-
- News
- Books
Featured Books
- smt007 Magazine
Latest Issues
Current IssueWhat's Your Sweet Spot?
Are you in a niche that’s growing or shrinking? Is it time to reassess and refocus? We spotlight companies thriving by redefining or reinforcing their niche. What are their insights?
Moving Forward With Confidence
In this issue, we focus on sales and quoting, workforce training, new IPC leadership in the U.S. and Canada, the effects of tariffs, CFX standards, and much more—all designed to provide perspective as you move through the cloud bank of today's shifting economic market.
Intelligent Test and Inspection
Are you ready to explore the cutting-edge advancements shaping the electronics manufacturing industry? The May 2025 issue of SMT007 Magazine is packed with insights, innovations, and expert perspectives that you won’t want to miss.
- Articles
- Columns
- Links
- Media kit
||| MENU - smt007 Magazine
Real Time with...SMTAI 2020: Aegis' Ontology Drives Digital Twin Process
September 23, 2020 | Real Time with...SMTAIEstimated reading time: 8 minutes
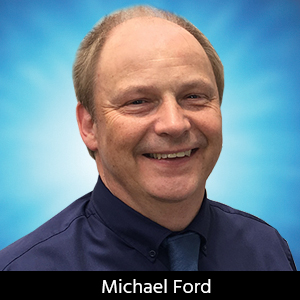
Andy Shaughnessy speaks with Michael Ford, senior director of emerging industry strategy for Aegis Software, about its newest concept—Ontology—which the company will discuss during SMTAI. He also explains how Ontology relates to the company’s existing MES products, as well as how it dovetails with the digital twin process.
View more videos and show-related content at Real Time with… SMTAI 2020 virtual.
Prefer to read the transcript of this interview? Read on...
Andy Shaughnessy: With me this morning is our good friend Michael Ford, the senior director of emerging industry strategy for Aegis. Good to see you, Michael. How’s it going?
Michael Ford: It’s going well, thanks. How are you?
Shaughnessy: Pretty good, considering all that’s been going on this year. How about you?
Ford: Yes. Unbelievably busy, actually. I think the whole industry is settling down, understanding now how to continue within this COVID-19 environment, and so things are really picking up.
Shaughnessy: I know you are going to be doing a big presence at the SMTAI virtual show in a couple of weeks. Tell us what, what do you all have planned for that?
Ford: Yes. What we’ve been seeing over the last few weeks and months is quite an unprecedented upturn in interest in our old friend CFX, the IPC standard for exchanging data between machines. And we did want to have customers lead this. We wanted them to go to machine vendors solution providers to say, “I need to get my data, I need to get my factory connected.” And what we need then to do is step two, which is creating this thing, which we call ontology.
Now, I had to look that word up, I didn’t understand what it meant, but it’s a great word to describe the relationship between things. In the sense of the data, how do you define the way to create value from data? It could be understanding flows and bottlenecks and opportunities. It could be understanding quality information, material information, etc. How do you have a set of rules that enable you to go from data points that just look like random bits of information to actually building the context in which those bits of information took place? And then that starts to describe a particular event or value.
Without the ontology, what you basically get is just the data going from A to B. And you end up with just a load of data, trying to make sense of that at a later time is very difficult. What we bring as part of our FactoryLogix MES is that built-in creation, that built-in ontology that automatically creates the relationships between the data and knows what to do in order to create actions. For example, “When should I order that next replenishment of material? When should I highlight there is a quality problem and maybe stop the process from running?” There are so many different rules that the software, in terms of its algorithms—they used to be called AIs, but I’m calling them algorithms—will process that contextualized data, and then be able to put that contextualized data into a data warehouse, such that customers can interrogate that and very easily, with standard off-the-shelf tools, be able to make their own reports and their own kind of judgment on what’s happening.
Shaughnessy: This fits in with your whole MES plan, basically.
Ford: It really does because I think a lot of the people who are beginning to see this data are thinking, “What on earth am I supposed to do with it?” And it can take a number of years to really start to understand the relationships between causes and events, symptoms, and actions. It is hard actually to put these things together, but we’ve been working now for many years with FactoryLogix where this is part of the value that we create. The data is not just data for data’s sake; it’s actually actionable information, and you have interoperability between all of the different facets around manufacturing. Everybody sees the same thing. They’re all saying stuff they can understand. It’s not just data points in a weird language, which is your value.
