-
- News
- Books
Featured Books
- pcb007 Magazine
Latest Issues
Current IssueInventing the Future with SEL
Two years after launching its state-of-the-art PCB facility, SEL shares lessons in vision, execution, and innovation, plus insights from industry icons and technology leaders shaping the future of PCB fabrication.
Sales: From Pitch to PO
From the first cold call to finally receiving that first purchase order, the July PCB007 Magazine breaks down some critical parts of the sales stack. To up your sales game, read on!
The Hole Truth: Via Integrity in an HDI World
From the drilled hole to registration across multiple sequential lamination cycles, to the quality of your copper plating, via reliability in an HDI world is becoming an ever-greater challenge. This month we look at “The Hole Truth,” from creating the “perfect” via to how you can assure via quality and reliability, the first time, every time.
- Articles
- Columns
- Links
- Media kit
||| MENU - pcb007 Magazine
Estimated reading time: 4 minutes
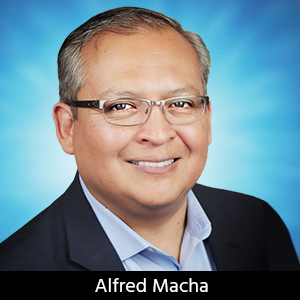
Operational Excellence: Strengthen Your Design Transfer Process With Agile NPI
Finalizing design engineering development is a significant milestone in the product development lifecycle but transitioning the design to manufacturing is the most critical phase of the project. The expectations to meet a compressed product launch schedule puts extreme pressure on the new production introduction process of manufacturers. Projects often fail at this critical juncture.
A recent survey of 120 industry leading manufacturing professionals conducted by Winshuttle [1], a leading software data management provider, found:
- 75% of respondents are under pressure to get products to market faster
- 51% of respondents are still using manual process for their design transfer and new production introduction processes
- 60% of respondents said their launch processes were too slow
- 45% of projects that complete new product introduction end up with cost overruns
This points out that most companies struggle with their NPI processes.
Addressing NPI Shortcomings
First, understand the root cause of why companies struggle with schedule delays and cost overruns. The probable cause will lead to the complexity of NPI processes. The complexity consists of the various reviews, documentation verification, and rigidity of controls put in place with the purpose of achieving a perfect new product introduction transition. However, the disconnect that exists is that the over controls limit the effectiveness of NPI processes—by the nature of NPI—fluidity and flexibility are necessary to optimize the design transfer process to manufacturing via the NPI process.
Understanding the Objectives of NPI
The objective is to have an effective transition from product design to serial manufacturing where product quality consistency is achieved in the manufacturing environment. The traditional approach to accomplish this has been to use a Waterfall development process. The Waterfall model requires design phases to follow a sequential order, where the project development team only moves to the next phase of development or testing if the previous step is completed successfully. The inherent consequence of the waterfall is that it has rigid design gate reviews where there is no room for design optimization and flexibility. The adverse impacts consist of making assumptions that a completed phase design review has satisfactorily met customer expectations where, in reality, the sequential design reviews only confirm that a controlled design review workflow is being followed. At the end of a traditional NPI process, the project documentation will show that a robust workflow was followed during the process—however, there will be minimal interactions with the customer where optimization efforts were not considered during the NPI process. The concept of fluidity and flexibility must be considered as part of the NPI process to achieve customer satisfaction excellence. This can be achieved by applying the concept of Agile methodologies into the NPI process.
The Agile Methodology
Agile methodology is a practice that helps continuous iteration of development and testing in the product development process. In this model, development and testing activities are concurrent, unlike the Waterfall model. This process allows more communication between customers, engineers, managers, and testers. This concept is widely used in software development and has established organizations that have created standards and proven methods for agile development. One of these methods is known as the Agile manifesto [2]. There are 12 key principles that govern agile development:
- Our highest priority is to satisfy the customer through early and continuous delivery of valuable software
- Welcome changing requirements, even late in development. Agile processes harness change for the customer's competitive advantage
- Deliver working software frequently, from a couple of weeks to a couple of months, with a preference to the shorter timescale
- Businesspeople and developers must work together daily throughout the project
- Build projects around motivated individuals. Give them the environment and support they need, and trust them to get the job done
- The most efficient and effective method of conveying information to and within a development team is face-to-face conversation
- Working software is the primary measure of progress
- Agile processes promote sustainable development. The sponsors, developers, and users should be able to maintain a constant pace indefinitely
- Continuous attention to technical excellence and good design enhances agility
- Simplicity—the art of maximizing the amount of work not done—is essential
- The best architectures, requirements, and designs emerge from self-organizing teams
- At regular intervals, the team reflects on how to become more effective, then tunes and adjusts its behavior accordingly
These principles are software development centric, but they can be applied to most new product introduction processes in manufacturing environments.
Creating an Agile Mindset for NPI in a Manufacturing Environment
The biggest challenge non-software companies face in leveraging an Agile mindset in their NPI process is weighing risk with cost.
Because of the high capital cost to launching engineered and manufactured products, it is not feasible to launch Rev A of a product and iterate further on the design over time like it is with Agile software development. These iterations might cause rework in the factory or supply chain that can result in a cost-prohibitive financial situation that no longer supports the original business case. Companies focused on driving top-line business growth through innovation and NPI can benefit greatly when leveraging the positives of Agile principles into their process of building real products.
The easiest area to apply Agile principles to is the concept phase. It is imperative to develop prototypes and proof of concepts that get shared internally and, more importantly, externally with the target consumer. Gaining a full understanding of the end user’s emotional response to a future product is paramount during the design engineering development phase. Also, these agile principles can be continued during the design transfer to manufacturing phase. A practical example is to use 3D print technology to create fixtures, guides, or tooling, which can assist the iterative changes required during the optimization phases of new product introduction.
An Agile NPI Framework
Implementing an Agile NPI process requires a paradigm shift. Below is a practical guide on setting an Agile NPI framework. Click image to download PDF of Table 1.
This column orginally appeared in the February 2021 issue of SMT007 Magazine.
More Columns from Operational Excellence
Operational Excellence: Redefine Recruiting to Attract and Hire the Right TalentOperational Excellence: Process Effectiveness Qualification
Operational Excellence: Working Remotely–Redesign Your Information Systems
Operational Excellence: Sharpening Your Organization’s Competencies
Operational Excellence: Hiring and Retaining Top Employees
Operational Excellence: Update Your Business Contingency Plan
Operational Excellence: The Gemba Transformation of Manufacturing With AI
Operational Excellence: Hiring and Retaining Top Employees