I-Connect007’s Latest Innovation: Joe Fjelstad’s E-Workshop on Flexible Circuits
September 9, 2020 | Pete Starkey, I-Connect007Estimated reading time: 5 minutes
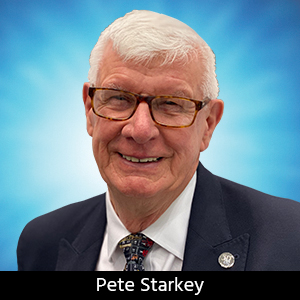
“Combining necessity with ingenuity stimulates originality in technical education!”
Denied the prospect of physically attending conferences, symposia, or live workshops by travel and social-distancing restrictions, I welcomed the opportunity to enjoy a privileged preview of I-Connect007’s latest innovation in technical webinars: a series of e-workshops covering structures, applications, materials, and manufacturing processes in flexible circuit technology with the industry’s leading authority—Joe Fjelstad.
All nine sessions will be accessible through straightforward registration upon release, each covering a specific aspect of flexible circuit technology. This video series is a commendable companion to Fjelstad’s book Flexible Circuit Technology, originally published in 1994 and now in its fourth edition. The definitive work of reference—and a must-have resource for designers, manufacturers, and users of flexible circuits—is a substantial volume of over 600 pages available for free download.
What was my experience? The configuration of the webinar user-interface was functional and uncluttered, and I found it pleasingly uncomplicated to operate. Video of Fjelstad’s presentation in one corner was synchronised with comprehensive notes and relevant illustrations on the main screen. It was easy to start, pause, and replay with a link for submitting questions.
In his introduction, Fjelstad commented that although some of the material was not new, it remained relevant because the basic principles of flexible circuit technology had changed little over its history and—for practical purposes—was representative of current and fundamental practices. Clearly, there had been some significant advances that were important to include. His series of individual presentations would offer a comprehensive awareness of flexible circuit technology, and he welcomed questions and feedback.
Fjelstad’s first workshop session was an intense 25-minute history of flexible printed circuits and a description of basic flex structures. He began by stressing that electronic interconnections were fundamental to the future with electronic devices playing an ever-expanding role in society. The integration of more functionality into less material and less space was a key objective both ecologically and technologically for electronic products. And flexible circuits were important enablers.
Many different types of construction were encompassed by the phrase “flexible circuit.” The fundamental definition of a flexible circuit according to IPC-T-50 was “a patterned arrangement of printed wiring utilising a flexible base material with or without flexible cover layers,” although that definition did not give a full appreciation of all the various structures. Flexible circuits could be further defined in terms of their applications: static flex designed to be bent to fit into an installation, dynamic flex designed to be flexed continuously or intermittently over the life of the product, IC packaging flex, and stretchable circuits designed to be resiliently stretched to conform to shapes.
Flexible circuits were originally designed as three-dimensional interconnection alternatives to wire harnesses, offering weight saving, assembly advantages, and freedom from wiring errors. They were adopted in military and aerospace applications—followed by the automotive industry and all types of consumer electronics, as well as telecom, computer, medical and IC packaging—and the evolution continued.
The ancestor of all flexible circuits was patented in 1903 by Albert Hanson, using flattened conductors on insulated coated papers. Soon afterward, Thomas Edison had the idea of forming a pattern of adhesive on linen paper and coating it with carbon dust. In the early 1940s, there was development work in Germany on flattened wire conductors in a polymer material for military purposes, and the technology later found its way to the U.S.
In 1956, Sanders and Photocircuits etched copper patterns on a flexible base film, and in 1959, Lockheed used flexible circuits in satellites and automobiles. Around 1965, John Marley at ITT used flex circuits in IC packaging, and in 1966, Sanders patented the first rigid-flex circuit. By 1974, IBM used flexible circuits in disk drive applications. Around 1975, Rogers Corporation transferred some flexible circuit technology to manufacturers in Japan, and Japanese engineers made enormous progress in developing dense consumer electronics at a lower cost.
Describing some basic flexible circuit constructions, Fjelstad listed single-sided flex, back-bared flex—allowing access to two sides of a single metal layer—two-metal-layer flex, multilayer flex, rigid-flex, and sculptured flex. He also touched briefly on stretchable circuits and gave examples and typical applications of each type. Fjelstad further stressed the importance of the designer spending time with the fabricator, particularly in the case of complex multilayer builds, which could appear deceptively simple but were highly engineered.
Polymer thick film offered some scope in flexible circuit technology, especially with the trend toward printed electronics. Multiple-shot injection moulding of catalytic and non-catalytic insulating materials offered a potentially clever approach to design, but tooling was expensive. Flexible circuit techniques had been adapted to provide more cost-effective solutions.
