-
- News
- Books
Featured Books
- smt007 Magazine
Latest Issues
Current IssueWhat's Your Sweet Spot?
Are you in a niche that’s growing or shrinking? Is it time to reassess and refocus? We spotlight companies thriving by redefining or reinforcing their niche. What are their insights?
Moving Forward With Confidence
In this issue, we focus on sales and quoting, workforce training, new IPC leadership in the U.S. and Canada, the effects of tariffs, CFX standards, and much more—all designed to provide perspective as you move through the cloud bank of today's shifting economic market.
Intelligent Test and Inspection
Are you ready to explore the cutting-edge advancements shaping the electronics manufacturing industry? The May 2025 issue of SMT007 Magazine is packed with insights, innovations, and expert perspectives that you won’t want to miss.
- Articles
- Columns
- Links
- Media kit
||| MENU - smt007 Magazine
‘Coatings Uncoated!’ Micro-webinar Series Review
May 4, 2020 | Pete Starkey, I-Connect007Estimated reading time: 5 minutes
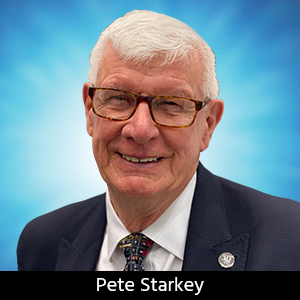
What’s a micro webinar? Divide a complicated technological topic into a logical sequence of concise, focused sections delivered online by a recognised expert, and you have an effective formula for transferring knowledge in clear-cut increments to a wide audience. I-Connect007 collaborated with Electrolube’s Phil Kinner to create a 12-part series of 5-minute micro-webinar sessions entitled “Coatings Uncoated!” offering the opportunity to gain a comprehensive basic understanding of the technology of conformal coatings, chemical types and application techniques, benefits and limitations, and the practicalities of where and how to use them. These were published as a weekly series between January and March this year, and the whole set is now available to view on-demand here.
I spent a remarkably informative and enlightening hour watching and listening. I thought I had begun with a reasonable knowledge of conformal coating technology; I realise now how little I actually knew! I am still no expert, but I am now considerably better educated as a result.
A highly respected name and a familiar face throughout the global electronics industry, Phil Kinner is the acknowledged expert on conformal coatings. Global business and technical director of Electrolube’s International Conformal Coatings Division, instrumental in the development and commercialisation of an extensive product range, hands-on applications specialist and trouble-shooter, prolific technical author and columnist, Kinner demonstrated his capability as an articulate and expressive presenter. And not as a disembodied voice behind a PowerPoint presentation, but continuously in view as a live teacher, with his bullet-point slides, graphics, and video illustrations expertly spliced into the picture by the production team.
In his introduction, Kinner explained the general characteristics of conformal coatings: thin polymer coatings designed to improve the reliability of electronic assemblies in hostile working environments by protecting metal surfaces from corrosion, providing additional dielectric reinforcement and tin whisker mitigation. He grouped coatings into three general types—solvent-based, water-based, and 100% solids—and listed the seven generic categories recognised in the IPC-CC-830C qualification and performance specification: acrylic (AR), epoxy (ER), silicone (SR), polyurethane (UR) paraxylylene (XY), ultra-thin coatings (UT) and styrene block co-polymer (SC). Kinner summarised principal characteristics, typical uses, and levels of protection offered by each type, with suggestions as to choosing an appropriate material for a particular job.
How to apply the coating? Kinner stressed the importance of making an appropriate choice of the application process in achieving adequate coverage and determining the effectiveness of the coating and described a range of techniques—from the basic paint-brush to dipping and spraying and the most sophisticated automated selective methods. The choice depended on factors, such as board design, coating material, cycle time, production line constraints, and quality requirements.
Kinner went on to discuss some aspects of corrosion resistance “Corrosion science is complicated, but the impacts are easy to understand—premature failure.” Ironically, the surface of a working circuit board assembly often carried all of the basic prerequisites for corrosion to occur: dissimilar metals, an external voltage bias, ionic species, and moisture. Cleaning could take away the ionic species, and in an ideal world, would result in a corrosion-resistant board; although, without protection, it would still be vulnerable to corrosion from external sources. Thus, a combination of cleaning and coating was advocated, but only if the coating was complete and continuous. Tin whiskering was another undesirable phenomenon that could be mitigated, provided the coverage was complete and the thickness was sufficient.
Referring to “the three Cs”—clearance, creepage, and coatings—Kinner explained the difference between clearance and creepage and demonstrated that a properly applied coating could allow substantial reductions in spacing between conductors, although practical considerations necessitated a trade-off between design rules and manufacturability.
“Datasheets don’t necessarily tell the whole story,” Kinner cautioned, taking acrylic conformal coatings as an example. “They’re not all created equally.” He particularly referred to differences in adhesion and permeability in the context of long-term reliability.
In a series of case studies, he described some real examples. A telecoms customer had experienced field failures on circuits with an immersion silver finish and a silicone conformal coating, resulting in what was initially believed to be silver sulphide creep corrosion. In fact, it was found that the silver plating was not continuous; sulphur gases were penetrating the silicone coating and forming a corrosion cell with the exposed copper. Changing to an acrylic coating overcame the problem.
A second example was in flight control avionics, showing faults related to condensation on assemblies chilled from flying at high altitude. Working in cooperation with the National Physical Laboratory, different two-component coating chemistries had been compared using a combination of condensation testing and surface-insulation-resistance testing. A new generation of two-component materials, mixed immediately before automated spray application, had been shown to provide better coverage, greater thickness, and improved protection in harsh environments.
A customer using a UL-recognised acrylic coating applied from an aerosol can was seeing field failures associated with arcing and creepage. Kinner explained the significance of the terminology used on UL Yellow Cards. “Minimum coating thickness” was measured on a flat test-piece, which was not representative of component leads, and multiple coats were needed to achieve an acceptable thickness in these critical areas.
An automotive engine management system had traditionally been coated with a solvent-based acrylic, but this was considered a fire hazard in production and was replaced with a non-flammable, UV-cured material. After two years’ service, excessive cracking of solder joints was observed as a consequence of the mechanical properties of the coating changing with time. Technology transfer could lead to problems as well. A dip-coating process established in one automotive factory was replaced with selective spray coating when production was transferred to another facility, and the material subsequently had to be re-formulated to overcome problems with bubbles and capillary flow. Kinner’s advised seeking the advice of the supplier before changing the application process.
In his closing summary, Kinner made it clear that successful conformal coating required the right combination of material selection and application process, and not all conformal coating materials were created equally. Design was an important consideration, the end application must be understood, and potential failure mechanisms must be considered. And it should never be assumed that a material would work in a different application method. “Test, test, and test again,” were his final words.
Thank you, Phil Kinner and the I-Connect007 production team. I enjoyed the “Coatings Uncoated!” content and micro-webinar format, learned a lot from it, and would recommend it to engineers involved in design, assembly, and quality assurance.
Download your free copy of Electrolube's book, The Printed Circuit Assembler's Guide to… Conformal Coatings for Harsh Environments, and watch the micro webinar series “Coatings Uncoated!”