Estimated reading time: 4 minutes
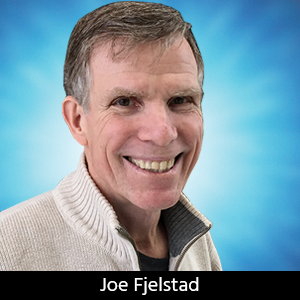
Flexible Thinking: DFM or Design With Manufacturing?
The great Irish author, playwright, and humorist Oscar Wilde once defined a cynic as an individual who knows the price of everything and the value of almost nothing. Unfortunately, over the decades, that same analysis could often be applied to procurement agents in electronic product companies around the globe. The reward for a purchasing agent is too often derived not from getting the best solution for their company but the best price. It is a simple fact that if the cost of a decision is not tracked through the entire manufacturing system, the dollar saved at incoming could cost the company much more at the end through process adjustments, rejects, rework, repair and, much worse, through product failure in the field and returns.
In earlier times, many companies were run by accountants (AKA bean counters) who simply ran the numbers with expectations that profit could be assured by controlling the cost of raw materials in the door. If the sales exceeded the cost of the raw materials, labor, and overhead, there was profit, and everything was good. However, in a globally competitive business environment, one can quickly lose position and market share to those competitors more attentive to inefficiencies in their operations and skilled at “cutting away the fat.” One of the important ways they have accomplished this is by giving manufacturing technicians and engineers a greater voice in manufacturing management. Those closest to the problem are typically those who understand it best. No one truly wants to make inferior products or contribute to waste.
However, manufacturing is limited in terms of what it can do in many situations. Design is the drum major of any manufacturing marching band regardless of the end-product. The decisions made by designers are critical to success. The phrase “garbage in, garbage out” was coined by computer programmers, but it can be applied to design as well. It is simply not possible to make a 3D model of an Escher drawing (though it is entertaining to think about).
Thus, one important prescription for increasing profitability must include the education of designers to the realities of manufacturing, including assembly. In this regard, truly skilled designers are increasingly designing with manufacturing rather than designing for manufacturing (DFM).
In the past, major OEMs were vertically integrated. In such environments, designers typically had a chance to interface internally with manufacturing engineers to check in advance and see if what they wanted to do was possible. On many occasions, what the designer wanted wasn’t really possible at the moment, but by simply asking the question, they caused manufacturing engineers to reconsider the challenge and often alter their thinking as to what was possible. In that regard, the interaction between designer and manufacturing engineer created a springboard for process innovation and improvement. Not every attempt to integrate into a new process was a success, but each one was a learning event. To quote another author and seminal thinker of the last century, T.S. Elliot, “Only those who will risk going too far can possibly find out how far one can go.”
Going too far is not a bad thing. Stretching out our limits is key to making progress. I have been challenging others in the electronics manufacturing industry for over a quarter-century to think in new ways through my various startup activities. In 1990, at Extended Length Flex (ELF) Technologies, we created a roll-to-roll machine and process to direct print catalytic toner on a flexible material web and plate it with copper.
At Tessera in the mid-‘90s, we developed the micro-BGA and fan-out wafer-level packaging concepts; in the process, we helped to usher in CSP technology. At Silicon Pipe in 2001, we re-envisioned electronic interconnection in the 3D dimension with over the top (OTT) interconnection of high-speed signals, novel 3D interconnections, and backplane structures that allowed us to demonstrate 40-Gbps data rates through two copper wires over a distance of a meter through two connectors. That was in October of 2003. All of those concepts have found or are now finding their way into products.
The Occam process, which I rolled out for consideration by the industry in 2007, is still waiting to get some consideration by designers and manufacturers who find themselves stymied by the limitations of current technology that relies on solder to make interconnections between components and circuits. Such an approach could prospectively save a substantial amount of money by reducing both the X-Y dimensions and circuit layer counts of the assemblies while integrating thermal management and increasing reliability. Fortunately, it appears that some fertile ground has finally been found where these ideas may be able to take root in the U.S. and in Europe. I look forward to keeping those with interest informed from time to time through my future shared thoughts and observations.
On a personal closing note, I would like to share an observation a dear and wise friend once shared with me: “One really only needs three things to enjoy a full life: something to do, something to look forward to, and friends.” I am fortunate enough to have many in each category, and the only thing I can add to that list is good health, especially at this moment in history.
Stay safe and stay well!
Editor’s note: Click here to read a related interview titled “Joe Fjelstad Breaks Down His Occam Process.”
This column originally appeared in the April issue of Design007 Magazine in the FLEX007 section.
More Columns from Flexible Thinking
Flexible Thinking: The Key to a Successful Flex Circuit Design TransferFlexible Thinking: Flexible Circuit Technology—Looking Back and Forward
Flexible Thinking: Mind-tapping into January
Flexible Thinking: Another PCB Design Paradigm Shift in the Works
Flexible Thinking: Rules of Thumb—A Word to the Wise
Flexible Thinking: Musings on High Density Interconnections
Flexible Thinking: Integrated Passive Devices—Design Solutions With Many Benefits
Flexible Thinking: Mechatronics in a Flex World