UV-curable Materials and Conformal Coatings
December 23, 2019 | Pete Starkey, I-Connect007Estimated reading time: 7 minutes
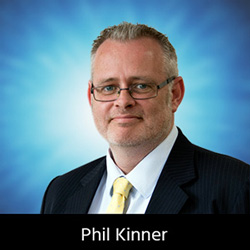
During productronica 2019, Pete Starkey and Phil Kinner, global business and technical director, coatings division, Electrolube, discuss the characteristics and benefits of the company’s new UV-cured conformal coatings. Phil also describes the development of coatings for critical avionics applications and Electrolube’s collaboration with the U.K. National Physical Laboratory to establish a new condensation test.
Pete Starkey: Phil, thanks for joining me. It’s lovely to see you again.
Phil Kinner: It’s always a pleasure, Pete.
Starkey: Thank you. I understand you have some new coatings launching at productronica.
Kinner: We have. Our focus this year is on UV-curable materials. As a process, UV curing offers a lot of benefits, predominantly the speed of cure and low energy consumption. At productronica, we’re showing two of these materials. We have two live demonstrations with two different selective coating machines, PVA and Asymtek, running new products UVCL-P and UVCL-X. With these types of UV curable materials, traditionally, there have been issues with secondary curing, where areas that don’t see the UV light don’t cure if they’re shielded by taller components, or there’s material on the back side of component leads, for example. It needs a secondary curing mechanism.
Starkey: Like a secondary thermal curing mechanism to back-up the UV cure.
Kinner: It could be thermal or moisture-initiated, but traditionally, it’s more moisture-driven. The issue is that it can take a long time for moisture to get through the cured coating to initiate that reaction. We’ve seen issues in the field where it has taken months, and sometimes years, for the material to be fully cured; in sensitive applications, that can be a problem if the material properties keep changing.
Starkey: Can you give me some examples of sensitive applications?
Kinner: For example, when sensors are trying to detect a signal, and the electrical properties of the material keep changing—even just a little bit—then if the sensor is sufficiently sensitive to those changes in electrical properties, once it’s been calibrated and the electrical properties change, it’s out of calibration. We’ve had situations with people who have had 20–30 days of stop time while they’re waiting for the material properties to stop changing before they could do the final calibration and ship their product. Thirty days for a work in progress; who wants that?
With the new materials, we’ve worked hard to get materials that will cure in a reasonable timeframe. These materials we’re showing will fully cure within six hours after exposure to UV. They’ll cure with conventional microwave or arc-lamp systems or LEDs at 365 nanometers, which is unusual; most materials cure with one or the other, so having the flexibility of curing with both is a big advantage. LEDs use a lot less power and have a lot longer life, so it seems to be the technology of the future, but it brings some challenges for conventional materials, such as getting them to cure to be tack-free; then, you still have the secondary issues with which to deal.
Starkey: With the demonstrations that you’re running live here at the show, what assemblies are you coating?
Kinner: We mocked up some demo boards that have a variety of discretes and an IC on them to simulate some of the components that we know are difficult to coat well so that we can demonstrate the better edge coverage and protection that we’re able to achieve on a real-looking assembly rather than just flat pieces of FR-4. That’s what we use during the development of our products, so it’s easy for us to use that in the show.
Starkey: With the thicknesses that you’re putting down, and the corrosion resistance that you’re achieving, are these materials good for aerospace-type applications, or would you suggest something different?
Kinner: I don’t think the aerospace industry really needs the fast-curing and throughput that you get with UV-curable materials, so these materials are more suitable for larger volume producers such as automotive and industrial controls. The aerospace industry is more concerned with protection and performance.
Starkey: They just want reliability.
Kinner: Right, so we have an application for the primary flight control electronics for Boeing and Airbus that is more suited to the thermal curing 2K range of materials.
Starkey: What conditions do these things have to withstand?
Kinner: To save weight and reduce costs, customers are moving away from hermetically-sealed housings. And these electronics are in non-airconditioned parts of the airplane, so when they’re up high, they probably hit -40 or -50°C, and when they land in Asia, they start warming up, and the humidity condenses dramatically, causing a lot of errors.
Starkey: I would imagine that presents you with a few challenges from the point of offering them a high-reliability coating.
