Copper
Trouble in Your Tank: Organic Addition Agents in Electrolytic Copper Plating
Trouble in Your Tank: Interconnect Defect—The Three Degrees of Separation
Trouble in Your Tank: Things You Can Do for Better Wet Process Control
Trouble in Your Tank: Processes to Support IC Substrates and Advanced Packaging, Part 5
Trouble in Your Tank: Materials for PWB Fabrication—Drillability and Metallization
Trouble in Your Tank: Supporting IC Substrates and Advanced Packaging, Part 5