-
- News
- Books
Featured Books
- pcb007 Magazine
Latest Issues
Current IssueSales: From Pitch to PO
From the first cold call to finally receiving that first purchase order, the July PCB007 Magazine breaks down some critical parts of the sales stack. To up your sales game, read on!
The Hole Truth: Via Integrity in an HDI World
From the drilled hole to registration across multiple sequential lamination cycles, to the quality of your copper plating, via reliability in an HDI world is becoming an ever-greater challenge. This month we look at “The Hole Truth,” from creating the “perfect” via to how you can assure via quality and reliability, the first time, every time.
In Pursuit of Perfection: Defect Reduction
For bare PCB board fabrication, defect reduction is a critical aspect of a company's bottom line profitability. In this issue, we examine how imaging, etching, and plating processes can provide information and insight into reducing defects and increasing yields.
- Articles
- Columns
- Links
- Media kit
||| MENU - pcb007 Magazine
Estimated reading time: 3 minutes
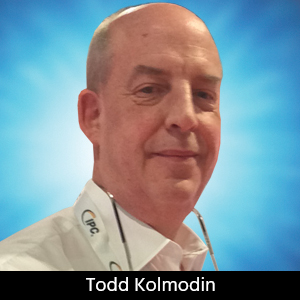
Testing Todd: Waste Not, Want Not
Spring is just around the corner! I’m sure many of us are already pondering our spring-cleaning projects where we will downsize and remove clutter and waste—the unnecessary junk or refuse. But were these things we clean out always junk? Probably not, but they became waste for one reason or another. Maybe those extra 2x4s in your shed or garage were not needed, had you estimated the project correctly, but then you had excess inventory, which led to wasted costs.
Any time we overestimate our projects, we lose costs. For individuals, it may not be as monumental, but for manufacturing, it can be painful. Building extra products exceeding demand is costly in both time and materials, which both affect the bottom line. There are multitudes of knowledge repositories out there covering everything from 5S to Kaizen. All these strive to reduce waste and streamline processes.
Many disciplines believe electrical testing (ET) means only performing electrical test, or, “Is the board electrically correct?” Of course, that is what ET does, but it doesn’t have to stop there. ET failures are faults in the electrical signature of the PCB, but a knowledgeable quality assurance provider can provide valuable feedback on the root causes of the electrical failures. Just like the earlier example about having extra junk in your shed or garage, ET can provide quality feedback to critical processes that may be generating waste.
Once products have reached ET, it is pretty much impossible to correct core issues of the PCB; most times, the PCB is scrapped. That is money down the drain. Unfortunately, in manufacturing arenas where processes are not controlled or monitored, the site compensates and manufactures excess quantities to compensate for scrap or waste. Adding an overage to an order isn’t necessarily a bad thing when compensating for acts of God, system/power failures, and variables such as those. However, when this is done because one is “rolling the dice” for a final yield, it is both reckless and extremely wasteful.
Today, ET can provide valuable feedback to core processes in the PCB. The advancements in 4-wire Kelvin, time-domain reflectometry (TDR), buried passive testing, and hi-pot testing can help isolate key areas where fatal detects can be addressed at their root areas before the point of no return has passed and the PCB continues through later processes, increasing cost when the PCB is already doomed for the scrap bin.
ET cannot be a “black box” in the overall process. Taking bets on whether the order gets through ET is not even what the lines in Las Vegas would take. Driving out waste takes a team approach, and ET can provide invaluable information to areas, such as plating, drill, print and etch, solder mask, all the way back to tooling. This can result in reduced material released for orders and higher first-pass yields, with the final goal being increased revenue to the bottom line.
Don’t bet on the order getting through ET, but rather embrace the feedback, tweak the process, reduce the scrap at the cause, and know the products are heading for ET to get certified and not entered into the certification lottery. Increasing the profitability and driving out waste requires a team approach to encompassing more areas than just the root-cause area.
We all need to check our egos at the door and work the problem. Just because we own a process doesn’t mean it’s perfect. Repetition begets monotony, and sometimes, new input or outside review may identify the new way or solution. Remember, we are all on the same team in the end.
This column originally appeared in the March 2020 issue of PCB007 Magazine.
More Columns from Testing Todd
Testing Todd: Why 4-wire Kelvin?Testing Todd: Why TDR?
Testing Todd: Positivity Boosts Employee Morale
Testing Todd: Preparing Employees for the Long Haul
Testing Todd: Where Can We Improve?
Testing Todd: Turning Into the Wind
Testing Todd: Coming Back to Life—Design Recovery
Testing Todd: Decision Time—Invest or Delegate?