Kinner: Correct. In that case, it’s all about coverage and thickness. Some of the other two-component materials that we have are better choices. We have a product 2K300 that is very hydrophobic. It’s very insensitive to being wet, and in this customer’s case, it was the best material they tested out of the 14 candidates they looked at. The mission requirement from the OEM, which was quite scary for me as an air traveler, was that the flight control system had to work for 30 minutes or more after landing. To me, that means that it didn’t previously! In this case, when they tested the flight controllers, they had one incident in an hour of their condensation testing where the unit went out of its range, and that was 58 minutes into the cycle. The best other material lasted around 15 minutes before it showed a failure, and there were 20–30 failures during that time. The existing materials they were using showed somewhere in the range of 20,000 failures during the hour-long test.
Starkey: That sounds very impressive, Phil. One critical thing in that application is that the coating must be continuous. However resistant the material is, it has to be everywhere protecting the surface. What application methods do you use to ensure that you have complete coverage?
Kinner: In this customer’s case, and with most customers, they use selective coating techniques. We’ve developed a couple of techniques from the process side so that we can guarantee better coverage and thickness. But one of the limitations with traditional materials is not necessarily getting it on thick, but what that thick coating does to the component and to itself during thermal cycles. With a lot of materials, if you get it on too thick, it’s going to crack, or it will crack solder joints.
Starkey: Are you looking at the tensile properties of the coating itself?
Kinner: Right. And with these materials, the idea was to apply them thick so that all of the development and testing we’ve done has been with that thick, well-covered board in mind. The materials had been designed from the ground up to be applied thick, which gives you a lot more choices because often, if you try to get it thick in critical areas, you get it super-thick in other areas, which can create problems. You’re trying to get it uniform at a certain thickness. It’s a combination of the process that we’ve developed as well as the material chemistry and how it applies as well.
Starkey: You have to match the thermal expansion characteristics to the substrate so that when it expands and contracts, it’s not pulling the substrate to pieces.
Kinner: That’s pretty much the key thing. But condensation was the big challenge, and that’s what the materials are developed for. We see more and more cases where condensation testing is becoming a critical part of the performance profile. As soon as things get wet with traditional materials, they fail almost instantaneously.
Starkey: I know that the National Physical Lab has been doing a lot of work on condensation testing. Have you been collaborating with them?
Kinner: Yes, we have. We helped them initially with the development of test methods. We wrote a co-paper with them, showing some results and materials that we’d given them, with all sorts of different factors to ensure they had a robust test. Now, there’s an industry project running; we’re a partner in that and waiting on their results.
Starkey: Hopefully, this test will be adopted as an industry standard.
Kinner: That would be great because all of the different OEMs have their own version of the condensation test. They’re all kind of the same, but they’re a little bit different too. Having one standardized test would make life easier for everybody.
Starkey: It has been great to talk to you, Phil. Thanks for your time.
Kinner: You too, Pete.
Suggested Items
BEST Inc. Introduces StikNPeel Rework Stencil for Fast, Simple and Reliable Solder Paste Printing
06/02/2025 | BEST Inc.BEST Inc., a leader in electronic component rework services, training, and products is pleased to introduce StikNPeel™ rework stencils. This innovative product is designed for printing solder paste for placement of gull wing devices such as quad flat packs (QFPs) or bottom terminated components.
See TopLine’s Next Gen Braided Solder Column Technology at SPACE TECH EXPO 2025
05/28/2025 | TopLineAerospace and Defense applications in demanding environments have a solution now in TopLine’s Braided Solder Columns, which can withstand the rigors of deep space cold and cryogenic environments.
INEMI Interim Report: Interconnection Modeling and Simulation Results for Low-Temp Materials in First-Level Interconnect
05/30/2025 | iNEMIOne of the greatest challenges of integrating different types of silicon, memory, and other extended processing units (XPUs) in a single package is in attaching these various types of chips in a reliable way.
E-tronix Announces Upcoming Webinar with ELMOTEC: Optimizing Soldering Quality and Efficiency with Robotic Automation
05/30/2025 | E-tronixE-tronix, a Stromberg Company, is excited to host an informative webinar presented by Raphael Luchs, CEO of ELMOTEC, titled "Optimize Soldering Quality and Efficiency with Robotic Automation," taking place on Wednesday, June 4, 2025 at 12:00 PM CDT.
CE3S Launches EcoClaim Solutions to Simplify Recycling and Promote Sustainable Manufacturing
05/29/2025 | CE3SCumberland Electronics Strategic Supply Solutions (CE3S), your strategic sourcing, professional solutions and distribution partner, is proud to announce the official launch of EcoClaim™ Solutions, a comprehensive recycling program designed to make responsible disposal of materials easier, more efficient, and more accessible for manufacturers.