-
- News
- Books
Featured Books
- pcb007 Magazine
Latest Issues
Current IssueSales: From Pitch to PO
From the first cold call to finally receiving that first purchase order, the July PCB007 Magazine breaks down some critical parts of the sales stack. To up your sales game, read on!
The Hole Truth: Via Integrity in an HDI World
From the drilled hole to registration across multiple sequential lamination cycles, to the quality of your copper plating, via reliability in an HDI world is becoming an ever-greater challenge. This month we look at “The Hole Truth,” from creating the “perfect” via to how you can assure via quality and reliability, the first time, every time.
In Pursuit of Perfection: Defect Reduction
For bare PCB board fabrication, defect reduction is a critical aspect of a company's bottom line profitability. In this issue, we examine how imaging, etching, and plating processes can provide information and insight into reducing defects and increasing yields.
- Articles
- Columns
- Links
- Media kit
||| MENU - pcb007 Magazine
Estimated reading time: 7 minutes
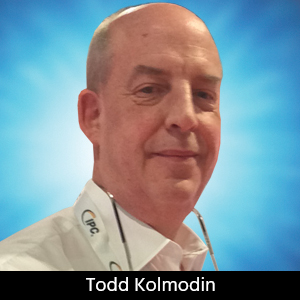
Testing Todd: Staying in Your Lane
Happy holidays! As 2019 comes to a close, I thought I would take a moment and talk about the importance of standardization. When we talk about the standardization of processes, it doesn’t necessarily mean that you have to do something the same as the people next door. Sure, there may be some industry guidelines that we all must follow, but there still is a great deal of latitude that allows us to perfect our way of doing things.
Some people may rise in the morning and put their right sock on first, while others may begin with the left. Is that a problem? No, the end result is the same—socks on! It doesn’t have to be any different in larger-scale processes. Standardization comes down to an agreement that we are to perform a task or set of tasks the same way every time. Putting your engineering hat on, this provides predictability. If we all agree on how the task(s) should be performed, we can predict the outcome with a high degree of accuracy.
Now, to begin with, the word “standardization” strikes fear into the hearts and minds of many who think about rules, regulations, problems. Not true! All that it means is that we review a task or set of tasks that we routinely perform and roadmap it. How we perform the task, and which steps are involved and in what order, results in the standardization of that task or process. Standardizing a process is nothing more than mapping the steps involved and repeating them each time to achieve the predicted result. Unfortunately, this is where many attempts at standardization fail.
I’ve written many processes and standardized numerous activities in the workplace over the years, and I have found areas of concern that usually result in a process failure or standardization breakdown.
Let’s explore some simple steps in building a process and standardizing it. Here are my 10 steps to building a process and standardizing:
1. Identify the task that requires standardization or process creation.
2. Map the process from a high altitude (i.e., block diagram, flow chart).
3. Zoom in to the individual blocks and expand into macro steps.
4. Zoom in again and expand into micro-steps.
5. Rebuild the pyramid from micro-steps back to the master flow chart.
6. Test your process.
7. Review the continuity of the process.
8. Edit/revise.
9. Retest your process.
10. Release and standardize.
Let’s break down these steps even more so that I don’t leave you all in a December Nor’Easta.
In step 1, we want to identify what we are trying to accomplish. This may sound easy, but it may be the most difficult task of all. This is where many failures occur and can result in wasted labor, increased cost, and reduced productivity. For those of you involved in the world of ISO, this is an area where the term “risk analysis” becomes very apparent.
Step 1 identifies a candidate for a process build or standardization. However, just because it has been identified does not necessarily mean it should be committed. What is the benefit of creating the process or standardization? What is the risk of not committing to building or standardizing this process or task? Some ideas to think about here are whether the task is mission critical or is it a menial task that has no significant impact on the overall end result. Performing a solid analysis here can save time and money in the long run but combatting “over-standardization,” or as I put it, “painting oneself into a corner.”
In step 2, we have decided that we need to proceed and build this process or standardization. A big mistake here is that many try to throw something together; “Write down how you do that task and bring it back.” Sound familiar? Send two people out on that same task, and I guarantee you that you will have two different versions of that same task from each of them. What needs to be done here is a map of the task, including where it starts and what we want the end result to be. Depending on the process, this can be a rather simple map, or with more complex operations, it could look like the Dallas 635 freeway at 5 p.m. Make general diagrams or flow steps. I use the term “high altitude” here, as we want a global view of the process requiring standardization.