Summarising this session, Fjelstad commented that he had tried to show that flexible circuits had a very long and interesting history. “Sometimes, history gets forgotten, but some of those technologies are still in use today.” He demonstrated that flexible circuits could vary significantly in their construction and that they would continue to offer many useful types of interconnection possibilities, with many more on the horizon.
In the next workshop session, he talks about flexible circuit applications, some of the technology drivers that would make one want to use flexible circuits, and how to use them successfully.
I also took a sneak peek at the technology and application drivers session to hear Fjelstad discussing package size reduction, weight reduction, assembly efficiency improvement, assembly cost reduction, assembly yield improvement, and reliability enhancement as potential benefits of flexible circuits. He explained that they also offered better electrical properties, improved heat dissipation capability, three-dimensional packaging capability, simplified inspection, and improved product appearance. Showing examples in automotive applications, computers and peripherals, industrial controls, medical electronics, IC packaging, and photovoltaics, Fjelstad demonstrated how flexible concepts could stimulate alternative approaches to circuit design.
Successive workshop topics included flexible circuit materials, implementing flexible circuit technology into products, design principles and practices, enhancing flex circuit robustness, design guidelines for bending, folding and dynamic movement, manufacturing processes including roll-to-roll processing and printed electronics, singulation methods, assembly aids, solderless constructions, connector options, and assembly standards. An encyclopaedic series!
To steal a quote from the foreword to Fjestad’s book, “It’s what you learn after you know it all that counts.”
You can get full access to the entire series now by registering here. Sponsored by American Standard Circuits, a proud supporter of online education.
Further Reading
- Joe Fjelstad, Flexible Circuit Technology: 4th Edition, I-Connect007, November 2011.
- Barry Matties, “Joe Fjelstad Updates His Online Flex Workshop,” Design007 Magazine, July 2020.
- Joe Fjelstad, “Flexible Thinking” columns, I-Connect007.
- Register to download and read Design007 Magazine, including the Flex007 section.
Testimonial
"In a year when every marketing dollar mattered, I chose to keep I-Connect007 in our 2025 plan. Their commitment to high-quality, insightful content aligns with Koh Young’s values and helps readers navigate a changing industry. "
Brent Fischthal - Koh YoungSuggested Items
50% Copper Tariffs, 100% Chip Uncertainty, and a Truce
08/19/2025 | Andy Shaughnessy, I-Connect007If you’re like me, tariffs were not on your radar screen until a few months ago, but now political rhetoric has turned to presidential action. Tariffs are front-page news with major developments coming directly from the Oval Office. These are not typical times. President Donald Trump campaigned on tariff reform, and he’s now busy revamping America’s tariff policy.
Global PCB Connections: Understanding the General Fabrication Process—A Designer’s Hidden Advantage
08/14/2025 | Markus Voeltz -- Column: Global PCB ConnectionsDesigners don’t need to become fabricators, but understanding the basics of PCB fabrication can save you time, money, and frustration. The more you understand what’s happening on the shop floor, the better you’ll be able to prevent downstream issues. As you move into more advanced designs like HDI, flex circuits, stacked vias, and embedded components, this foundational knowledge becomes even more critical. Remember: the fabricator is your partner.
MKS’ Atotech to Participate in IPCA Electronics Expo 2025
08/11/2025 | AtotechMKS Inc., a global provider of enabling technologies that transform our world, announced that its strategic brands ESI® (laser systems) and Atotech® (process chemicals, equipment, software, and services) will showcase their latest range of leading manufacturing solutions for printed circuit board (PCB) and package substrate manufacturing at the upcoming 17th IPCA Show to be held at Pragati Maidan, New Delhi from August 21-23, 2025.
MKS Showcases Next-generation PCB Manufacturing Solutions at the Thailand Electronics Circuit Asia 2025
08/06/2025 | MKS Instruments, Inc.MKS Inc, a global provider of enabling technologies that transform our world, today announced its participation in Thailand Electronics Circuit Asia 2025 (THECA 2025), taking place August 20–22 at BITEC in Bangkok.
Point2 Technology, Foxconn Interconnect Technology Partner to Revolutionize AI Cluster Scalability with Terabit-Speed Interconnect
08/06/2025 | BUSINESS WIREPoint2 Technology, a leading provider of ultra-low-power, low-latency mixed-signal SoC solutions for multi-terabit interconnect, and Foxconn Interconnect Technology (FIT), a global leader in precision interconnect solutions, have signed a Memorandum of Understanding (MOU) to accelerate the commercialization of next-generation Active RF Cable (ARC) and Near Pluggable e-Tube (NPE) solutions.