-
- News
- Books
Featured Books
- pcb007 Magazine
Latest Issues
Current IssueSales: From Pitch to PO
From the first cold call to finally receiving that first purchase order, the July PCB007 Magazine breaks down some critical parts of the sales stack. To up your sales game, read on!
The Hole Truth: Via Integrity in an HDI World
From the drilled hole to registration across multiple sequential lamination cycles, to the quality of your copper plating, via reliability in an HDI world is becoming an ever-greater challenge. This month we look at “The Hole Truth,” from creating the “perfect” via to how you can assure via quality and reliability, the first time, every time.
In Pursuit of Perfection: Defect Reduction
For bare PCB board fabrication, defect reduction is a critical aspect of a company's bottom line profitability. In this issue, we examine how imaging, etching, and plating processes can provide information and insight into reducing defects and increasing yields.
- Articles
- Columns
- Links
- Media kit
||| MENU - pcb007 Magazine
Estimated reading time: 5 minutes
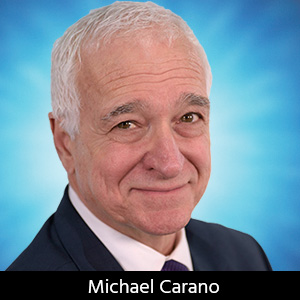
Contact Columnist Form
Trouble in Your Tank: Material Challenges for PCB Fabricators
Laminate materials are the building blocks on which PCBs are manufactured. Circuit board designers rely on the critical electrical properties of the materials to design the interconnect. And with the drive toward the internet of things (IoT), autonomous driving, virtual and augmented reality, material properties take on a very high level of importance.
The crux of the issue is quite simple: Designers are looking for electrical performance, and printed board fabricators are concerned with manufacturability and yields. As the complexity of circuit technology increases (and it is not going to stop anytime soon), there will be a continual pressure to improve yields. However, that is the conundrum, or the “rock and a hard place” cliché.
For the purpose of this discussion, let’s consider the requirements for high-speed data transmission. System designers are looking at several factors, most importantly signal speeds, loss characteristics, and laminate selections.
?Laminate Selection: Dk and Df
The Dk is the property that determines the relative speed that an electrical signal will travel in that material. A low dielectric constant will result in higher signal propagation speed while a high dielectric constant results in lower signal propagation speed (i.e., the lower the Dk, the less impedance there is to the signal propagation). The characteristic impedance of a PCB is determined by the thickness of the laminate and its Dk. Impedance control, and impedance matching of critical linked functional modules, becomes especially important in very high-speed designs (i.e., high-frequency designs). Dk also tends to shift with temperature, so heat generation by such designs is another important factor.
The Df or loss tangent of the material is a measure of the percentage of total transmitted power that will be lost as power dissipated into the laminate material. High-frequency signals switch backward and forward rapidly. There is the switch between positive and negative, causing the molecules within the resin (dielectric) materials to polarize with the electromagnetic field of the signal. During this situation, there is heat loss. Thus, there are signal losses that become greater at higher frequencies. These losses are proportional to frequency and become more pronounced at frequencies higher than 10 GHz. However, today’s technologies are requiring signal speeds in excess of 35 GHz for selected applications. Skin effect is real and must be considered as higher frequencies are used as part of the main-stream circuit designs going forward.
What does all this mean? From a simplicity standpoint, these higher-performance materials are much more difficult to process for the PCB fabricator. Basically, it is not your father’s FR-4 anymore! From a fabrication standpoint, processing a 140°C Tg material through the desmear/etchback process as an example is much easier to etch the resin, remove drill smear, and create sufficient topography to enhance the adhesion of the plated copper. As one moves up the laminate material technology curve (lower Dk, lower Df, engineered materials, including ceramic-filled), resin removal, or simply etching the resin becomes more difficult.
For the fabricator, this necessitates a change in mindset related to chemical desmear. If the end-user requires a significant amount of etch-back, this may not be practical with current mechanical and chemical set-ups. The fabricator must resort to radical departures from the status quo. This includes extended dwell times in the desmear process, increasing the aggressivity of the chemistry and the use of plasma etchback as either a stand-alone or in combination with chemical processing.
Satisfactorily, bareboard fabrication now includes a variety of materials. Glass-reinforced laminate for rigid printed boards—and unreinforced laminates, used primarily for flexible printed boards—present significant challenges for desmear/metalization, as well as in lamination. Further, these higher-performance, thin-core materials are being combined in a variety of applications to achieve a thinner profile of the end-product. Thus, lamination of the combined materials (including adhesives) requires changes in the lamination cycle parameters, including time, pressure, and heat rise rate.
There are several additional material properties that the PCB fabricator must consider to optimize the process: drillability and conductive anode filament (CAF) formation.
Drillability
Drillability is an important consideration in the selection of a laminate for a backplane, particularly with high PTH aspect ratios and the increase in backdrilling. Constant diameter and clean finish are essential. The grade of glass fiber, fillers, and dielectric material hardness all contribute to the hole quality.
Ceramic-filled materials can also introduce extra cost in fabrications. The ceramic can reduce the lifetime of a drill bit from 5000 to 500 hits. There are concerns with hole wall quality as fabricators move up the material technology curve—most notably rough drilled holes along with deep gouges (Figure 1).
Drill quality—or lack thereof, as shown in Figure 1—affects several aspects, including solderability, plating adhesion, and potentially component insertion. Regardless, higher-performance materials are more difficult to drill. Hole wall roughness must be reckoned with.
CAF Formation
CAF is caused by the separation or lack of bonding between the woven glass and the resin material. Essentially, the separation causes a hollow tube, so to speak, that allows moisture to provide sufficient conductivity under bias to form an actual copper filament. This filament can lead to an electrical short.
The hollow fiber shown in Figure 2 is the typical medium leading the conductive filament. The resin can separate from the glass due to the glass-coupling chemistry, resin moisture absorption, drill fractures, or the degree of effectiveness of the prepreg resin coating (no bare fiber ends should be exposed). Then, the pathway provides the ideal situation for the growth of the filament (Figure 3).
Recently, resin suppliers and laminators have made great strides in the understanding of CAF and even better methods to detect the issue. In addition, IPC-4101B helps to address the concerns with resin materials and the propensity to lead to CAF. Most datasheets now state whether materials are CAF-resistant.
Even with the development of CAF-resistant materials, higher-density circuit board designs, higher aspect ratio vias, as well as alternative glass styles, one should not assume that CAF will not occur. Always perform due diligence.
This column originally appeared in the March 2020 issue of PCB007 Magazine.
More Columns from Trouble in Your Tank
Trouble in Your Tank: Can You Drill the Perfect Hole?Trouble in Your Tank: Yield Improvement and Reliability
Trouble in Your Tank: Causes of Plating Voids, Pre-electroless Copper
Trouble in Your Tank: Organic Addition Agents in Electrolytic Copper Plating
Trouble in Your Tank: Interconnect Defect—The Three Degrees of Separation
Trouble in Your Tank: Things You Can Do for Better Wet Process Control
Trouble in Your Tank: Processes to Support IC Substrates and Advanced Packaging, Part 5
Trouble in Your Tank: Materials for PWB Fabrication—Drillability and Metallization