-
- News
- Books
Featured Books
- pcb007 Magazine
Latest Issues
Current IssueInventing the Future with SEL
Two years after launching its state-of-the-art PCB facility, SEL shares lessons in vision, execution, and innovation, plus insights from industry icons and technology leaders shaping the future of PCB fabrication.
Sales: From Pitch to PO
From the first cold call to finally receiving that first purchase order, the July PCB007 Magazine breaks down some critical parts of the sales stack. To up your sales game, read on!
The Hole Truth: Via Integrity in an HDI World
From the drilled hole to registration across multiple sequential lamination cycles, to the quality of your copper plating, via reliability in an HDI world is becoming an ever-greater challenge. This month we look at “The Hole Truth,” from creating the “perfect” via to how you can assure via quality and reliability, the first time, every time.
- Articles
- Columns
- Links
- Media kit
||| MENU - pcb007 Magazine
Estimated reading time: 3 minutes
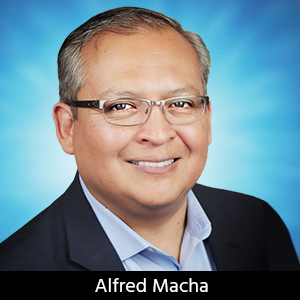
Operational Excellence: Update Your Business Contingency Plan
With the unprecedented events associated with COVID-19, companies are facing worst-case scenarios and looking at ways to manage work stoppage or limited production for essential manufacturing needs. This column provides a practical guideline to create or update your business contingency plan to help you manage your business during a crisis situation.
An effective business contingency plan consists of two categories: business continuity and disaster recovery. Business continuity provides you a structure to identify critical functions in the organization required to execute your business plan over time. On the other hand, a disaster recovery plan is a process to help your organization navigate adverse situations to help your business stay afloat.
Business Continuity
Business continuity consists of seven essential elements in a manufacturing organization.
1. Governance: Define the roles and responsibilities of executive leadership. Define a back-up plan in case you have departures of leaders in the organization.
2. Personnel: Define talent acquisition and development of employees. The objective is to retain top performers and continuously develop skills in the workforce.
3. Manufacturing Facilities: This section covers many areas within manufacturing operations. At a minimum, identify all key equipment and back-up plans in case of malfunction and requirements to continue to have utilities, equipment maintenance, compliance with regulations, and security to support operations.
4. Technology Roadmap: Define current and future process capabilities. Identify the direction that the organization plans to take to sustain or increase revenue based on competitive technological advantages. Consider including the protection of intellectual property.
5. Supply Chain: Securing a supply chain to meet current and future business demands is paramount. Identify all key vendors and possible new vendor qualifications to confirm that the supply of components, raw materials, and sub-assemblies is secure to ensure continuity of your operations.
6. Information Systems: Develop a solid data storage back-up system and establish external support to maintain your information systems. The ongoing development of information technologies requires partnering with a reputable vendor that can support your information technology systems as new software applications are made available.
7. Customer Management: Develop customer management processes to secure key accounts for your business. Include a business development plan to acquire new strategic business for future growth.
Disaster Recovery
Disaster recovery planning is risk-based and can have multiple factors to consider. The recommended approach is to prepare a table based on specific risks and define a risk mitigation plan to address each risk. Consider using Table 1 as an example.
- Risk: Identify risks that could affect your operations. Common risks include:
- Supplier ABC obsoletes a particular component
- The company email or intranet is disrupted
- An employee with unique skills or knowledge leaves the organization
- Equipment failure of specialized technology
- A key customer moves manufacturing orders to a competitor
- Probability of Occurrence: Consider having five levels of occurrence (90% = very likely, 75% = likely, 50% = possible, 25% = unlikely, 10% = very unlikely).
- Impact of Occurrence: Consider having five levels of impact (5 = severe impact, 4 = high impact, 3 = moderate impact, 2 = limited impact, 1 = insignificant)
- Risk Mitigation Plan: Prepare a specific action plan to prevent or minimize the risk from occurring.
- Recovery Plan: Prepare a recovery plan to remedy adverse outcomes when risk occurs.
- Leadership: Clearly identify responsible individuals within the organization to lead risk mitigation and recovery plans to address a specific risk.
- Reference Documentation: Reference existing procedures, standards, manuals, or other documents that provide supplemental information to help with risk mitigation and/or recovery plans.
Author’s Note: Fundamental concepts and methods illustrated in this column were derived from the following books:
- Business Continuity Management: Global Best Practices, 4th Edition by Andrew N. Hiles and Kristen Noakes-Fry
- The Power of Resilience: How the Best Companies Manage the Unexpected by Yossi Sheffi
- Crisis Management: How to Develop a Powerful Program by Regina Phelps
This column originally appeared in the May 2020 issue of SMT007 Magazine.
More Columns from Operational Excellence
Operational Excellence: Strengthen Your Design Transfer Process With Agile NPIOperational Excellence: Redefine Recruiting to Attract and Hire the Right Talent
Operational Excellence: Process Effectiveness Qualification
Operational Excellence: Working Remotely–Redesign Your Information Systems
Operational Excellence: Sharpening Your Organization’s Competencies
Operational Excellence: Hiring and Retaining Top Employees
Operational Excellence: The Gemba Transformation of Manufacturing With AI
Operational Excellence: Hiring and Retaining Top Employees