-
- News
- Books
Featured Books
- smt007 Magazine
Latest Issues
Current IssueSupply Chain Strategies
A successful brand is built on strong customer relationships—anchored by a well-orchestrated supply chain at its core. This month, we look at how managing your supply chain directly influences customer perception.
What's Your Sweet Spot?
Are you in a niche that’s growing or shrinking? Is it time to reassess and refocus? We spotlight companies thriving by redefining or reinforcing their niche. What are their insights?
Moving Forward With Confidence
In this issue, we focus on sales and quoting, workforce training, new IPC leadership in the U.S. and Canada, the effects of tariffs, CFX standards, and much more—all designed to provide perspective as you move through the cloud bank of today's shifting economic market.
- Articles
- Columns
- Links
- Media kit
||| MENU - smt007 Magazine
Improving Tech Support During a Pandemic
September 7, 2020 | Nolan Johnson, I-Connect007Estimated reading time: 3 minutes
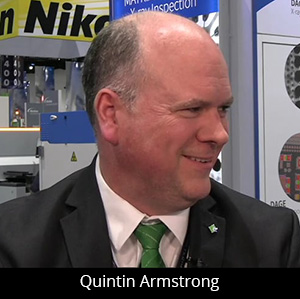
Koh Young’s Quintin Armstrong, senior manager of technical services and applications for the Americas, discusses the work that has been going on at the company around field support, including pre- and post-sales support training, and how those areas have been affected by COVID-19.
Nolan Johnson: Quintin, for those who don’t know you, what’s your role?
Quintin Armstrong: I joined Koh Young in August of 2019. My role is to enhance our organizational procedures and methods in our approach to customer support, as well as to better harmonize our modus operandi throughout our Americas operations. It’s always a continuous improvement type of objective between the various different pieces of the operation, technical services in the field, general support, applications type of activities—both pre- and post-sale—and the demo room type of activities. Some of that would include things like evaluation activities at customer sites, as well as training activities—both in our KYA offices, and at customer sites, or even at representatives’ office sites.
I focus on each of these different areas, tie them all in together, try to unify our support approach, and look at improvement opportunities within the organization. We have offices throughout the Americas, including in the U.S., Mexico, and down through Central America and South America, with the main markets there being Brazil and Argentina. We have a series of reps, and we have a lot of these subsite facilities set up there for the same purposes. It’s about bringing all that together and meeting the overall objective to best serve our customers in every aspect.
Johnson: Given the current situation and the restrictions that accompany it, how do you service the customer differently?
Armstrong: To be honest, it’s not a huge difference in the way that we always have done things. As technology evolves, some of these tools make it easier to do some things more remotely. Those are utilized, and they have been even before the onset of the situation that we have with COVID-19, but we already had a lot of those things in place. And this happened very suddenly. In my case, I went from working in the office on a Friday afternoon to not going into the office the following Monday in March. All of this meant making sudden adjustments. Fortunately, it wasn’t a big change in the way that we had to approach things; we just had to focus solely on the remote support aspect of it.
It’s about utilizing the tools that we’ve had for some time. We have a very good setup with our help-desk arrangement and the incoming tickets. A lot of that support happened via that method. Many people prefer to avoid phone calls and go to a messaging type of system instead. That has always worked very effectively for those needs. Then, there are things like installations, where we basically were doing dedicated support. We’d have a field service engineer assigned to a customer. We use digital aids, and the methods that we have to connect with them, and various documentation sources, supplemental videos, etc., to accomplish those objectives. And tying all those pieces together has helped us meet the various emergency support needs. But we also had some people traveling when it was an absolute necessity for those instances that could only be handled with the on-site support, as may have been appropriate, given the travel challenges and restrictions, and policies adopted by our customers as we all have adjusted to the situation.
To read this entire interview, which appeared in the September 2020 issue of SMT007 Magazine, click here.
Testimonial
"Advertising in PCB007 Magazine has been a great way to showcase our bare board testers to the right audience. The I-Connect007 team makes the process smooth and professional. We’re proud to be featured in such a trusted publication."
Klaus Koziol - atgSuggested Items
Bell to Build X-Plane for Phase 2 of DARPA Speed and Runway Independent Technologies (SPRINT) X-Plane Program
07/09/2025 | Bell Textron Inc.Bell Textron Inc., a Textron Inc. company, has been down-selected for Phase 2 of Defense Advanced Research Projects Agency (DARPA) Speed and Runway Independent Technologies (SPRINT) X-Plane program with the objective to complete design, construction, ground testing and certification of an X-plane demonstrator.
Nolan’s Notes: Moving Forward With Confidence
06/03/2025 | Nolan Johnson -- Column: Nolan's NotesWe’re currently enjoying a revitalized and dynamic EMS provider market with significant growth potential. Since December 2024, the book-to-bill has been extremely strong and growing. Starting with a ratio of 1.24 in December, book-to-bill has continued to accelerate to a 1.41 in April. Yet, there is a global economic restructuring taking place. To say that the back-and-forth with tariffs and trade deals makes for an uncertain market is an understatement. While we may be in a 90-day tariff pause among leading economic nations, the deadline is quickly approaching and that leaves many of you feeling unsettled about what to expect.
Mycronic High Flex Changes Division Name to PCB Assembly Solutions
05/20/2025 | MycronicMycronic AB, the leading Sweden-based electronics assembly solutions provider, announced that its division formerly known as High Flex will now operate under the name PCB Assembly Solutions.
SolderKing Achieves the Prestigious King’s Award for Enterprise in International Trade
05/06/2025 | SolderKingSolderKing Assembly Materials Ltd, a leading British manufacturer of high-performance soldering materials and consumables, has been honoured with a King’s Award for Enterprise, one of the UK’s most respected business honours.
Foxconn's Tiger Leap Combining Nature and Technology in Ecological Roof Garden
04/23/2025 | FoxconnHon Hai Technology Group, the world's largest technology manufacturing and service provider, has actively responded to the United Nations Sustainable Development Goals (SDGs).