Shaughnessy: Right. Now, does this tie in with the whole digital twin? Is it going in that direction? How does that work?
Ford: Yes, it’s an interesting term, isn’t it? Digital twin. If you look online, everybody’s got the digital twin solution. I was developing digital twin solutions in the 1980s, but it wasn’t called digital twin. It was just a computer program that took data in about the physical world and made some decisions in a digital world, which were then actioned back. Digital twin has been out there for many, many, many, many years, but it’s a marketing term now.
Does Aegis have a digital twin? Of course. All software like Aegis FactoryLogix is a digital twin and probably has many, many different types. The other thing I’m talking about at SMTAI is the IPC digital twin because what we wanted to do was instead of having different companies, each with their own proprietary digital twin solution. Those solutions very good, but they only do one thing, and they use a lot of data to do that one thing.
What I wanted to do was enable people to have many uses for their data in the operability, or the ability, to move data around so that many different solutions can use it. For example, you have the data from design. You want to be able to use that for many different purposes in manufacturing. You may want to perform some DFM/DFX checks at the manufacturing sites and then feed that data back to manufacturing. You need to understand every aspect, the digital product model of that design. Plus, you need your digital twin, if you like, of your manufacturing area, as well as your lines, your machines, your robots, your arms, your material flows, and all of these different things. And wouldn’t it be nice that wherever you got the data from, it didn’t matter anymore? You are simply able to drag a product into a manufacturing digital twin, and it started to do all kinds of wonderful calculations for you.
You’re basically able to run digital twin solutions but with one standard set of data. And the digital twin from IPC also stretches out into the market so that I can really get feedback from the market in terms of product reliability, quality, use cases, repairs, RMOs, and RMAs, for example. You can link those then back into the core manufacturing data so that you can really understand the performance of the product in the market against defined use cases.
And I think as people come out of this COVID-19 era, they want to understand more about how products are affecting the environment. We want an understanding of if the recycling was really done against the manufacturing intent and design intent. This is a holistic mechanism for the interoperability of data from design, manufacturing, and out into the market so that if you’re looking at things like recycling, energy consumption, or anything like that associated with the product, you are able to have interoperability of that data. And that’s what’s making the IPC digital twin unique and that nobody else has ever attempted to put all of these different pieces of data together in a way that people can understand.
Shaughnessy: Right. A lot of the big game seems to be in data. We have all this data floating around, and it seems to be a matter of just getting it to where people would have access to it, in the format that they want, where they can use it, take action with it because otherwise, it’s just a bunch of data just swirling around.
Ford: You’re absolutely right. And I hear this in so many different round tables and forums; they say, “Look, we have data, and it’s swirling around. It’s doing all of this stuff, but it’s our data, and we don’t know how to use it. We don’t know how to apply it.” If you have the solution and the correct ontology within the MES system and you’re using IIoT-based infrastructure, you’ve just created the usability of the data and the actionability of the data across the shop floor. With the digital twin, beyond incorporating this design manufacturing and lifecycle, you’re right that it’s a big frustration. And this is why we believe this is so important for people to understand. Data for data’s sake is very limited value, but you to build ontology on top of the connectivity with a solution such as our FactoryLogix solution. Defined over many, many years of experience to use that data, that allows you to drive advanced smart manufacturing. It’s the key to going forward.
Shaughnessy: Right. Is there anything else that we haven’t covered that you’d like to mention?
Ford: I think that’s basically it for now. It’s been very interesting over the last few weeks and months. As I said, people are really beginning to devote some time now to use data and information within the factory, making that factory smart as we come out of this. I think the main thing is going to be, “How do companies become flexible enough to take advantage of business opportunities?” Because as demand changes, we need to make new products. How is manufacturing going to adapt? And I believe that we are seeing this interest in connectivity and ontology as being the way of finding out how to become that highest common factor. They’re not just making more dedicated to one type of product. Now, they can basically do anything at any time, at almost a moment’s notice, because they have that best practice digital solution.
Shaughnessy: Right. That sounds good. We wish you all a good show, and maybe we’ll get to actually see each other at the show eventually and have a pint or two.
Ford: Yes, get a pint of beer. That’s fantastic.
Shaughnessy: It has been a long time—about a year, really—but it seems like years.
Ford: Yes. It seems much longer than it’s been, but it’s going to be even longer. Then, we’ll get a chance.