-
- News
- Books
Featured Books
- pcb007 Magazine
Latest Issues
Current IssueIn Pursuit of Perfection: Defect Reduction
For bare PCB board fabrication, defect reduction is a critical aspect of a company's bottom line profitability. In this issue, we examine how imaging, etching, and plating processes can provide information and insight into reducing defects and increasing yields.
Voices of the Industry
We take the pulse of the PCB industry by sharing insights from leading fabricators and suppliers in this month's issue. We've gathered their thoughts on the new U.S. administration, spending, the war in Ukraine, and their most pressing needs. It’s an eye-opening and enlightening look behind the curtain.
The Essential Guide to Surface Finishes
We go back to basics this month with a recount of a little history, and look forward to addressing the many challenges that high density, high frequency, adhesion, SI, and corrosion concerns for harsh environments bring to the fore. We compare and contrast surface finishes by type and application, take a hard look at the many iterations of gold plating, and address palladium as a surface finish.
- Articles
- Columns
Search Console
- Links
- Media kit
||| MENU - pcb007 Magazine
Estimated reading time: 1 minute
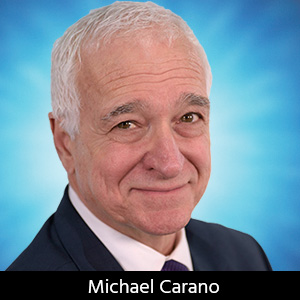
Contact Columnist Form
Trouble in Your Tank: Conductive Anode Filament (CAF) Formation
Editor's note: Mike Carano has since published a follow-up column titled "CAF Formation: Correction of Misrepresentation of Origins and Causes."
Introduction
There are two additional concerns fabricators must understand and reconcile as the circuit technology continues on the high-density curve along with the plethora of new materials to meet the technological demands: conductive anode filament (CAF) formation and wicking.
CAF Versus Wicking
While both issues may lead to electrical failure in a PCB, there are some subtle differences worth mentioning. In addition, CAF is typically related to the resin and glass material while wicking is more process related. More about wicking in a future column.
CAF commonly occurs between adjacent vias (i.e., plated through-holes) inside a PCB, as the copper migrates along the glass/ resin interface from anode to cathode. CAF failures can manifest as current leakage, intermittent electrical shorts, and even dielectric breakdown between conductors in PCBs. This often makes CAF very difficult to detect, especially when it occurs as an intermittent issue.
There are a few things that can be done to isolate the fault location and confirm CAF as a root cause of a failure. If the issue is intermittent then putting the sample of interest under combined temperature-humidity-bias (THB) may help re-create the failure mode. In addition, techniques such as cross-sectioning can be used to identify the failure.
CAF is caused by the glass fiber and the dielectric resin separating from each other within the laminate material itself. This is sometimes seen as a hollow glass fiber (Figure 1) that acts as a conduit, allowing process chemistry and moisture to travel along the opening. Moisture and ionic residues can access the void and enable conductive copper filament growth along the glass fiber reinforcement, leading to shorts.
To read this entire column, which appeared in the April 2020 issue of PCB007 Magazine, click here.
More Columns from Trouble in Your Tank
Trouble in Your Tank: Yield Improvement and ReliabilityTrouble in Your Tank: Causes of Plating Voids, Pre-electroless Copper
Trouble in Your Tank: Organic Addition Agents in Electrolytic Copper Plating
Trouble in Your Tank: Interconnect Defect—The Three Degrees of Separation
Trouble in Your Tank: Things You Can Do for Better Wet Process Control
Trouble in Your Tank: Processes to Support IC Substrates and Advanced Packaging, Part 5
Trouble in Your Tank: Materials for PWB Fabrication—Drillability and Metallization
Trouble in Your Tank: Supporting IC Substrates and Advanced Packaging, Part 5