Step 3 takes us down to a low altitude and breaks down the blocks. In a simple process, this may not require too much effort. In larger tasks, this is where a team approach works very well. Instead of just one person writing steps how they perform them, there is a collective approach to the task which optimizes it for the best flow. This is where we identify sub-processes that may affect the success of this step. This lower altitude pass is a necessary step to prevent missed opportunities for success.
In step 4, we are now on the ground or in the trench. We expand the tasks within our blocks and really turn the wrenches. This is the fine print of the task down to dial settings, colors to use, where to place what, use what tools, etc. Don’t forget safety concerns, as well. We don’t need an unexpected OSHA visit!
We start building our pyramid in step 5. We combine steps 4 through in reverse order to bring our process or standard to maturity. Work instruction notes from the micro and macro levels are combined to validate the process map. This is where we find whether we are in our lane or experiencing a train wreck.
In step 6, we have a written process or standardization candidate. Again, this is another area where failure can occur. If the process or standard is released at this point, you may find that the result may not even be close to what you outlined in step 1. Unfortunately, for many, this is the case and can lead to unpredictable results, loss of time or materials, and ultimately, failure. The process needs to be tested. This should not be done by any person writing the micro and macro levels of the process or standard. This should be an independent third party. This provides an unbiased view of the task and will quickly identify inconsistencies. The result of this step is really a “go or no go” on whether the process or standardization is functional.
With step 7, we want to know the continuity of the process or standardization with respect to ergonomics, movements, tool accessibility, repetition, lighting, etc. If the steps of the task are correct from the testing done in step 6, are they being done efficiently? Just having the steps for repeatability doesn’t mean it is efficient. Here is where efficiency is taken into consideration and applied.
In step 8, we review the actions of steps 6 and 7. Adjustments are made to correct inconsistent results and to improve efficiency. I cannot state enough how important steps 6 and 7 are when building a process or standardizing. Omitting those steps and going right to a mature process is almost a guaranteed failure.
After the corrections and optimizations are done in step 8, we move to step 9: test it again. This time, use another third party candidate to perform the tasks. Use a fresh pair of eyes and abilities to perform the tasks. We may identify yet another anomaly that was not detected previously. This also adds to the continuity of the process or standard. We want it capable of being performed by anyone qualified to perform the task or set of tasks outlined with the same predicted results.
Step 10 is the home stretch. We have a final working process or standard. It’s ready for release, right? Not so fast. Here is another pitfall that many fall into; release the document, post it to the databases for online reference, and it’s done. Here, we must remember that we need to educate those who are in this department, area, or team that will be responsible for the results. That means training and review of the process or standard. We can write standards all day long, but if our teams are not educated or aware of the standard, how can we hold them to it?
Conclusion
Hopefully, I’ve given you some solid building blocks for creating your processes or standards within your circle of the world. Of course, there are other guidelines and building techniques out there, but I’ve found a very high degree of success with the tools I’ve outlined above. In my time doing process audits and standard reviews, there is an overall design which can be characterized by “staying in your lane.” We’ve all seen it; we may all be driving in the same direction to the same destination, but there is always that “one guy” who is drifting over the lines, looking at his cellphone, eating a burger, or who knows what. Sure, he is probably going to get there, but with reduced efficiency, more steps and unnecessary corrections (and maybe a ticket too!).
Thanks for reading this year. I appreciate your readership! I hope you all have a great holiday season as we look forward to a prosperous 2020.
This column originally appeared in the December 2019 issue of PCB007 Magazine.
More Columns from Testing Todd
Testing Todd: Why 4-wire Kelvin?Testing Todd: Why TDR?
Testing Todd: Positivity Boosts Employee Morale
Testing Todd: Preparing Employees for the Long Haul
Testing Todd: Where Can We Improve?
Testing Todd: Turning Into the Wind
Testing Todd: Coming Back to Life—Design Recovery
Testing Todd: Decision Time—Invest or Delegate?