-
- News
- Books
Featured Books
- pcb007 Magazine
Latest Issues
Current IssueIn Pursuit of Perfection: Defect Reduction
For bare PCB board fabrication, defect reduction is a critical aspect of a company's bottom line profitability. In this issue, we examine how imaging, etching, and plating processes can provide information and insight into reducing defects and increasing yields.
Voices of the Industry
We take the pulse of the PCB industry by sharing insights from leading fabricators and suppliers in this month's issue. We've gathered their thoughts on the new U.S. administration, spending, the war in Ukraine, and their most pressing needs. It’s an eye-opening and enlightening look behind the curtain.
The Essential Guide to Surface Finishes
We go back to basics this month with a recount of a little history, and look forward to addressing the many challenges that high density, high frequency, adhesion, SI, and corrosion concerns for harsh environments bring to the fore. We compare and contrast surface finishes by type and application, take a hard look at the many iterations of gold plating, and address palladium as a surface finish.
- Articles
- Columns
Search Console
- Links
- Media kit
||| MENU - pcb007 Magazine
Estimated reading time: 5 minutes
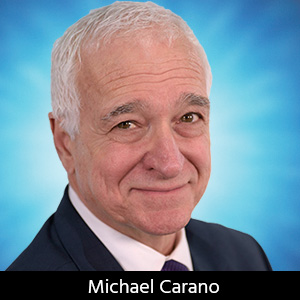
Contact Columnist Form
Trouble in Your Tank: A Process Engineer’s Guide to Advanced Troubleshooting, Part 1
The Case of Failed Boards at Assembly
Defects may “manifest” or be detected in or after a specific operation within the PCB manufacturing process, but the underlying root cause may have occurred earlier (perhaps much earlier) in the process. As has been written in many of my columns published thus far, I chose to present the anomaly or defect where it is most likely to be detected and subsequently present the most likely root causes wherever they might have been introduced. It should be noted that these examples are presented as likely starting places for the investigation of anomalies or defects presented or the kinds of causes that might be investigated.
The process engineer’s task (aka “the troubleshooter”) is complicated by the fact that there are many possible ways to combine or sequence the individual process steps available to achieve the desired end structure. As an example, a “simple” single-lamination multilayer printed wiring board may involve 30–50 process steps, while a complex, multiple lamination (“sequential lamination”) printed wiring board, with pre- and post-machining and other mechanical operations and selective plating processes, could involve several hundred process steps.
In an ideal world, each step could be verified to be correct immediately during or after the process, but in practice, the effect of many processes cannot be readily evaluated until the completion of many subsequent steps makes latent errors visible. Much effort is expended and has been expended in attempts to improve this with limited success. Thus, it remains a troublesome issue.
Process Control
Before presenting the main subject of this month’s feature, a word with respect to process control is in order. What gets measured gets managed. Simply put, one needs to understand that processes by themselves (excuse the non-technical term) have hiccups. Even when employing in-tank sensors and controllers to monitor chemistry, it is strongly suggested that wet titrations be employed to verify that chemical parameters are in check. While wet analysis involving titrations may be time-consuming, a skilled operator will get accurate results. More on specific aspects of process control in a future column.
In this issue of “Trouble in Your Tank,” the focus will be on several anomalies that may have their origins in process steps not normally recognized as the root cause of the issue.
Assembly-Related Defects
It happens. You receive the dreaded phone call from one of your assembly customers. Some of the boards (very expensive ones!) that your company built failed during assembly. There were some vias with poor solder flow-up and a few vias with blowholes in the solder fillet. Obviously, the assembly company is placing the blame squarely on you (Figures 1 and 2).
In Figure 2, there are concerns with solderability as well. For reference, the final (solderable finish) on these boards is organic solderability preservative (OSP). Note the lack of solder fill or flow-up. OSP was also the finish of choice on the other part numbers that did not fail.
In Figure 2, the through-hole component lead wetted well. It would be difficult to assign cause to poor component lead wettability. Figure 3 shows another view of the issue.
Some additional background here for the troubleshooter: As part of this story, this group of boards flagged by the assembly company was processed through metallization and electroplating on the same day. And all the boards in question were of the same part number. Two other part numbers manufactured for the same assembly company processed without issue. Adding further mystery to the problem was the fact the boards passed electrical test before shipping to the assembler.
Working Backward to Get to the Root Cause
At first glance, you will see that in Figure 1, the electrolytic copper looks very thin yet continuous. However, the blowhole or outgas is quite evident, leaving a void in the solder fillet. Upon re-examination of the coupons associated with this job, some sections did show the copper plating thickness at 0.5 mils (12 microns), which was obviously thinner than the specification. Could this have been a contributing factor? The answer is yes, clearly. In simple terms, the thinner copper did not provide sufficient strength to prevent the possible rupture of the copper during assembly. It is also possible that there was a micro-void that went undetected. Regardless, it resulted in a combination of rough holes due to poor drilling (excessive in-feed rates, slow up-feeds, incomplete cure of the laminate material).
What went wrong in the electrolytic copper plating operation, at least for this part number? Electroplating follows the rule of Faraday’s Law of Electrolysis[1]. Simply put, when electroplating any metal from a solution of its electrolyte (in this case, copper ions +2 valence in a water/acid solution), it takes so much current flowing per unit of time to reach the required plating thickness. This assumes excellent plating distribution and high efficiency. In the real world, there will be deviations that do not allow for the perfect distribution and uniform plating thickness across the circuit board.
Process engineers must use the tools available to optimize the plating distribution as much as possible. However, in this case, the tools were not used properly. As Figure 2 shows, plating is also related to the thin amount of copper at the knee of the hole. When thin plating over the knee (often referred to as dishing) is encountered, the most likely causes are excessive solution agitation, organic contamination in the copper plating electrolyte, or additional agent imbalance. Agitation is easily adjusted. Organic build-up must be rectified through solution purification.
A final word on this defect analysis: There were clear issues that caused the plated copper to be below specification. On the day in question, there were several electrical issues, including lower direct current to be applied to the plating cell lead in part to lower plating thickness in the hole (Faraday’s law). In addition, the fabricator should look into improved drilling, more uniform solution agitation (less turbulence), and adjustment of the organic additives in the plating electrolyte.
Click here for Part 2 of this column.
Reference
1. Wikipedia, “Faraday’s laws of electrolysis.”
This column originally appeared in the June 2020 issue of PCB007 Magazine.
More Columns from Trouble in Your Tank
Trouble in Your Tank: Yield Improvement and ReliabilityTrouble in Your Tank: Causes of Plating Voids, Pre-electroless Copper
Trouble in Your Tank: Organic Addition Agents in Electrolytic Copper Plating
Trouble in Your Tank: Interconnect Defect—The Three Degrees of Separation
Trouble in Your Tank: Things You Can Do for Better Wet Process Control
Trouble in Your Tank: Processes to Support IC Substrates and Advanced Packaging, Part 5
Trouble in Your Tank: Materials for PWB Fabrication—Drillability and Metallization
Trouble in Your Tank: Supporting IC Substrates and Advanced Packaging, Part 5