Estimated reading time: 7 minutes
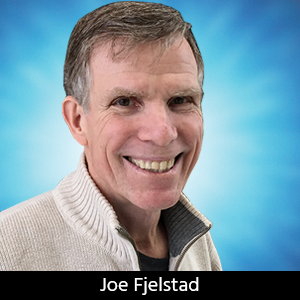
Flexible Thinking: Lead-Free Solder—Panacea or Pandemic?
Solder has been used as the primary means of interconnecting electronic components for more than seven decades. For the first five-plus years of those decades, life was simple, and the solder of choice was fundamentally tin-lead solder in the form of one of two basic alloys: Sn60Pb40 and Sn63Pb37—the latter being the eutectic variant of the timeless and tireless servant of electronics assembly.
Today, however, the number of solder alloy options available to make electronic connections run into the many tens—if not hundreds—of different alloy choices. Read your journals, and you will see that the subject of solder dominates the content in terms of new or recurring problems and their detection, solutions in the form of processes and equipment, and concerns about the reliability of solder joints, which remain the primary root cause of failure of electronics.
For the benefit of all those who are new to the electronics interconnection industry (and there is a constant flow of new people entering the industry), I believe it is worth recalling how we got to this point for your knowledge and edification. This is my opinion, and it is a cautionary tale.
In 2006, the EU legislated a ban on lead in electronic solders. This was covered under the moniker of Restriction of Hazardous Substances (RoHS), which restricts the use of a number of naturally occurring elements that can be toxic under certain circumstances, along with some man-made organic compounds commonly used as flame retardants, which have been shown to have possible links to cancer.
RoHS was conceived as a prospective means of protecting both the environment and the health of Europe’s citizenry (and presumably those of others around the world). However, most high-profile targets of the effort and promotion were executed out under the banner of “lead-free.” This was arguably done because lead has long been identified as the potentially poisonous element that harms the health and development of children, mostly from ingestion of paint chips tinted with lead pigments, which are sweet to the taste. (The Romans used to store wine in lead vessels to increase its sweetness as lead is quite soluble in vinegar, and the common name for lead acetate formed in the process was “lead sugar.”)
While lead in paint and gasoline were definitely vectors for ingestion and poisoning, there was little to no evidence to show any risk of lead in electronics solder making its way to children (or adults, for that matter). The exception was found in the injury of those unfortunate individuals in Asia and South Asia who were tasked to recycle electronics without being given any education, training, tools, or protective gear to carry out those tasks. It was both calculated, callous, and inhumane, but it was also highly profitable to those in charge.
It was an opening for lead-free, and since that time, lead-free has, in general, been a moneymaking machine that continues to crank out profits because it is a mandate that will never have a single solution. There are too many variables to control, and too many chasing the “perfect” solution. I have some dear and highly respected friends and colleagues in this industry who have—year after year—tried to solve the problem, but like those who play the fun but insidious game “whack-a-mole,” it is unlikely they will ever win because one never knows when the next best thing will be found that will make everything perfect at last. It has not happened yet. Instead, the horizon has just gotten more cluttered with prospective solutions.
With that said, and again for the benefit of the newcomers to the electronics interconnection industry, the recounting of some of the important reasons why lead-free should never have been adopted are hereafter provided so that those newcomers might have these reasons to ponder and reflect upon as they themselves step up with mallet in hand to give the game of “whack-a-mole” their best shot. I suspect when one considers these reasons, one might as well ask themselves, “Is lead-free solder really a panacea, or is it a pandemic?
Reason 1
At the time of the ban, lead in electronic solders accounted for approximately 0.5% of all lead used globally. To target such a small quantity with such sweeping and overwhelming legislative force was the equivalent of using a shotgun to exterminate a mosquito.
Reason 2
Lead in electronic solder has never been proven to cause a single individual any harm from normal use and standard and reasonable sanitary practices. (If any reader has data to the contrary, please do not hesitate to share it with me so I can be corrected.)
Reason 3
Legacy lead from electronic solders that has ended up in landfills has not been shown to leach into groundwater. Even with years of such legacy lead from many other sources, such as batteries and painted structures, studies done at the time showed that all but a few landfills around the nation had significant quantities of lead leaching, and these were in landfills which took in significant waste from nearby high lead use industries[1].
