-
- News
- Books
Featured Books
- smt007 Magazine
Latest Issues
Current IssueMoving Forward With Confidence
In this issue, we focus on sales and quoting, workforce training, new IPC leadership in the U.S. and Canada, the effects of tariffs, CFX standards, and much more—all designed to provide perspective as you move through the cloud bank of today's shifting economic market.
Intelligent Test and Inspection
Are you ready to explore the cutting-edge advancements shaping the electronics manufacturing industry? The May 2025 issue of SMT007 Magazine is packed with insights, innovations, and expert perspectives that you won’t want to miss.
Do You Have X-ray Vision?
Has X-ray’s time finally come in electronics manufacturing? Join us in this issue of SMT007 Magazine, where we answer this question and others to bring more efficiency to your bottom line.
- Articles
- Columns
Search Console
- Links
- Media kit
||| MENU - smt007 Magazine
Global Automotive Leader AW Europe Invests in Class-Leading Yamaha Solder Paste Printing Capability
March 3, 2020 | YAMAHA SMT SectionEstimated reading time: 3 minutes
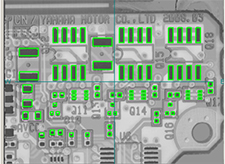
AW, part of the global Aisin Group, researches, develops, and manufactures cutting-edge automotive infotainment systems and electronically controlled automatic transmissions. The company serves major European and Asian carmakers that place extremely high requirements on every unit produced by their partners.
Today’s car drivers interact with their vehicles extensively through the infotainment system, including configuring the many preferences and settings, and receiving navigation and driver assistance continuously while on the move. Electronic automatic transmission control units (ATCUs) must deliver driver satisfaction as well as controlling emissions. Both types of systems are critically connected with the vehicle-ownership experience, demanding not only advanced design but also faultless production quality and reliability.
AW Europe, located in Braine l’Alleud (Brussels) for development and administration, builds the electronic control boards for the systems in-house using state-of-the-art surface-mount assembly lines in its Baudour plant (Mons) where most operational activities are based. Production quality meet stringent customer specifications while business pressures also demand high productivity. To be sure of the best results from the very beginning of assembly, the company installed two Yamaha YSP solder-paste printers, aided by Theo Loohuis and his team at Europe-SMT, Yamaha’s appointed sales representative for Belgium, Netherlands and Luxembourg. After experiencing excellent results, including the outstanding speed and accuracy of the on-board 2D inspection system, the team purchased two more YSP printers for other lines in the factory.
New Investment for Quality and Productivity
“Our surface-mount assembly capabilities significantly influence the quality of our products, so we simply must have the best,” comments the team of AW Europe operations improvement and manufacturing engineers. “We need flexibility and fast product changeovers, to handle anything from prototype requirements from our R&D department, to rapid NPI, and full production. The Yamaha YSP printer has delivered superior ease of use, speed, repeatability, and automated features that save time setting up and programming the machines. It is also extremely reliable.”
The Yamaha YSP printer contains advanced features to assist setup and enhance process control. Leveraging graphical base layer alignment, the stencil and board are quickly aligned within ± 10µm (6?) for perfect paste on pad. The unique 3S Swing Single Squeegee head attack angle setting ensures the perfect filling of stencil apertures and excellent paste-volume repeatability. Automatic detection of remaining solder-paste quantity enables fast and easy refill by the Print Stability Control (PSC) system to ensure constant paste volume for excellent repeatability and minimise paste loss. In addition, automatic stencil cleaning at the optimum interval keeps the stencil surface clean and apertures clear to deliver perfect printed boards every time.
Printing Quality Control by 2D Inspection Camera
The Yamaha YSP printer contains a 2D inspection camera with a large field of view (30mm x 22.5mm) that can inspect the complete printed board with minimum impact on cycle time. With fast image capturing methods that leverage unique Yamaha inspection technology, the complete printing cycle time including inspection is faster than the mounting cycle times in each line. The inspection camera has a LED dome containing three annular rings at different angles, each containing LEDs of two different colours, to illuminate the complete board without shadows. At every view it captures two images with one top light and one side light. This gives a 2.5D inspection result due to excellent contrast between the solder paste, the board surface, and the solder pads. Comprehensive inspection modes include paste positioning, paste volume, bridging, and excess paste on pad.
By testing the Yamaha YSP built-in 2D inspection capability against the inline 3D SPI machines already in place, the team at AW Europe confirmed the performance is just as fast and thorough as a dedicated standalone inspection system. This gave them confidence to rely on the Yamaha YSP printer’s 2D camera and inspection system, and save the burden of running additonal SPI machines in the lines.
“2D inspection with the Yamaha YSP printer delivers the same high level of solder-paste inspection capability as we had before, allowing us to provide the same, excellent quality assurance,”agrees Ludovic Anciaux, Senior Operations Improvement Engineer.
Easy Access to Superior Capability
Impressed overall by the simplicity of the acquisition process, supported by Yamaha and Europe-SMT from the first equipment evaluations and help to choose the most suitable features and options, to delivery, setup, and operator training, he adds, “The service and support has been excellent, the equipment was installed and ready to use extremely quickly, and the machines are so reliable and intuitive that we have become highly proficient and productive in a very short space of time. Every experience has confirmed we made the right decision.”
Suggested Items
Preventing Surface Prep Defects and Ensuring Reliability
06/10/2025 | Marcy LaRont, PCB007 MagazineIn printed circuit board (PCB) fabrication, surface preparation is a critical process that ensures strong adhesion, reliable plating, and long-term product performance. Without proper surface treatment, manufacturers may encounter defects such as delamination, poor solder mask adhesion, and plating failures. This article examines key surface preparation techniques, common defects resulting from improper processes, and real-world case studies that illustrate best practices.
Breaking Silos with Intelligence: Connectivity of Component-level Data Across the SMT Line
06/09/2025 | Dr. Eyal Weiss, CybordAs the complexity and demands of electronics manufacturing continue to rise, the smart factory is no longer a distant vision; it has become a necessity. While machine connectivity and line-level data integration have gained traction in recent years, one of the most overlooked opportunities lies in the component itself. Specifically, in the data captured just milliseconds before a component is placed onto the PCB, which often goes unexamined and is permanently lost once reflow begins.
BEST Inc. Introduces StikNPeel Rework Stencil for Fast, Simple and Reliable Solder Paste Printing
06/02/2025 | BEST Inc.BEST Inc., a leader in electronic component rework services, training, and products is pleased to introduce StikNPeel™ rework stencils. This innovative product is designed for printing solder paste for placement of gull wing devices such as quad flat packs (QFPs) or bottom terminated components.
See TopLine’s Next Gen Braided Solder Column Technology at SPACE TECH EXPO 2025
05/28/2025 | TopLineAerospace and Defense applications in demanding environments have a solution now in TopLine’s Braided Solder Columns, which can withstand the rigors of deep space cold and cryogenic environments.
INEMI Interim Report: Interconnection Modeling and Simulation Results for Low-Temp Materials in First-Level Interconnect
05/30/2025 | iNEMIOne of the greatest challenges of integrating different types of silicon, memory, and other extended processing units (XPUs) in a single package is in attaching these various types of chips in a reliable way.