-
- News
- Books
Featured Books
- pcb007 Magazine
Latest Issues
Current IssueIn Pursuit of Perfection: Defect Reduction
For bare PCB board fabrication, defect reduction is a critical aspect of a company's bottom line profitability. In this issue, we examine how imaging, etching, and plating processes can provide information and insight into reducing defects and increasing yields.
Voices of the Industry
We take the pulse of the PCB industry by sharing insights from leading fabricators and suppliers in this month's issue. We've gathered their thoughts on the new U.S. administration, spending, the war in Ukraine, and their most pressing needs. It’s an eye-opening and enlightening look behind the curtain.
The Essential Guide to Surface Finishes
We go back to basics this month with a recount of a little history, and look forward to addressing the many challenges that high density, high frequency, adhesion, SI, and corrosion concerns for harsh environments bring to the fore. We compare and contrast surface finishes by type and application, take a hard look at the many iterations of gold plating, and address palladium as a surface finish.
- Articles
- Columns
Search Console
- Links
- Media kit
||| MENU - pcb007 Magazine
Estimated reading time: 6 minutes
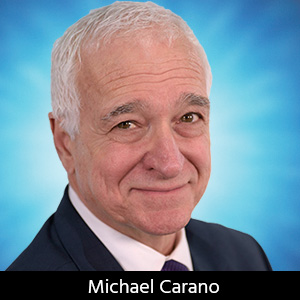
Contact Columnist Form
Trouble in Your Tank: CAF Formation—Correction of Misrepresentation of Origins and Causes
Dear readers,
In my April 2020 column in PCB007 Magazine, I incorrectly misrepresented the origins and causes of conductive anode filament (CAF) formation. This follow-up column will provide more insight and depth of knowledge on the CAF failure mode.
In that column, I incorrectly stated that CAF is caused by the separation or lack of bonding between the woven glass and the resin material. Essentially, the separation causes a hollow tube, so to speak, that allows moisture to provide sufficient conductivity under bias to form an actual copper filament. This filament can lead to an electrical short.
In that column, I did not mention that a hollow fiber was not related to CAF growth and has no relationship to the polymer/glass bond. Further, as shown later, I did not specifically state that the CAF failure growth must be from the anode toward the cathode to be called CAF. The key requirements for CAF growth are a path and temperature, humidity, and bias (THB) conditions. If these ingredients are not present, then CAF cannot occur.
For example, if a hollow fiber is present and aligned to the plated through-hole (PTH) wall, during the plating process, the hollow fiber will be filled with copper and plating salts, which—when exposed to temperature and humidity conditions—will become conductive and result in current leakage. This is not CAF since no bias was present to drive the CAF growth electrochemically.
Lastly, I did not distinguish the difference between wicking and CAF growth, so I would like to make it clear that the CAF failure mode is not the same as wicking. Thus, to avoid any confusion, I would like to keep these two items as separate topics.
There have been many extensive research and publications on CAF. This column will be based on several scholarly research papers to provide a much better understanding of the CAF failure mode. I would like to personally thank Dr. Antonio Caputo for his advice and counsel on this subject matter. He has performed significant work related to CAF, and I have captured his comments here.
It was pointed out to me that CAF is a special type of electrochemical migration (ECM) failure mode that occurs in PWBs. The CAF failure mode was first discovered in parallel by Bell Labs researchers [1] and Raytheon [2] in 1976, and later named conductive anodic filament by Lando et al. in 1979 [3].
Under temperature-humidity-bias (THB) conditions, CAF, which has been identified to be Cu(OH)3Cl or atacamite [4], typically grows sub-surface along the polymer glass interface from the anode toward the cathode—eventually causing a bridge and catastrophic failure (a dead short). As the name anodic suggests, the growth must be from the anode, or the failure cannot be called CAF. Additionally, the anode (+) must be clearly identified, and SEM/EDX must be done to confirm that the compound is copper-chloride containing or it CANNOT be called CAF.
This information is based on a significant body of research performed on the CAF failure mechanisms. To reiterate, this was pointed out by one of the experts in this area, and it is important that the reader view the image in Figure 1 (a) and (b). Based on Dr. Caputo’s consultation with me, I have been able to provide more critical information related to CAF, and I’ll share some of his additional comments. He has also provided scholarly peer-reviewed research papers on the subject as references for the reader to gain additional insight on CAF formation.
