-
- News
- Books
Featured Books
- pcb007 Magazine
Latest Issues
Current IssueIn Pursuit of Perfection: Defect Reduction
For bare PCB board fabrication, defect reduction is a critical aspect of a company's bottom line profitability. In this issue, we examine how imaging, etching, and plating processes can provide information and insight into reducing defects and increasing yields.
Voices of the Industry
We take the pulse of the PCB industry by sharing insights from leading fabricators and suppliers in this month's issue. We've gathered their thoughts on the new U.S. administration, spending, the war in Ukraine, and their most pressing needs. It’s an eye-opening and enlightening look behind the curtain.
The Essential Guide to Surface Finishes
We go back to basics this month with a recount of a little history, and look forward to addressing the many challenges that high density, high frequency, adhesion, SI, and corrosion concerns for harsh environments bring to the fore. We compare and contrast surface finishes by type and application, take a hard look at the many iterations of gold plating, and address palladium as a surface finish.
- Articles
- Columns
Search Console
- Links
- Media kit
||| MENU - pcb007 Magazine
Estimated reading time: 4 minutes
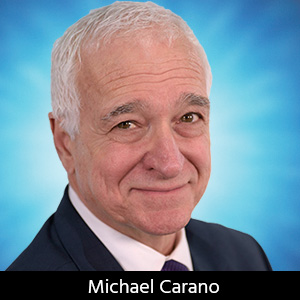
Contact Columnist Form
Trouble in Your Tank: A Process Engineer’s Guide to Final Etching, Part 1
Introduction
Sure, etching of copper foil has been in existence since before through-holes were mechanically drilled. However, as circuit density has evolved into finer and finer lines and spaces, the mechanical and chemical aspects of etching copper have evolved as well. The purpose of this edition of “Trouble in Your Tank” is to provide an overview of the inner layer and outer layer etching processes. This will include chemical and mechanical aspects of each process, different chemical formulations involved, and other unique aspects of each.
The Etching Process
Most process problems that appear during the etching stage of printed circuit production can be traced to one of two general areas. The most common and obvious cause of etching problems is the etching equipment itself, either through equipment malfunctioning or other issues, such as temperature controls and specific gravity measurement malfunction.
The second most common cause of problems during the etching step are issues that occur during prior processing steps but are not detected until the boards are processed through the etcher. An example would be resist scum left on the board during the stripping of a plating resist, which can cause uneven etching to occur. Or the defect—such as excessive undercut, resist lifting, darkening, or etch-out of the tin etch resist—can be attributed to chemical factors (pH control, operating temperature) or other parameters, such as surface preparation, handling, and exposure/development of the photoresist.
Here, I will outline some of the problems that can occur during the etching process with the most probable cause(s) and actions that can be taken to correct them. When the cause of a problem can be traced to a prior process step, it will be noted as such, and the reader directed to the appropriate section if necessary.
This column is organized by etching chemistries. The first subsection deals with general problems that can be encountered with any chemistry used for etching and should be referred to first. The following subsections cover the problems relating to bath control, over-etching, under-etching, and residues left on the board surface and will be covered in a future column.
Main Types of Etching Chemistries
Depending on the unit operation (inner layer or outer layer etching), the fabricator has the option of using cupric chloride (acid-based) or alkaline ammoniacal etching. In general, the former is used on inner layers, and the latter is primarily used as an etchant when metallic etch resists are protecting the underlying circuity. And with some adjustments, alkaline ammoniated etchants are employed on inner layers. Consequently, the fabricator must consider the compatibility of the photoresist with each of the etching chemistries.
Recognizing these different chemistries, there are several common issues related to these etchants that are worth covering here.
Effects From Equipment and Other Processes
Since etching is best performed in conveyorized equipment, the etching machine plays a significant role in the quality of the finished product. One very common issue leading to non-conformity is non-uniform etching of the copper from the panel (side to side). Table 1 lists the possible causes for non-uniform etch and suggested remedies to correct the issue.
Table 1: Possible causes for non-uniform etch and suggested remedies to correct the issue. (Source: RBP Chemical Technology)
Spray nozzles will plug with debris over time. In addition, these nozzles, after repeated use, begin to wear out. Pressure drops are completely bothersome as this reduces the etching chemistry solution flow to the board. In addition, check pressure gauges regularly. An unexpected drop in pressure may indicate blocked nozzles or issues with filters plugging.
Another interesting issue that is equipment- and process-related (not the etching chemistry, however) is non-uniform etching. Basically, some areas of the panels are completely etched, while others show copper. Here, this is a good exercise in reviewing other processes involved in fabrication. An example of the unetched copper is shown in Figure 1. Essentially, copper is visible in some areas of the panels after etching.
There are several possibilities that explain why copper could remain on the panels after etching. And while etching chemistry options will be explored in Part 2 of “Trouble in Your Tank: A Process Engineer’s Guide to Final Etching,” the main focus for this column is not on chemical process issues.
As written previously, there are several other causes of unetched copper that can find their genesis in the imaging/developing process steps of PWB fabrication. The remaining copper is usually random and manifests itself as copper spots or even somewhat larger (Figure 2).
In this case, one must review several areas prior to final etching. This includes the following:
- Developer control in terms of pH and resist loading
- Moisture or oxidation on the panel prior to resist lamination
- Breakpoint in the developer needs to be adjusted
- Overexposure, leading to partial polymerization of the resist where none was desired
- Excessive hold times between resist lamination and exposure and between lamination and development
Again, as the engineer responsible for this process, do not underestimate the influence of up and downstream processes. The defect or defects that are visible after a particular process step may have their origins several process steps earlier.
This column originally appeared in the November 2020 issue of PCB007 Magazine.
More Columns from Trouble in Your Tank
Trouble in Your Tank: Yield Improvement and ReliabilityTrouble in Your Tank: Causes of Plating Voids, Pre-electroless Copper
Trouble in Your Tank: Organic Addition Agents in Electrolytic Copper Plating
Trouble in Your Tank: Interconnect Defect—The Three Degrees of Separation
Trouble in Your Tank: Things You Can Do for Better Wet Process Control
Trouble in Your Tank: Processes to Support IC Substrates and Advanced Packaging, Part 5
Trouble in Your Tank: Materials for PWB Fabrication—Drillability and Metallization
Trouble in Your Tank: Supporting IC Substrates and Advanced Packaging, Part 5