Additive Electronics TechXchange: NSWC Crane and Lockheed Martin Presentations
October 27, 2020 | Happy Holden, I-Connect007Estimated reading time: 2 minutes
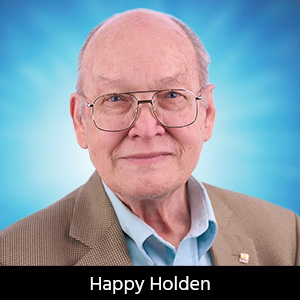
The Additive Electronics TechXchange this year was a virtual event. One presentation, “Very High-Density Investigation Project,” was given by Steve Vetter of the NSWC Crane Naval Facility in Crane, Indiana.
Crane is a very large Naval Surface Warfare Center created in WWII to be as far from the ocean as possible. It is now a research, storage, and test facility for the DoD. Fortunately, they have a state-of-the-art PCB facility to support interconnect devices for the DoD. Their role is also to support technology development and transition efforts for the DoD (Figure 1).
Steve reported on a new Project at Crane: the S2MARTS VHDI Project (Strategic and Spectrum Missions Resilient Trusted Systems) awarded to them in 2019. The project has four phases that will run over a number of years. The purpose of this program is to show its application to DoD projects and to provide the U.S. public with results and technical advice.
Steve detailed the process of using a proprietary SAP process—first on inner layers, and then on multilayers with through-holes and blind vias. Imaging was performed on a new MIVA LED direct image system with 10-micron resolution. Resist developing, plating, and differential etch processes were modified.
A special multilayer test vehicle was designed to test the performance to the 25-µm and 12-µm geometries. Conclusions and lessons learned from Phase 1 were presented.
Steve finished by outlining plans for Phase 3, the “Embedded Latent Catalyst process (ELCAT)” for 20-micron features and embedded die (SIP).
Figure 1: NSWC Crane’s printed circuit facility.
The next presentation was “Electronics Additive Manufacturing for Defense and Space” by Kourtney Wright, Ph.D., of Lockheed Martin Advanced Technology Center.
Dr. Wright gave a short introduction of the Advanced Technology Center, and about the roles Lockheed Martin performs. She explained “Why Additive for Space and Defense,” including:
- Distributed manufacturing in-field, repair, and anywhere
- Lower sustainment cost leading to lower program costs
- Lower deployment cost for spare parts/units and quicker diagnostics
Their current focus is on copper inks, additive RF structures, flex circuits, and circuit re-engineering:
- Copper Inks: They have developed a large-scale manufacture of nanocopper inks that sinter at 200C to form high electrical conductivity and is solderable
- Flex Circuits: Using the new nanocopper inks on flex circuits and printed antennas
- RF Structures: Printing on complex 3D substrates and to trim designs for superior performance (Figure 2)
- Circuit Re-Engineering: Testing the new nanocopper inks for additive jumper wires to re-engineer a complex board.
Kourtney then provided some insight on issues for adhesion of the new inks and repeatability of print parameters. She concluded with some final thoughts on the future of additive technologies for space and defense use.
Figure 2: Lockheed Martin’s Advanced Technology Center printed antennas.
Suggested Items
RF PCB Design Tips and Tricks
05/08/2025 | Cherie Litson, EPTAC MIT CID/CID+There are many great books, videos, and information online about designing PCBs for RF circuits. A few of my favorite RF sources are Hans Rosenberg, Stephen Chavez, and Rick Hartley, but there are many more. These PCB design engineers have a very good perspective on what it takes to take an RF design from schematic concept to PCB layout.
Trouble in Your Tank: Causes of Plating Voids, Pre-electroless Copper
05/09/2025 | Michael Carano -- Column: Trouble in Your TankIn the business of printed circuit fabrication, yield-reducing and costly defects can easily catch even the most seasoned engineers and production personnel off guard. In this month’s column, I’ll investigate copper plating voids with their genesis in the pre-plating process steps.
Elephantech: For a Greener Tomorrow
04/16/2025 | Marcy LaRont, PCB007 MagazineNobuhiko Okamoto is the global sales and marketing manager for Elephantech Inc., a Japanese startup with a vision to make electronics more sustainable. The company is developing a metal inkjet technology that can print directly on the substrate and then give it a copper thickness by plating. In this interview, he discusses this novel technology's environmental advantages, as well as its potential benefits for the PCB manufacturing and semiconductor packaging segments.
Trouble in Your Tank: Organic Addition Agents in Electrolytic Copper Plating
04/15/2025 | Michael Carano -- Column: Trouble in Your TankThere are numerous factors at play in the science of electroplating or, as most often called, electrolytic plating. One critical element is the use of organic addition agents and their role in copper plating. The function and use of these chemical compounds will be explored in more detail.
IDTechEx Highlights Recyclable Materials for PCBs
04/10/2025 | IDTechExConventional printed circuit board (PCB) manufacturing is wasteful, harmful to the environment and energy intensive. This can be mitigated by the implementation of new recyclable materials and technologies, which have the potential to revolutionize electronics manufacturing.