1. Example of the CAF Failure Mode
Figure 1 (a) shows an optical image with backlight lighting where CAF grew from the anode toward the cathode but did not bridge. Figure 1 (b) shows a cross-section image where SEM was performed. From the SEM image, CAF surrounds the polymer/glass interface (circled in yellow, and red arrows point to the CAF compound) [5–6].
2. The Mechanism for CAF formation
Lando et al. [3] showed that CAF forms via a two-step mechanism. In the first step, the path for CAF formation is created. This step results in the weakening of the polymer/glass interface, which provides the path for the migration of the copper-chloride containing compound (i.e., represented by time = t1). In the second step, moisture provides the aqueous medium for the electrochemical formation of atacamite, which has been identified to be CAF (i.e., represented by time = t2). The rate-limiting step is the creation of the path for CAF to form (t1), which takes much greater time to occur. In summary, time = t1 >> time = t2.”
3. Other ECM or Conductive Failure Type Failure Modes in PWBs
A hollow fiber shown in Figure 2 is a glass defect that can occur during the glass manufacturing process. This defect will be present when the PCB material supplier receives the glass cloth. However, it is not related to the polymer/glass bond and will be present before the manufacturing of PWB cores and pre-pregs; thus, it should not be used as a metric to evaluate the PCB materials CAF performance.
If a hollow fiber is present in the PWB building blocks and is aligned with the drilled hole during the PWB manufacturing process, the hollow fiber will be filled with copper via a capillary action during the plating process, and plating salts will become trapped within the hollow fiber. During temperature-humidity (TH) condition, this will become conductive and result in a drop in insulation resistance, but this does not result in a dead short (i.e., it recovers after a dry out). Also, this type of failure is not to be confused with CAF. Further, to date, no one has shown that any growth from the anode has occurred within a hollow fiber; hence, it would not be appropriate to call a hollow fiber a CAF failure. A hollow fiber failure would be better termed as a conductive path type failure.
The movement to more compact designs has led to finer pitch designs and hence tighter hole wall-hole wall gaps. In these types of designs, when two plated through-holes are inline with each other (like Figure 1 (a)), this can pose reliability concerns if the PWB drilling process is not optimized during PWB manufacturing. In this situation, PWB manufacturers need to take extra care during the hole drilling step, or fracturing of the polymer/glass interface can occur. This can result in plating salts being trapped during the plating process between the holes internal to the PWB, which—when exposed to temperature-humidity conditions with no bias—will become conductive from the moisture absorption, which results in a sudden drop in insulation resistance, and failure. This is not CAF (as CAF requires bias), but rather a conductive path type failure, which will recover upon dry out [7].
Acknowledgment
I would once again like to thank Dr. Antonio Caputo from Intel Corporation for his time and expertise in guiding and helping me better understand the CAF failure mode. This has helped me provide more information on CAF in this follow-up column and will help readers better understand CAF.
References
- P.J. Boddy, R.H. Delaney, J.N. Lahti, and E.F. Landry, 14th Annual Proceedings of Reliability Physics (1976).
- Der Marderosian, Proceedings of IPC fall meeting, San Francisco, California (1976).
- D.J. Lando, J.P. Mitchell, and T.L. Welsher, 17th Annual Proceedings of Reliability Physics (1979).
- W.J. Ready and L.J. Turbini, The Journal of Electronic Materials, 31, 1208 (2002)
- Caputo, Ph.D. Thesis in Materials Science and Engineering, University of Toronto (2010).
- Caputo, A., L.J. Turbini, L.J. et al., The Journal of Electronic Materials, 39, 85 (2010).
- Caputo, L.J. Turbini et al., Microsystem Technologies, 15, 39 (2009).
Michael Carano is VP of technology and business development for RBP Chemical Technology.
More Columns from Trouble in Your Tank
Trouble in Your Tank: Yield Improvement and ReliabilityTrouble in Your Tank: Causes of Plating Voids, Pre-electroless Copper
Trouble in Your Tank: Organic Addition Agents in Electrolytic Copper Plating
Trouble in Your Tank: Interconnect Defect—The Three Degrees of Separation
Trouble in Your Tank: Things You Can Do for Better Wet Process Control
Trouble in Your Tank: Processes to Support IC Substrates and Advanced Packaging, Part 5
Trouble in Your Tank: Materials for PWB Fabrication—Drillability and Metallization
Trouble in Your Tank: Supporting IC Substrates and Advanced Packaging, Part 5