-
- News
- Books
Featured Books
- design007 Magazine
Latest Issues
Current IssueDesigning Through the Noise
Our experts discuss the constantly evolving world of RF design, including the many tradeoffs, material considerations, and design tips and techniques that designers and design engineers need to know to succeed in this high-frequency realm.
Learning to Speak ‘Fab’
Our expert contributors clear up many of the miscommunication problems between PCB designers and their fab and assembly stakeholders. As you will see, a little extra planning early in the design cycle can go a long way toward maintaining open lines of communication with the fab and assembly folks.
Training New Designers
Where will we find the next generation of PCB designers and design engineers? Once we locate them, how will we train and educate them? What will PCB designers of the future need to master to deal with tomorrow’s technology?
- Articles
- Columns
Search Console
- Links
- Media kit
||| MENU - design007 Magazine
Chris Hanson: New Ventec IMS Dielectrics Rated for Higher Temps
July 7, 2020 | Andy Shaughnessy, Design007 MagazineEstimated reading time: 5 minutes
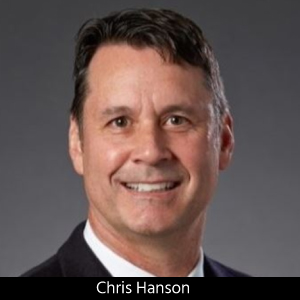
Andy Shaughnessy recently spoke with Chris Hanson, global head of IMS Technology for Ventec International Group.
During their conversation, Chris discusses his group’s recent efforts to create new IMS materials, with a focus on dielectrics. As Chris explains, Ventec has developed several new dielectrics that can withstand much higher operating temperatures, one of which is UL-rated for a maximum operating temp of 155°C, which may be the highest for an IMS dielectric.
Chris also discusses some of the challenges in the IMS segment, including the coefficient of thermal expansion (CTE). The CTE becomes an issue when using materials made of dissimilar metals; because of their different properties, these metals can move at certain temperatures and cause a strain on solder joints. Chris details how Ventec has fielded an IMS material with a lower modulus and an aluminum base plate, which eliminates many of these concerns.
As they wrap up, Andy and Chris look ahead to the post-pandemic future, when technologists once again can travel and meet face to face with customers instead of via videoconferences.
I-Connect007 continues to deliver original reporting and coverage of the electronics design, electronics manufacturing, and contract manufacturing industries, including up-to-date information from the companies, associations, and supply chains globally. Find the latest news and information at I-Connect007.com.
Related Link
- To download this audio (mp3) file, click here.
AUDIO TRANSCRIPT:
Andy Shaughnessy: Hi, I’m Andy Shaughnessy for I-Connect007. Here with me this afternoon is Chris Hanson of Ventec International Group. How are you doing, Chris?
Chris Hanson: I’m doing great, Andy. Thanks for having me.
Shaughnessy: Thanks for being here. Chris is the global head of IMS technology for Ventec. Chris, why don’t you start, just for anyone who’s not familiar, by giving us a quick background about Ventec and some of your responsibilities there.
Hanson: Will do. Ventec has been around since the year 2000. Ventec came into the electronics industry primarily as a supplier of FR-4 type laminates. But since the year 2000, the strategy has always been to develop world-class dielectrics and laminate materials that are specialized. Ventec has several business units. I happen to manage the business unit title IMS. IMS stands for insulated metal substrate. Our division works on dialectics and laminates that are designed to dissipate heat. Ventec has other business units that promote signal integrity for 5G, polyimide-type laminates for medical and military or aerospace applications, and a whole host of other specialty laminates.
Shaughnessy: I understand that you all have been working on some really cool, innovative materials.
Hanson: Absolutely. We have been working on a lot of new IMS-type materials. And when we say we’re working on new materials, the primary focus would be in the selection of the dielectric. The dielectric is the thermally loaded resin that is buried between the copper foil that becomes the circuitry and the base plate, which tends to be, in most cases, aluminum or copper.
But in just the last 12 months, we have developed a couple of new dialectics geared to higher max operating temperatures, meaning as the world moves to silicon carbide and gallium nitride, the push in the power industry is to get to higher MOT-rating products. We have a dielectric that was just released and recognized by UL with a 155°C max operating temp, which, to my knowledge, is the first of its type in our IMS-type industry.