Reason 4
Most lead-free solders contain substantial percentages of silver (~3–4%), and silver is toxic to microbial life and fish larva. This has often been ignored perhaps because it was felt that it would be recaptured and recycled.
Reason 5
The global conversion cost to lead-free ran to perhaps $100 billion or more with no real benefit[2]. The conversion cost continues to this day.
Reason 6
Lead-free solders typically require significantly higher temperatures to solder, meaning that more energy is required and will be required on an ongoing basis. The higher temperatures required also negatively impact and influence the PCB material choice, as well as PCB and semiconductor devices and other component reliability.
Reason 7
The definitive reliability of lead-free solders remains elusive to this day. Alloy after alloy is trotted out to run the assembly gauntlet with varying degrees of success and it remains an uncertainty how well they will perform over time, as there are numerous effects (cracking, voiding, tin whiskers [3], etc.)—all of which have causes that remain, in many cases, and are neither well understood nor predictable.
Reason 8
Several early studies from both universities[4] and the U.S. EPA[5] (and which were largely ignored) indicated at the time that, on-the-whole, lead-free electronics appeared to be much less environmentally friendly than those using tin-lead solder. Again, the primary case against lead was its toxicity, which for lead—as metal or in an alloy—was and remains unlikely to cause harm unless directly ingested. (Most common lead salts, hydroxides, chlorides, and sulfates are insoluble in water and many acids.)
Reason 9
Traditional tin-lead solders continue to be used by military and aerospace manufacturers that are exempt because they must have the highest levels of reliability, resulting in a dual path that has created an ongoing logistical headache; this is becoming ever more challenging as sources of tin-lead finished components continue to dry up.
Reason 10
Interconnection innovation remains hobbled as engineers are diverted from solving real technological problems to solving a “lead problem” that never existed in the opinion of most scientists.
Reason 11
Tin resources have always been significantly lower than those of lead; as a result, new tin mines were opened often in areas where rival factions fight to the death for control of the mines. It is also highly unfortunate that some of the richest tin mines are found in rain forests, which must be clear-cut to get to the tin deposits, contributing to global warming[6].
Reason 12
The provisions of the Waste Electrical and Electronic Equipment (WEEE) regulations mandate the recycling of electronic products, making all the concerns of lead in electronics completely moot.
Conclusion
As the timeless adage goes, “The road to hell is paved with good intentions.” If you can feel the heat as you are trying to make your products better and more reliable, you may well get the impression you have already arrived there. Then again, as Winston Churchill sagely said, “When you are going through hell, keep going.”
Keep up your spirits, and stay well.
Editor’s Note: Read the Solderless Assembly for Electronics: The SAFE Approach e-book written by Joe Fjelstad to consider an alternative approach to manufacturing electronics without solder. Visit I-007eBooks.com to download this and other free, educational titles.
Joe Fjelstad is founder and CEO of Verdant Electronics and an international authority and innovator in the field of electronic interconnection and packaging technologies with more than 185 patents issued or pending.
References
- G.C. Munie, L. Turbini, D. Berneir, J. Gamalski, & D.W. Bergman, "Examining the Environmental Impact of Lead-Free Soldering Alternatives,” Proceedings of IEEE International Symposium on Electronics and the Environment, San Francisco, California, May 2000.
- H. Miller, “Lead-free Electronic Solder, Why?” InfraFOCUS, 2002.
- nepp.nasa.gov/WHISKER
- L. Turbini, “The Real Environmental Cost of Lead-Free Soldering,” Solid State Times, Volume 4, Issue 3, July 2002.
- “Solders in Electronics: A Life-Cycle Assessment,” U.S. Environmental Protection Agency August 2005.
- K. Hodal, “Death Metal: Tin Mining in Indonesia,” The Guardian, November 23, 2012.
More Columns from Flexible Thinking
Flexible Thinking: The Key to a Successful Flex Circuit Design TransferFlexible Thinking: Flexible Circuit Technology—Looking Back and Forward
Flexible Thinking: Mind-tapping into January
Flexible Thinking: Another PCB Design Paradigm Shift in the Works
Flexible Thinking: Rules of Thumb—A Word to the Wise
Flexible Thinking: Musings on High Density Interconnections
Flexible Thinking: Integrated Passive Devices—Design Solutions With Many Benefits
Flexible Thinking: Mechatronics in a Flex World