-
- News
- Books
Featured Books
- pcb007 Magazine
Latest Issues
Current IssueThe Hole Truth: Via Integrity in an HDI World
From the drilled hole to registration across multiple sequential lamination cycles, to the quality of your copper plating, via reliability in an HDI world is becoming an ever-greater challenge. This month we look at “The Hole Truth,” from creating the “perfect” via to how you can assure via quality and reliability, the first time, every time.
In Pursuit of Perfection: Defect Reduction
For bare PCB board fabrication, defect reduction is a critical aspect of a company's bottom line profitability. In this issue, we examine how imaging, etching, and plating processes can provide information and insight into reducing defects and increasing yields.
Voices of the Industry
We take the pulse of the PCB industry by sharing insights from leading fabricators and suppliers in this month's issue. We've gathered their thoughts on the new U.S. administration, spending, the war in Ukraine, and their most pressing needs. It’s an eye-opening and enlightening look behind the curtain.
- Articles
- Columns
- Links
- Media kit
||| MENU - pcb007 Magazine
Four Reasons to Choose Polycapillary Optics for XRF Coatings Analysis
January 29, 2020 | Hitachi High-Tech Analytical Science AmericaEstimated reading time: 3 minutes
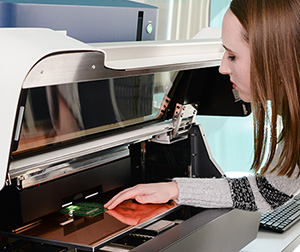
As electronics and electronic components continue to shrink and increase in complexity, metal finishes on these components need to be plated onto smaller features—as thinner layers—with tighter controlled tolerances. If finishes are too thin, the product won’t meet performance specifications and could fail prematurely, risking warranty claims, safety and damage to reputation. If platings are too thick, the cost of plating material increases and money is wasted, plus there are possible issues with mechanical fit of the plated components that could result in costly scrap or rework.
X-ray fluorescence (XRF) is a widely used technique for measuring coating thickness and material composition because it’s non-destructive, fast and straightforward to use. To measure coatings on small features, traditional XRF instruments use a mechanical collimator to reduce the beam size of the X-ray tube down to fractions of a millimeter. This is achieved through the instrument by placing a metal block, with a small hole drilled through it, in front of the X-ray tube, allowing only the X-rays aligned with the hole to pass through and reach the sample. Using this method, a vast majority of the X-ray tube output cannot be used for analysis, as it’s stopped by the collimator block.
Figure 1: A comparison of the collimator and capillary methods.
Today’s approach to address the need to measure fine features is to use a polycapillary optic. This type of focusing optic is comprised of arrays generated from thousands of small and hollow glass tubes which are curved and tapered. Using this method XRF can easily accommodate a wide variety of geometries relative to the complexity and miniaturization of components which typically need to be plated within the electronics industry. Within a polycapillary optic, the X-rays are guided through the tubes using reflection, which is very similar to the way light is guided in fiber-optic technology. The polycapillary optic is paired to a micro-spot X-ray tube to collect more of the tube’s output. This focuses it onto smaller areas with flux that is orders of magnitude greater than that of a mechanically collimated system. Polycapillary optics in XRF coatings analyzers have several advantages:
Figure 2: Chart detailing how a polycapillary optic functions.
1. Smaller Feature Measurement
Polycapillary optics have a beam size of less than 20 µm, making it possible to measure ultra-fine features on microelectronics, advanced circuit boards, connectors, lead frames and wafers. This allows measurement of areas that can’t be achieved with the traditional mechanical collimators.
2. Thinner Coatings Measurement
By focusing more X-ray tube output onto the sample, an XRF analyzer fitted with a polycapillary optic can measure nanometer-scale coatings and measure thicker coatings with better precision.
3. Increased Testing Throughput with Higher Confidence
A greater intensity generated by the optic results in higher count rates. In XRF, higher count rates translate into improved precision and faster results. This allows for more measurements to be taken in any given time period and higher confidence in the results, leading to better quality control and tighter production.
4. Easier Conformity to Specifications
XRF plays an essential role in determining and controlling finish thickness to meet with performance specifications IPC-4552A for ENIG (electroless nickel immersion gold) and IPC-4556 for ENEPIG (electroless nickel electroless palladium immersion gold). In using XRF to meet the required specifications, analyzers must demonstrate performance levels within a defined tolerance. Using a capillary optic makes it easier to achieve this performance level and allows operations to run as close as possible to the minimum control limits, saving money on materials and chemicals. With recent advances in software, it is now possible to simultaneously measure the thickness and composition of electroless nickel coatings under gold and palladium, assuming these layers are thin enough to allow X-ray transmission.
Combining a polycapillary optic with a high-resolution detector such as a silicon drift detector (SDD), plus a high-precision stage, high-definition camera and clever software provides the ultimate analysis of ultra-fine coatings on ultra-fine features.
SPONSORED LINK
Learn more about Hitachi XRF Analysers.
Suggested Items
The Global Electronics Association Releases IPC-8911: First-Ever Conductive Yarn Standard for E-Textile Application
07/02/2025 | Global Electronics AssociationThe Global Electronics Association announces the release of IPC-8911, Requirements for Conductive Yarns for E-Textiles Applications. This first-of-its-kind global standard establishes a clear framework for classifying, designating, and qualifying conductive yarns—helping to address longstanding challenges in supply chain communication, product testing, and material selection within the growing e-textiles industry.
IPC-CFX, 2.0: How to Use the QPL Effectively
07/02/2025 | Chris Jorgensen, Global Electronics AssociationIn part one of this series, we discussed the new features in CFX Version 2.0 and their implications for improved inter-machine communication. But what about bringing this new functionality to the shop floor? The IPC-CFX-2591 QPL is a powerful technical resource for manufacturers seeking CFX-enabled equipment. The Qualified Product List (QPL) helps streamline equipment selection by listing models verified for CFX compliance through a robust third-party virtual qualification process.
The Knowledge Base: A Conference for Cleaning and Coating of Mission-critical Electronics
07/08/2025 | Mike Konrad -- Column: The Knowledge BaseIn electronics manufacturing, there’s a dangerous misconception that cleaning and coating are standalone options, that they operate in different lanes, and that one can compensate for the other. Let’s clear that up now. Cleaning and conformal coating are not separate decisions. They are two chapters in the same story—the story of reliability.
Advancing Aerospace Excellence: Emerald’s Medford Team Earns Space Addendum Certification
06/30/2025 | Emerald TechnologiesWe’re thrilled to announce a major achievement from our Medford, Oregon facility. Andy Abrigo has officially earned her credentials as a Certified IPC Trainer (CIT) under the IPC J-STD-001 Space Addendum, the leading industry standard for space and military-grade electronics manufacturing.
Magnalytix and Foresite to Host Technical Webinar on SIR Testing and Functional Reliability
06/26/2025 | MAGNALYTIXMagnalytix, in collaboration with Foresite Inc., is pleased to announce an upcoming one-hour Webinar Workshop titled “Comparing SIR IPC B-52 to Umpire 41 Functional & SIR Test Method.” This session will be held on July 24, 2025, and is open to professionals in electronics manufacturing, reliability engineering, and process development seeking insights into new testing standards for climatic reliability.