The other product, and the other concern in the electronics industry with these metal-based laminates, is around CTE of the material, or the coefficient of thermal expansion. If you use dissimilar metals to make a laminate, you can, under certain temperature conditions, start to see movement of those metals at different rates and different capacities. That puts a lot of strain on the solder joint of a power component capacitor or LED. We’ve developed a dielectric that we consider to be lower modulus, and it is combined with a very specialty aluminum base plate that really reduces the risk of solder joint fatigue.
Shaughnessy: What are some of the challenges that your customers are coming to you with?
Hanson: In general, the challenges we see today are really a function more based on economic conditions. A lot of these products that we develop are used in automotive applications. And through the virus and other worldwide global situations that we’ve now been exposed to in any of our lifetimes, the challenge is really to help these customers through the slower periods of time. We’ll get there. I’m not concerned about that.
And the Ventec strategy through this entire four or five months of quarantine and lockdown has been to continue forward with product development. We all know that, sooner or later, the economic condition will improve and things will get back to relative normalcy. We are continuing forward with these new products. Thermal improvement is in the industry that I play in with IMS materials, and customers continually are asking, “What is your next best thermal performing dielectric? How do we get more heat out of our components and through your boards?” Our challenge in our R&D labs is to take our current product offering and just make it 10%, 15%, or 20% better, with respect to its ability to dissipate heat.
I have a ton of respect for Ventec, in regard to the amount of time, effort, and money that have been reinvested into new product development. I’ve worked for other customers in similar industries in years past. They came to market with some fabulous products but didn’t keep that momentum going. And companies like Ventec have incredibly gifted R&D folks. It’s imperative for companies and suppliers to stay ahead of the competition. To do that, you have to have great product development.
Shaughnessy: Is there anything else you’d like to add, Chris, that we haven’t covered?
Hanson: The two main products that we’re really promoting right now are the high max operating temp and then the solder joint fatigue dielectric. Other than that, that’s all I have to share today.
Shaughnessy: Hopefully, we’ll see each other at a conference again, when the new normal kicks in.
Hanson: As much as I’ve traveled in my lifetime when business was normal, I might complain on occasion that traveling gets old. But now being quarantined for three months, I seriously have the itch to get out and see some customers and some engineers. Yes, I’d very much like to see and meet up at a conference or future trade show.
Shaughnessy: In the meantime, it’s been good talking to you, Chris. Thanks again for doing this. We appreciate it.
Hanson: Thank you, Andy. Great to talk with you.
Shaughnessy: Again, this has been Andy Shaughnessy for I-Connect007, speaking with Chris Hanson of Ventec International Group. Thanks for listening.
Suggested Items
'Chill Out' with TopLine’s President Martin Hart to Discuss Cold Electronics at SPWG 2025
05/02/2025 | TopLineBraided Solder Columns can withstand the rigors of deep space cold and cryogenic environments, and represent a robust new solution to challenges facing next generation large packages in electronics assembly.
BEST Inc. Reports Record Demand for EZReball BGA Reballing Process
05/01/2025 | BEST Inc.BEST Inc., a leader in electronic component services, is pleased to announce they are experiencing record demand for their EZReball™ BGA reballing process which greatly simplifies the reballing of ball grid array (BGA) and chip scale package (CSP) devices.
Indium Wins EM Asia Innovation Award
05/01/2025 | Indium CorporationIndium Corporation, a leading materials provider for the electronics assembly market, recently earned an Electronics Manufacturing (EM) Asia Innovation Award for its new high-reliability Durafuse® HR alloy for solder paste at Productronica China in Shanghai.
Summit Interconnect Hollister Elevates PCB Prototyping with New TiTAN Direct Imaging System from Technica USA
05/01/2025 | Summit Interconnect, Inc.Summit Interconnect’s Hollister facility has recently enhanced its quick-turn PCB prototyping capabilities by installing the TiTAN PSR-H Direct Imaging (DI) system.
KOKI Expands U.S. Sales Coverage with Multiple New Representatives
04/29/2025 | KOKIKOKI, a global leader in advanced soldering materials and process optimization services, is pleased to announce the expansion of its U.S. sales network with the addition of three new manufacturers’ representative firms: Assembled Product Specialists, Diversitech Reps Inc., and Eagle Electronics.